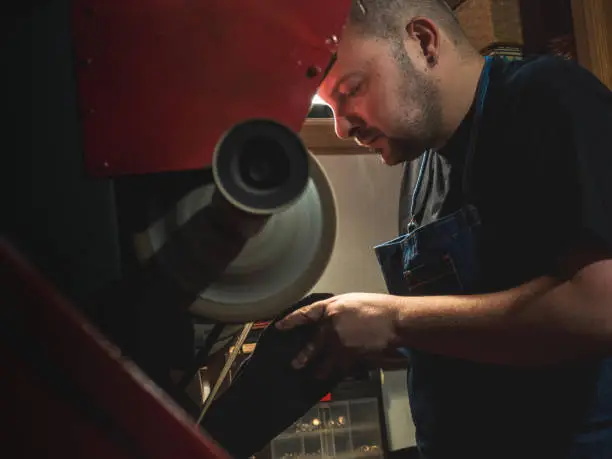
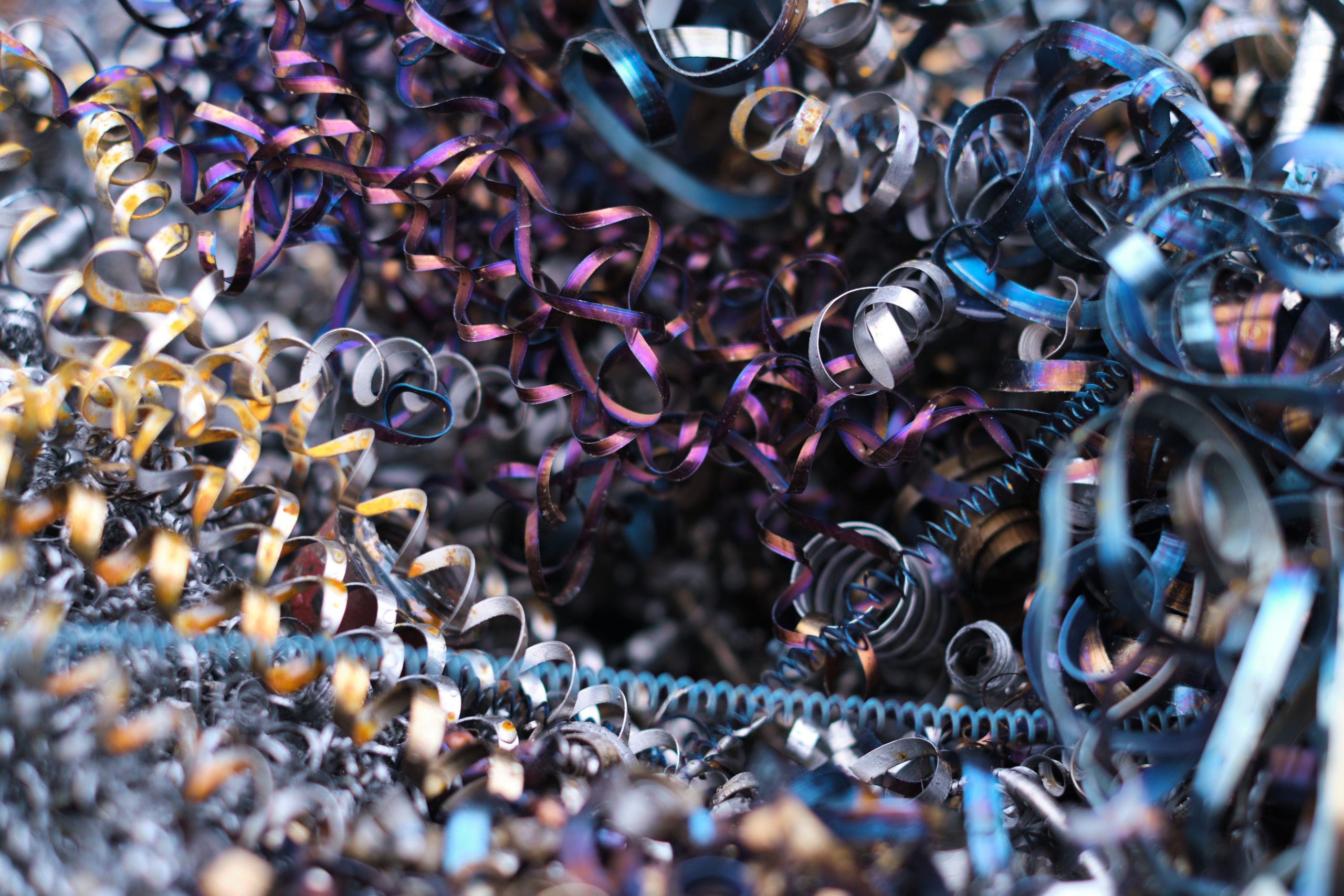
Understanding the Different Materials Used in Metal Spinning
Metal spinning is a specialised manufacturing process that shapes flat metal discs or tubes into cylindrical or conical forms using rotational force. Unlike other metal forming techniques, spinning does not remove material but instead reshapes it, making it highly efficient and cost-effective. This method sees wide use across industries such as aerospace, automotive, lighting, and consumer goods, where precision and durability are essential.
The choice of material in metal spinning significantly influences the final product’s strength, longevity, and functionality. Different metals offer unique properties, such as corrosion resistance, electrical conductivity, or lightweight strength, making them suitable for specific applications. Selecting the right metal ensures optimal performance, ease of forming, and cost-effectiveness.
In this article, we explore the key materials used in metal spinning. By understanding their distinct properties, manufacturers can make informed decisions to enhance final product quality and production efficiency.
Aluminium: Lightweight and Versatile
Aluminium is one of the most widely used metals in spinning due to its excellent workability and natural resistance to corrosion. Its low weight makes it an essential material for industries requiring strength without unnecessary bulk. For example, in aerospace, aluminium is prized for its ability to provide structural integrity without adding significant weight. At the same time, in automotive manufacturing, it contributes to fuel efficiency by reducing overall vehicle mass. Aluminium is also widely used in lighting fixtures, cookware, and food storage containers due to its aesthetic appeal and non-reactive properties.
The metal’s ability to form an oxide layer provides an additional protective barrier against environmental exposure. Certain aluminium alloys, such as 1100 and 3003, offer superior formability, making them ideal for deep drawing and spinning processes.
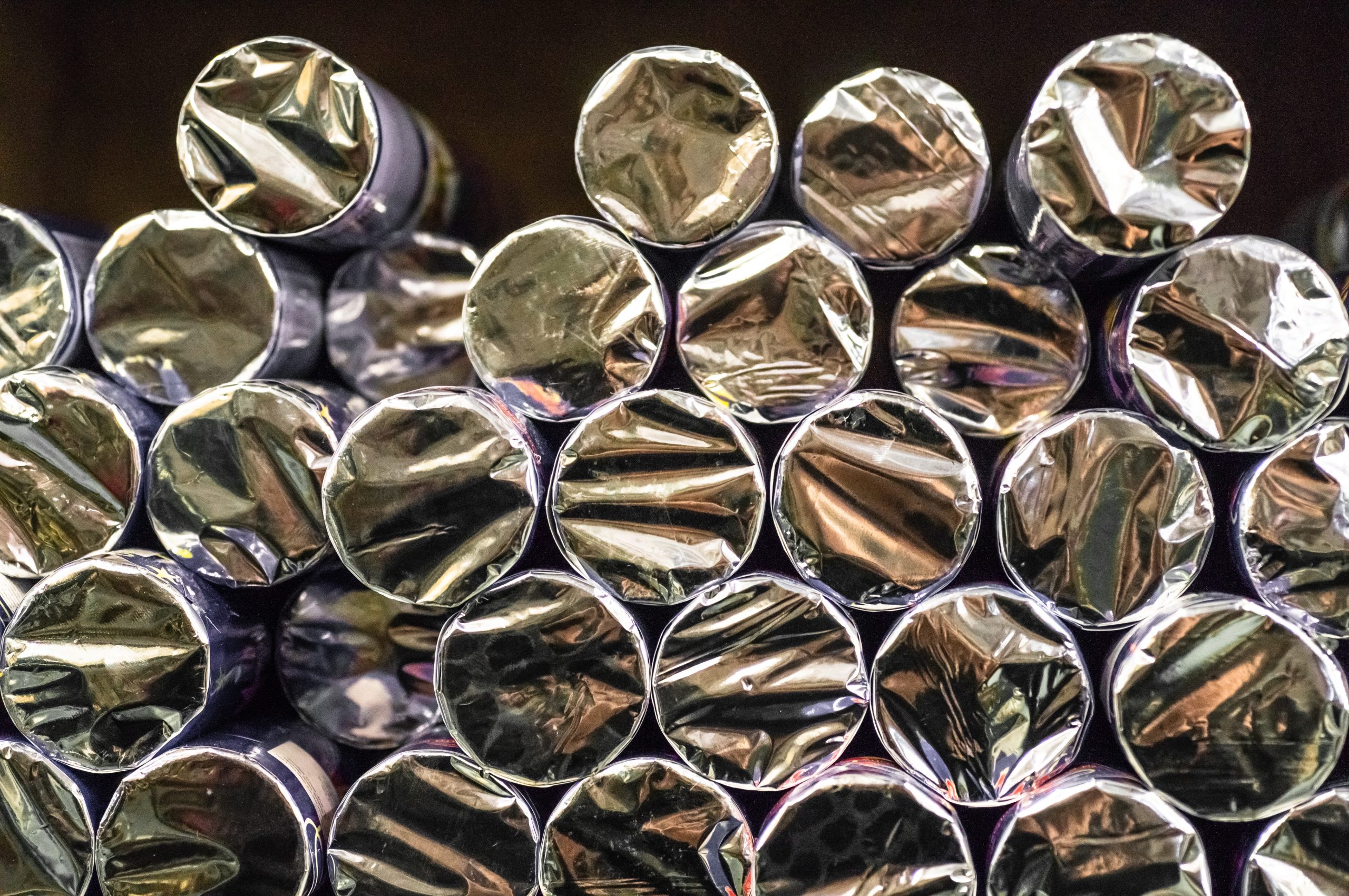
Stainless Steel: Strength and Durability
For applications that demand strength and longevity, stainless steel is an excellent choice. It is commonly used in industries where hygiene, corrosion resistance, and durability are key factors. Food processing equipment, medical tools, and automotive components all benefit from the exceptional properties of stainless steel. The material resists deformation under high stress, ensuring it maintains its integrity even in extreme environments.
Stainless steel’s resistance to rust and oxidation makes it ideal for applications that require longevity, particularly in wet or harsh environments. Common grades such as 304 and 316 are popular choices in spinning due to their excellent corrosion resistance.
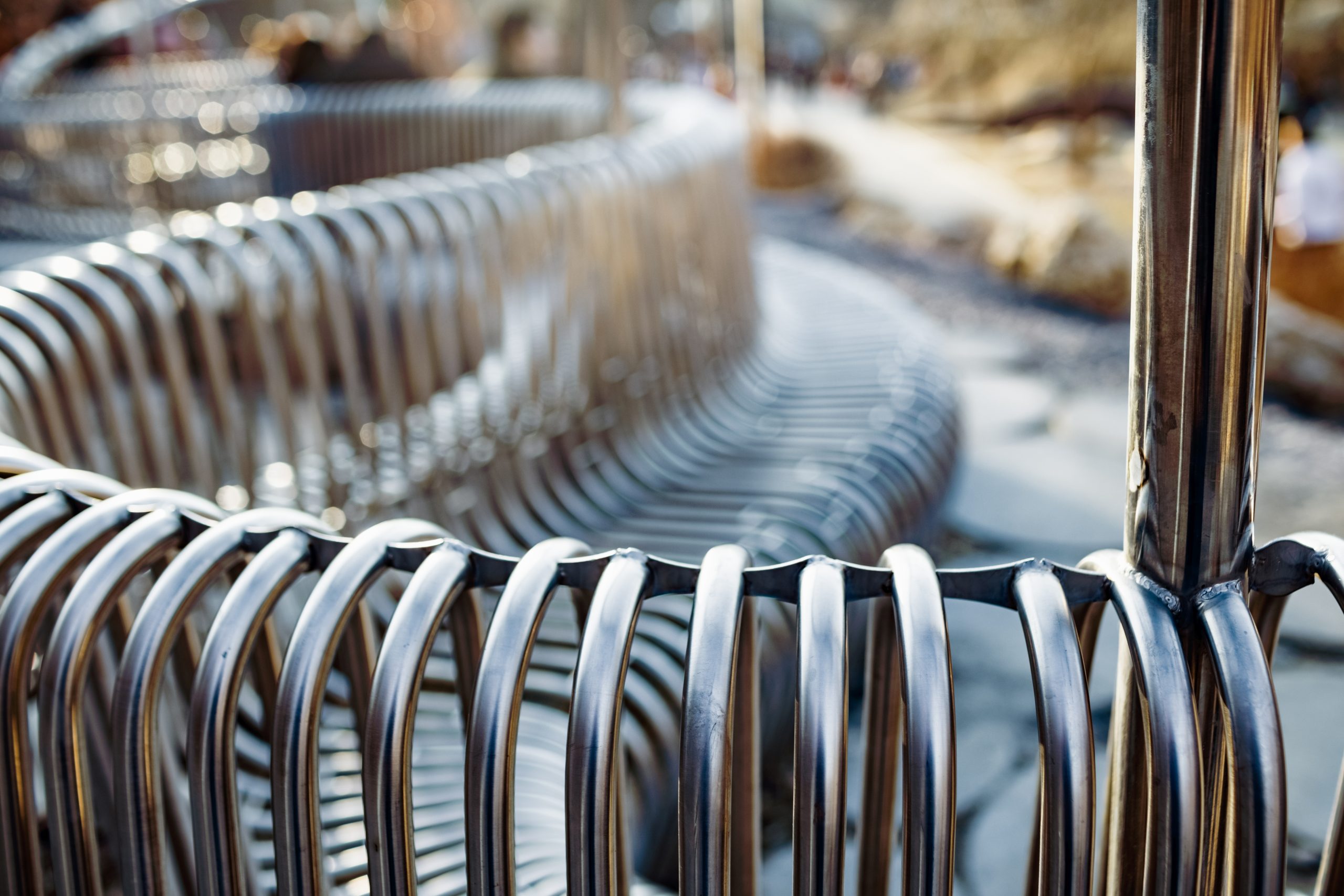
Copper: Aesthetic and Conductive
Copper is often selected for metal spinning when superior conductivity or an attractive visual finish is required. Its excellent thermal and electrical conductivity make it a perfect material for electrical components, heating systems, and architectural features. In addition, copper’s antimicrobial properties make it an ideal choice for food and medical applications where hygiene is a priority.
The rich, natural patina that copper develops over time enhances its visual appeal, making it a sought-after material for decorative installations, watch cases, high-end cookware, and luxury lighting fixtures.
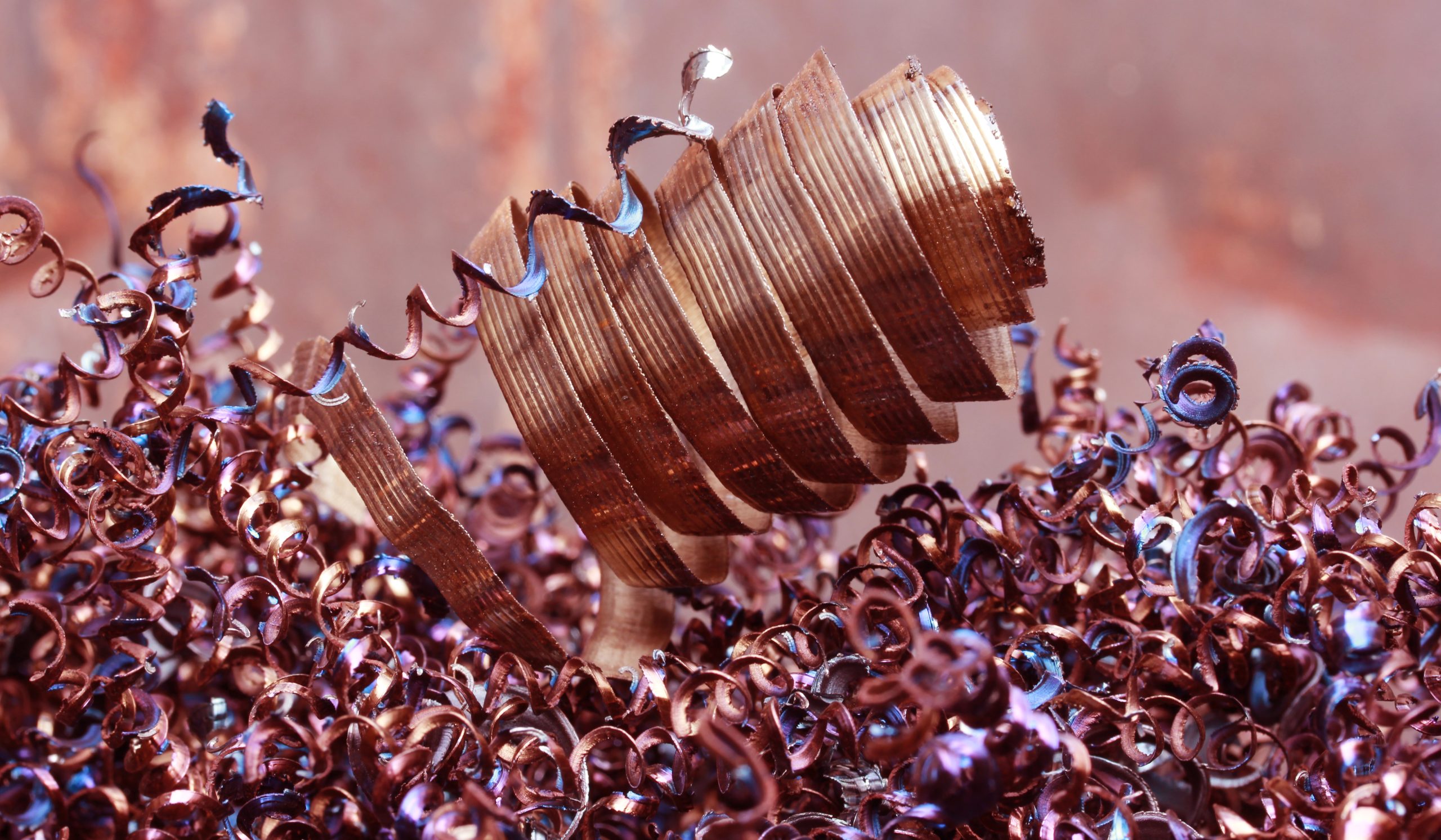
Other Notable Metals in Metal Spinning
Beyond aluminium, stainless steel, and copper, other metals also play an important role in metal spinning.
- Brass: an alloy of copper and zinc, provides an excellent balance of strength and formability, making it a popular choice for decorative applications and musical instruments.
- Mild steel: a cost-effective option used in industrial and automotive manufacturing, where durability is essential.
- Titanium: known for its exceptional strength-to-weight ratio, is used in high-performance aerospace and medical applications, though it requires specialised spinning techniques due to its hardness.
- Magnesium: one of the lightest structural metals, is used in industries where weight reduction is crucial, although it is more challenging to spin due to its brittleness.
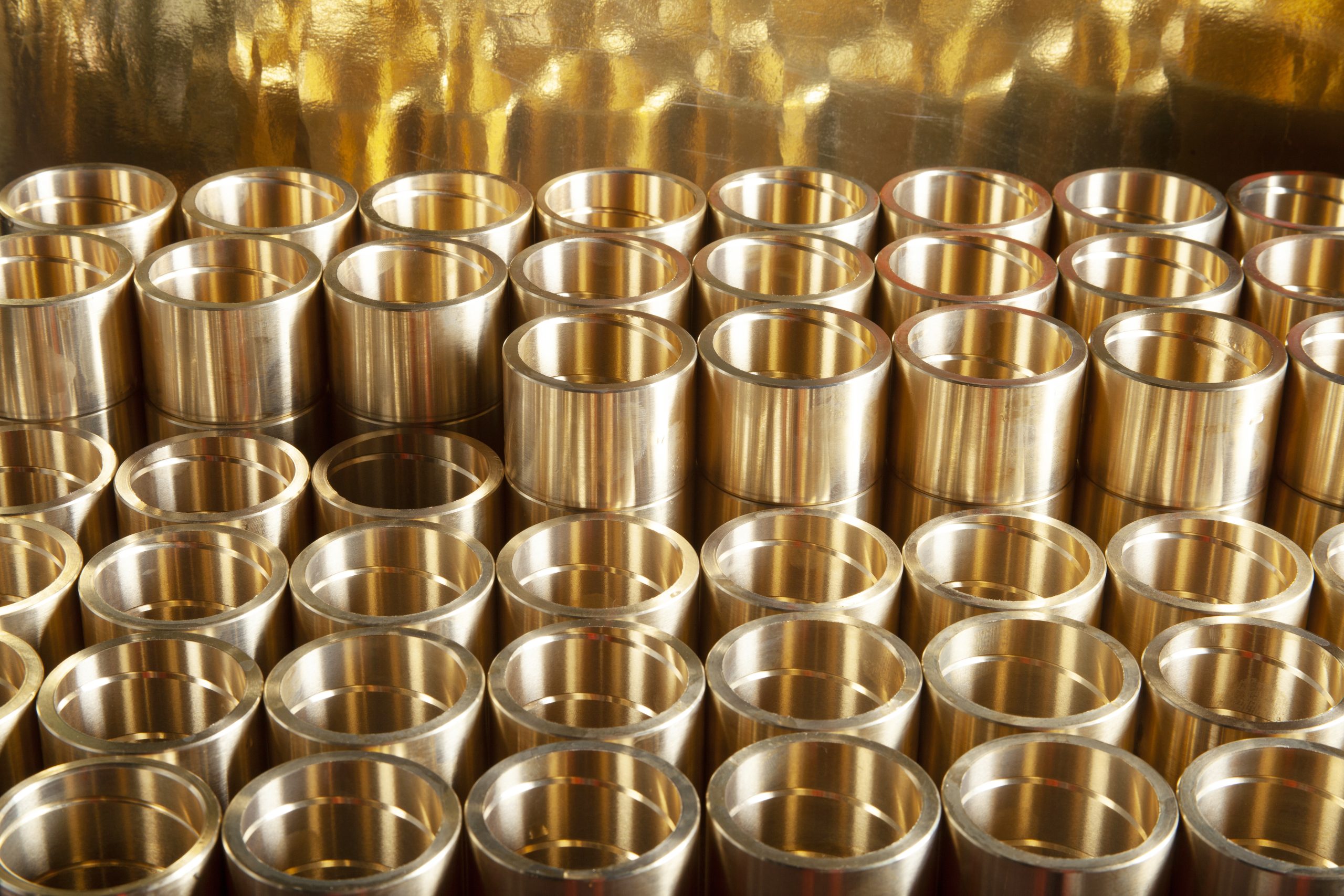
Choosing the Right Metal for Your Project
Selecting the appropriate metal for a spinning project depends on several key considerations. The intended use of the final product will determine the necessary balance between strength, weight, and resistance to environmental factors. Workability is also important, as some metals, such as aluminium, can be shaped easily, while others, like stainless steel, require greater force and precision. Finally, post-processing requirements, such as heat treatments or coatings, may influence material selection to ensure optimal performance. The table below details common industry and application uses of each material.
Metal | Core Industries | Preferred Applications |
Aluminium | Aerospace, Automotive, Lighting | Lightweight structures, reflectors, cookware |
Stainless Steel | Medical, Food Processing, Industrial | Surgical instruments, sanitary equipment, automotive parts |
Copper | Electrical, Architecture, Consumer Goods | Conductive components, decorative elements, cookware |
Brass | Musical Instruments, Decorative Hardware | High-end fixtures, artistic designs, precision components |
Mild Steel | Automotive, Heavy Industry | Structural components, machinery, industrial equipment |
Titanium | Aerospace, Medical | High-strength, lightweight applications, prosthetics |
Magnesium | Aerospace, High-Performance Engineering | Lightweight structural components, performance parts |
Optimising Your Metal Spinning Projects
Metal spinning is a crucial part of modern manufacturing, enabling the creation of precise, durable, and high-performance components across various industries. Selecting the right material ensures that projects meet their design and functional requirements while optimising production efficiency.
At Tanfield Metal Spinners, we bring decades of expertise working with a diverse range of metals, ensuring high-quality results for every project. Whether you’re developing aerospace components, medical instruments, or decorative finishes, our team is here to support your metal spinning needs with precision and care.
Contact us today to discuss your next project and discover how we can help you achieve the perfect balance of form and function.