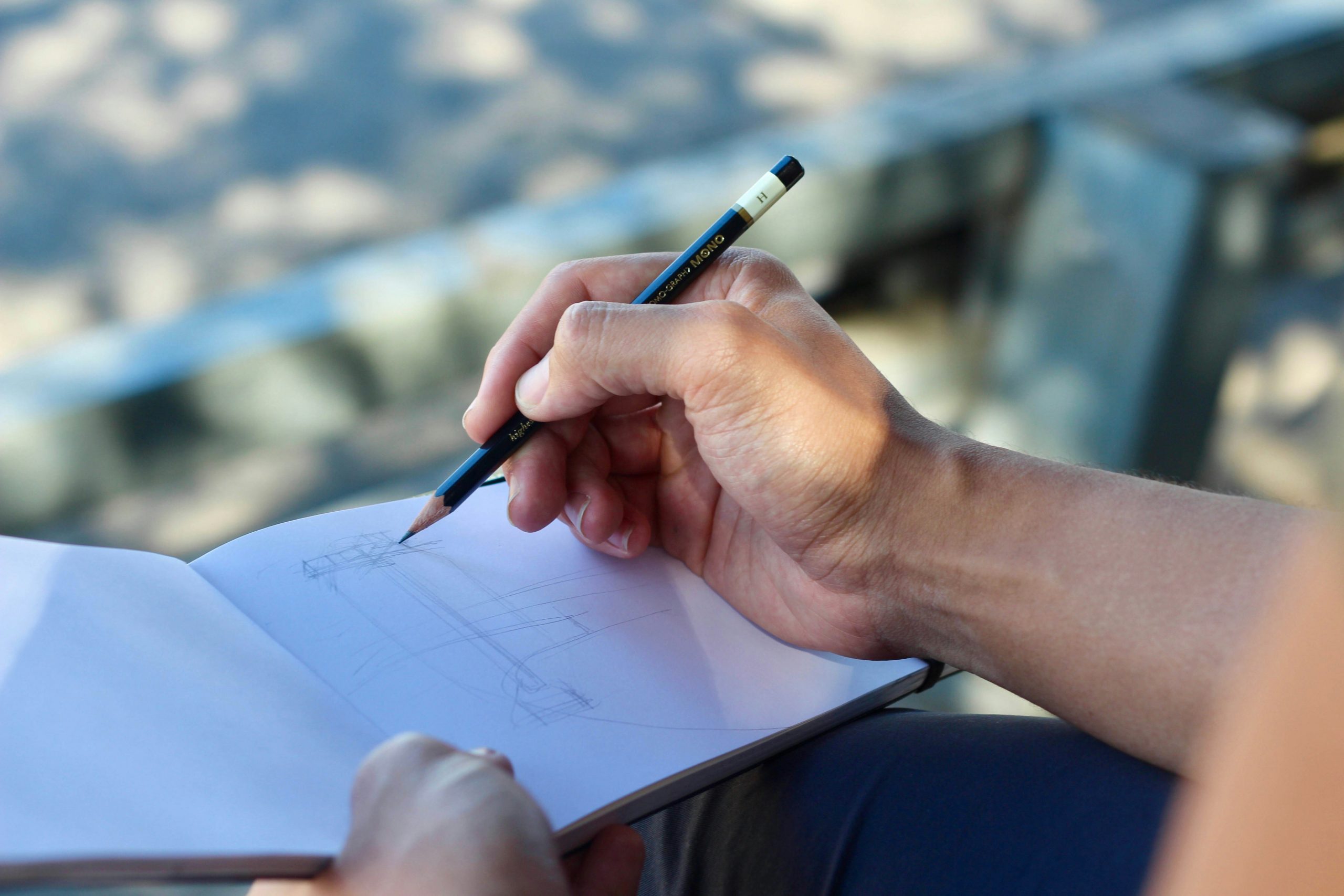
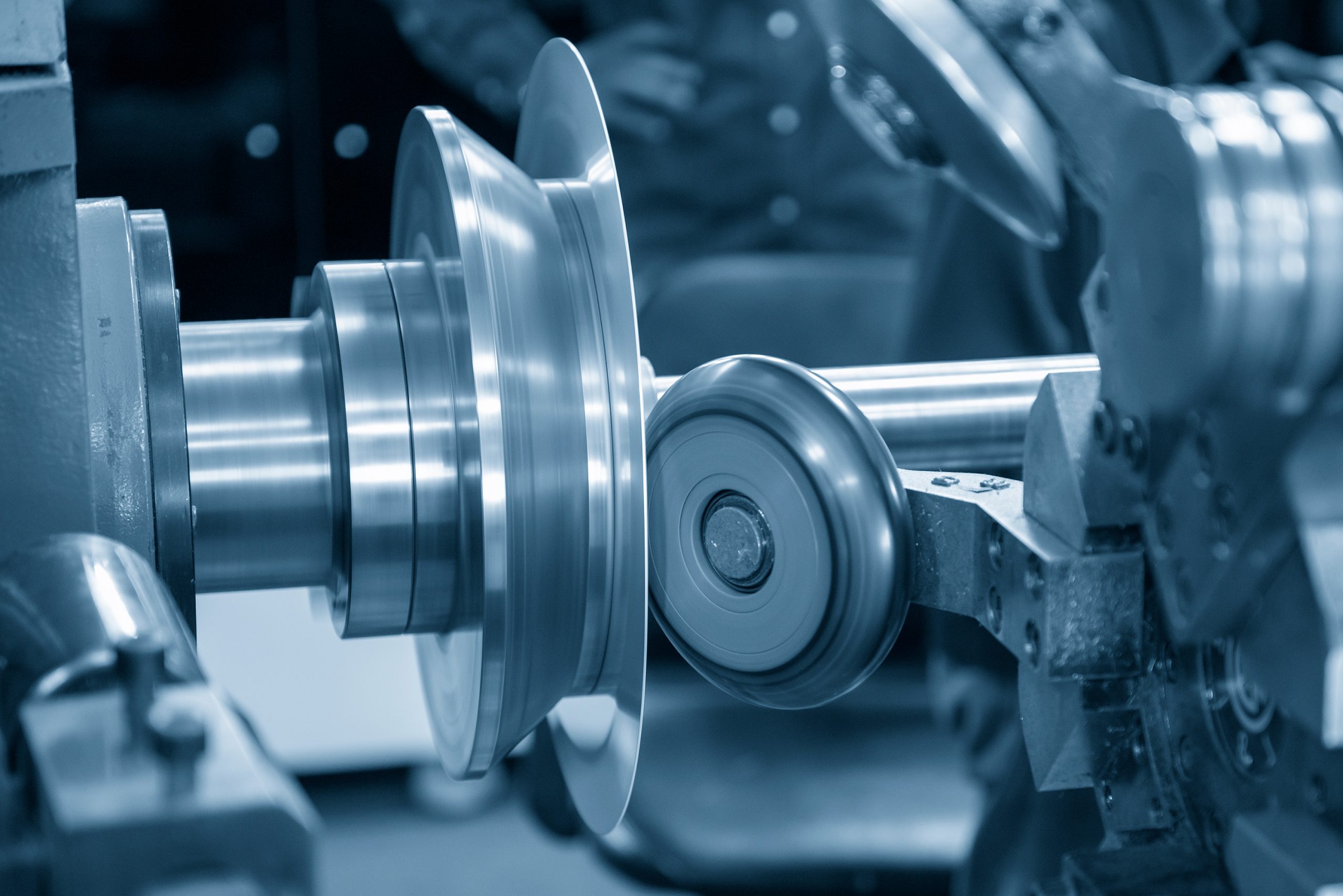
What is the metal spinning process?
Metal spinning is a highly efficient and accurate process for creating symmetrical metal parts that can be used for a wide range of purposes. Also, as this process can be repeatable with PNC or CNC machines, it pays to know exactly how it works and what steps are involved. Metal spinning stands above many other forms of fabrication for these reasons, but many people don’t know what’s involved in the process, so they assume it isn’t for them.
The information in this blog is designed to provide an in-depth detailing of the metal spinning process used by experts in the field.
How is metal spinning done?
Metal spinning is a forming process that shapes a sheet of metal over a die or tool. The metal takes on the shape of the die as force is exerted on it. As such, this piece is intentionally designed to certain dimensions and specifications depending on the part that’s being made. Metal spinning can be performed manually by an experienced metal spinner, or through automated PNC / CNC (Computer Numerical Control) technology. Metal spinning lathe machines feature the following parts:
- Headstock – contains the main mechanism responsible for controlling the spin rpm and driving the spindles. It also supports the spindle and has the tool mounted on it.
- Spindle – a shaft on the headstock that rotates the tool during forming. A second spindle is located on the tailstock which mounts the follower.
- Tailstock – located to the far end of the headstock, used to pressurise the backplate
- Backplate – a changeable pressure pad that secures the workpiece in place during forming. The base of the follower therefore corresponds to the base of the finished part.
- Lathe Bed – structure that supports all the metal spinning machine components.
- Roller – a rigid tool to apply localised force to the workpiece. The roller design should reduce friction by spinning freely throughout the process.
- Centraliser – Used to centre circled metal spinning that has no hole.
- Cutter – used to trim the finished product, in cycle
The metal spinning process explained
While there can be variations on the metal spinning process, along with different processes that take place after spinning. Examples include swaging and finishing, both of which can see use when creating popular metal spun parts such as pressure vessels.
Metal spinning can be used to form parts from a wide range of materials. These include Mild Steel, Aluminium, Stainless Steel (along with many of its variations), Titanium, and more. The properties of these metals will dictate why they are the best choice for the project in question. Our team uses their extensive materials knowledge to make this selection.
The sheet of metal is then cut into a piece of a size that’s needed to make the part required. Each sheet will therefore be able to produce a set number of parts depending on what the size specifications are. At Tanfield, we’ll advise you on the order that will provide the greatest return on investment, so you get the maximum benefit from the process.
The Circle from the sheet metal is affixed to the lathe, which begins to spin. A spinning roller, operated by either machinery or an expert, then passes over the metal to form it against the tool. Multiple passes are typically used to get the metal to take on the exact shape. During this stage, the starting thickness of the metal changes. Metal spinners have a calculation for this based on the shape and size. They will advise on the finishing thickness and can change the starting thickness to achieve if a minimum is required (generally for pressurised parts). In addition, as the shape is changed due to compressive force, the strength and performance of the part can be increased as a result of spinning.
Once the part has been spun according to its specifications and we are happy that it meets the needs of your project, the part is removed from the tool. It will then be stored, ready to subject to other forming processes or transported to the client. By inputting the specifications to the machine, the same part can be spun over and over, using the same process.
If you want more detail on what can be achieved through metal spinning, you can read about our metal spun parts for various industries.
Professional metal spinning for large scale projects
Tanfield Metal Spinners are experienced metal spinners that have been assisting manufacturing and engineering businesses for over 40 years. The range of tools we have in stock is the largest for metal spinning in Europe. This means we can reduce the costs of the spinning process for your project, especially if it requires large bulk orders, without compromising on quality. Our metal spinners are fully qualified and can repeat the same level of precision perfectly. They are also trained to operate modern metal spinning machines to maximise efficiency. Get in touch via talktoanexpert@metal-spinners.com or through 0191 4193377 to get a fast quote.