Bespoke Metal Spinning
Our Custom Metal Spinning Process
Tanfield’s bespoke metal spinning process starts with a thorough debrief of the initial design. This allows us to allocate our resources accordingly and ensure your project work follows quality control measures and all relevant regulations.
The design then changes hands to our expert metal spinning team. The Tanfield metal spinning process can then be followed to our typical level of quality and control.
If you don’t have a drawing, our technical engineering department will supply a drawing upon your request for a quote, at no additional cost. This drawing can be signed off before placing an order.
Bespoke Metal Spinning Applications
As commercial metal spinners, we aim to meet our customer’s needs no matter the sector. Tanfield Metal Spinners can shape a variety of bespoke metal spun components and parts with wide ranging applications.
Let’s say you need bespoke metal work for a dynamic industry such as Cryogenics. Our highly trained and experienced spinners can execute your designs with precision. In addition, we often shape bespoke metal spun products for safety, agriculture, air movement, playground, and food industry businesses.
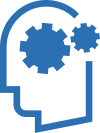
Expertise
We believe that collaboration is key! That’s why we work closely with you to ensure that we provide solutions tailored to your unique needs and requirements.
No drawing? No problem, our expert team will provide one free of charge.

Flexibility
Since 1984 we’ve built an enviable first-class reputation based on the highest quality workmanship with the best advice available on metal thickness and tolerance levels.
We have an open-minded approach to satisfying our customers engineering needs.

Responsive
We pride ourselves on deeply understanding our customers’ needs quickly and effectively. 90% of our quotes are provided within 24 hours.
We take great pride in our excellent on time deliver performance, helping our customers projects run on time, every time.
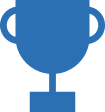
Competitive
With our large range of fully automatic spinning lathes, in our 35,000 sq-ft facility, you can be assured of receiving the best solution for your application, along with the very best lifetime value.
We are very proud to say we are a 100% ‘made in Great Britain’ manufacturer.
Top things we get asked
Bespoke metal spinning is the custom manufacturing of metal by spinning sheet metal into specific shapes tailored to client needs. Tanfield adapts to your project’s exact specifications. You have access to metal spinning services that are entirely unique to your organisation and purpose, when you work with our team. We use our expertise to consider which materials and processes will produce the best results for your project.
The following materials can all be spun. If your project requires a different metal, we can work with many more specialist materials. Tanfield has the capabilities necessary to perform and make adjustments in our metal spinning process to accommodate a wide range of materials including:
- Aluminium
- Brass
- Carbon Steel
- Copper
- Corten
- Duplex
- Hastelloy Alloys
- Inconel
- Mu-metal
- Nimonic
- Nirosta
- Silver
- Stainless Steel
- Titanium
- Zintec
Tanfield serves a variety of industries that require high-quality, precise metal fabrication. These include sectors such as agriculture, air movement, renewable energy, safety, pressure vessels, food industry, and playground. Tanfield offers versatile services, including metal spinning, swaging, and machining, to meet the range of needs of each sector.
There is a great deal of flexibility when it comes to what can be achieved with metal finishings. Tanfield offers the finishings:
- Polishing
- Electropolish
- Anodising
- Pickling & Passivating
Our metal spinners might recommend a certain type of finishing be applied to your metal spun parts. Although this will add time and a slight extra expense, this is done solely to help you get the best outcome for your project. Equally, we won’t be afraid to tell you when using a metal polisher is unnecessary.
Tanfield Metal spinners will quote for work up to a radius of 2.4 meters and material thickness of up to 10mm. For projects that require anything above contact us.
If you do not have a drawing, our technical engineering department will supply a drawing upon your request for a quote, at no additional cost. This drawing can be signed off before placing an order.