Expert Metal Swaging Services
Our Metal Swaging Process
Our swaging process utilises cold forming and compressive force to shape functional metal products. A cutting edge Tanfield sheet metal swaging machine forces the workpiece through a die, which is responsible for the shape the metal takes on. Secondary passes with different dies can be used to shape the workpiece further.
At Tanfield, we pride ourselves on being flexible. As such, our customers can expect us to provide expert advice before and during metal forming processes such as swaging. Our knowledge allows us to provide recommendations in relation to metal thickness and tolerance levels.
What Metal Swaging Can Do For You
Our metal swaging process can be used to form complex shapes and contours in metal tubing, rods, and wires. As a result, sheet metal swaging can have applications in air movement systems, playground apparatus, and manufacturing machine components, as a few examples.
Furthermore, we use metal swaging to reduce the diameter of a workpiece, create tapers or flares, or produce irregular shapes. We recognise that these features are often difficult to achieve through other metalworking processes. Therefore, our metal swaging services ensure Tanfield can meet your needs.
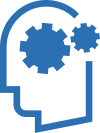
Expertise
We believe that collaboration is key! That’s why we work closely with you to ensure that we provide solutions tailored to your unique needs and requirements.
No drawing? No problem, our expert team will provide one free of charge.

Flexibility
Since 1984 we’ve built an enviable first-class reputation based on the highest quality workmanship with the best advice available on metal thickness and tolerance levels.
We have an open-minded approach to satisfying our customers engineering needs.

Responsive
We pride ourselves on deeply understanding our customers’ needs quickly and effectively. 90% of our quotes are provided within 24 hours.
We take great pride in our excellent on time deliver performance, helping our customers projects run on time, every time.
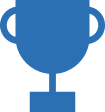
Competitive
With our large range of fully automatic spinning lathes, in our 35,000 sq-ft facility, you can be assured of receiving the best solution for your application, along with the very best lifetime value.
We are very proud to say we are a 100% ‘made in Great Britain’ manufacturer.
Top things we get asked
Metal swaging is a metal forming technique that uses pressure to form metal into a desired shape. It’s a cold-forming process that doesn’t remove metal but instead reshapes it. As the swaging process doesn’t require heat, it becomes energy efficient too. The process can create precise shapes, reduce diameters, or add features. As the metal’s structure is refined the strength of the metal is also enhanced.
Metal swaging is widely used in metal forming due to its capability to create precise, strong parts with minimal material waste. Swaging is also efficient as it’s a cold-forming process, requiring no heating which reduces energy consumption, and this makes it suitable for high volume production.
The process of metal swaging is a cold-forming process where force reshapes metal. Involving forcing a metal part through a die, which forms its final shape. The process is typically used to form complex shapes, reduce diameters, or create features. Swaging is an effective solution for unique or irregular shapes that other processes or methods may not easily achieve.
Some advantages of swaging metal are material utilisation, cost-effectiveness, and precise reshaping. The material’s mechanical properties are improved, including strength and resistance to fatigue, making it suitable for demanding applications.
At Tanfield, we uphold strict quality inspections, adherence to ISO standards, and advanced technology helps to ensure every component meets customer specifications.
Tanfield serves a variety of industries that require high-quality, precise metal fabrication. These include sectors such as agriculture, air movement, renewable energy, safety, pressure vessels, food industry, and playground. Tanfield offers versatile services, including metal spinning, swaging, and machining, to meet the range of needs of each sector.