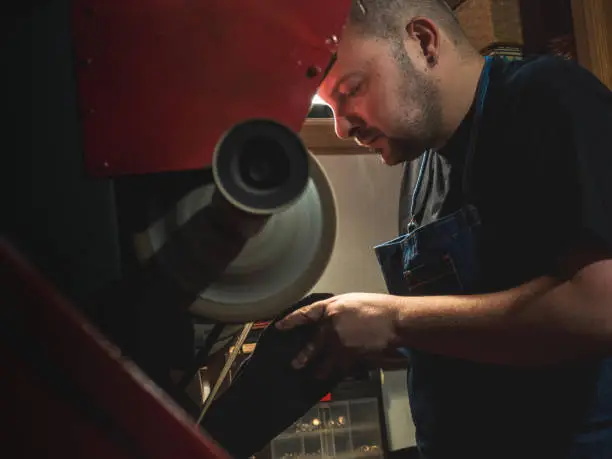
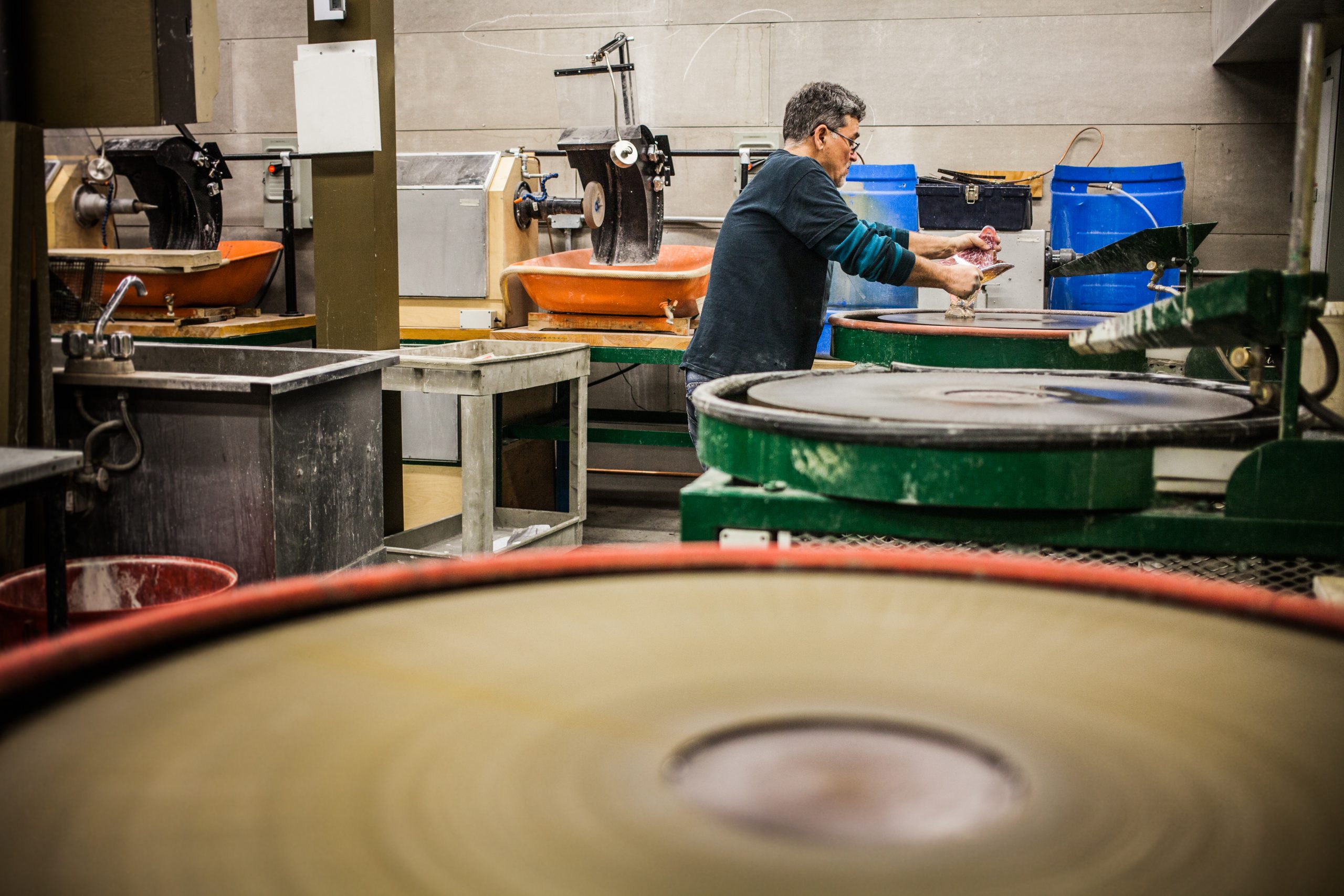
The Benefits of Partnering with a Trusted Metal Spinning Manufacturer
Precision, efficiency, and adaptability are paramount in modern manufacturing. Quality and consistency are essential whether you’re producing components for aerospace, medical equipment, or lighting. A trusted metal spinning partner helps you ensure your manufacture meets exact specifications, is delivered on time, and is optimised for performance.
Working with an experienced manufacturer offers technical capabilities and the assurance of industry expertise, responsive support, and a commitment to quality. Below, we explore the key advantages of partnering with a reliable metal spinning company like Tanfield Metal Spinners and how it can positively impact your project from concept to completion.
Cost-Effective Metal Spinning for Custom and Large-Scale Production
A trusted metal spinning partner understands how to reduce costs without compromising quality. Metal spinning is inherently efficient, using a single blank to form the final component with minimal waste. Unlike stamping or casting, which require expensive dies or moulds, metal spinning needs only a mandrel, significantly lowering tooling costs.
This level of efficiency makes it an ideal solution for both low-volume custom parts and high-volume production. The ability to scale quickly while keeping production costs in check gives manufacturers flexibility and long-term value, especially when combined with Tanfield’s automation capabilities.
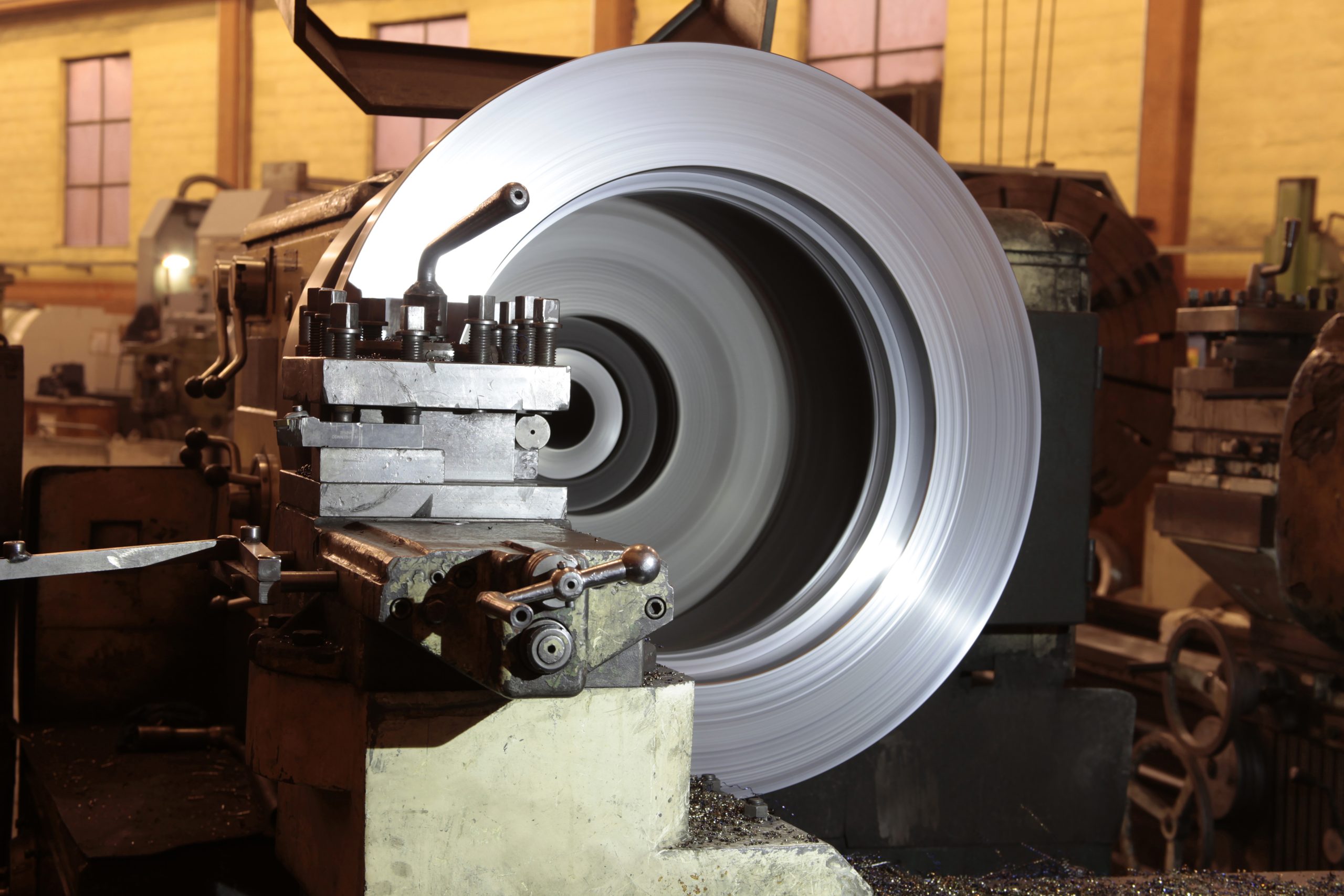
Precision Engineering with CNC Metal Spinning Technology
Working with a reputable manufacturer provides access to advanced CNC (Computer Numerical Control) metal spinning machinery. CNC spinning delivers exceptional consistency, enabling tight tolerances and complex geometries to be replicated across large production runs with absolute accuracy.
Tanfield’s use of CNC automation ensures precision without the variability of manual processes, making it ideal for industries such as aerospace and medical, where even minor deviations can compromise performance. CNC spinning also allows for faster setup and reduced lead times, supporting design changes and prototyping without disruption.
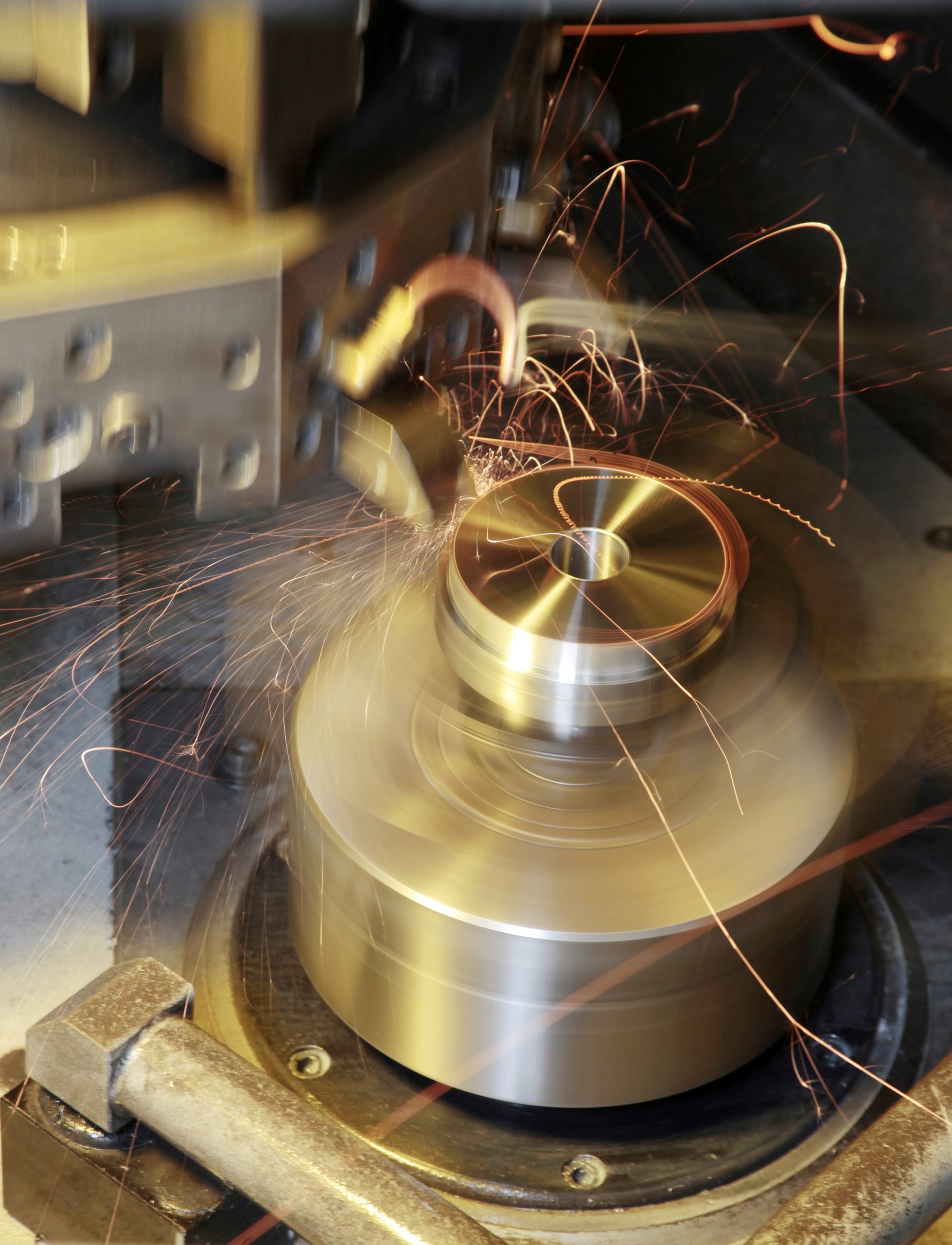
Stronger, More Durable Components with Work-Hardened Materials
The metal spinning process naturally strengthens materials through work-hardening, which aligns the metal’s grain structure for added durability. Components produced this way can withstand high stress, temperature variations, and corrosive environments, all without welding or additional reinforcement.
At Tanfield, our engineers ensure each component is optimised for its application. By advising on the most suitable material, be it stainless steel, aluminium, copper, or brass, we help clients enhance their product performance and lifespan.
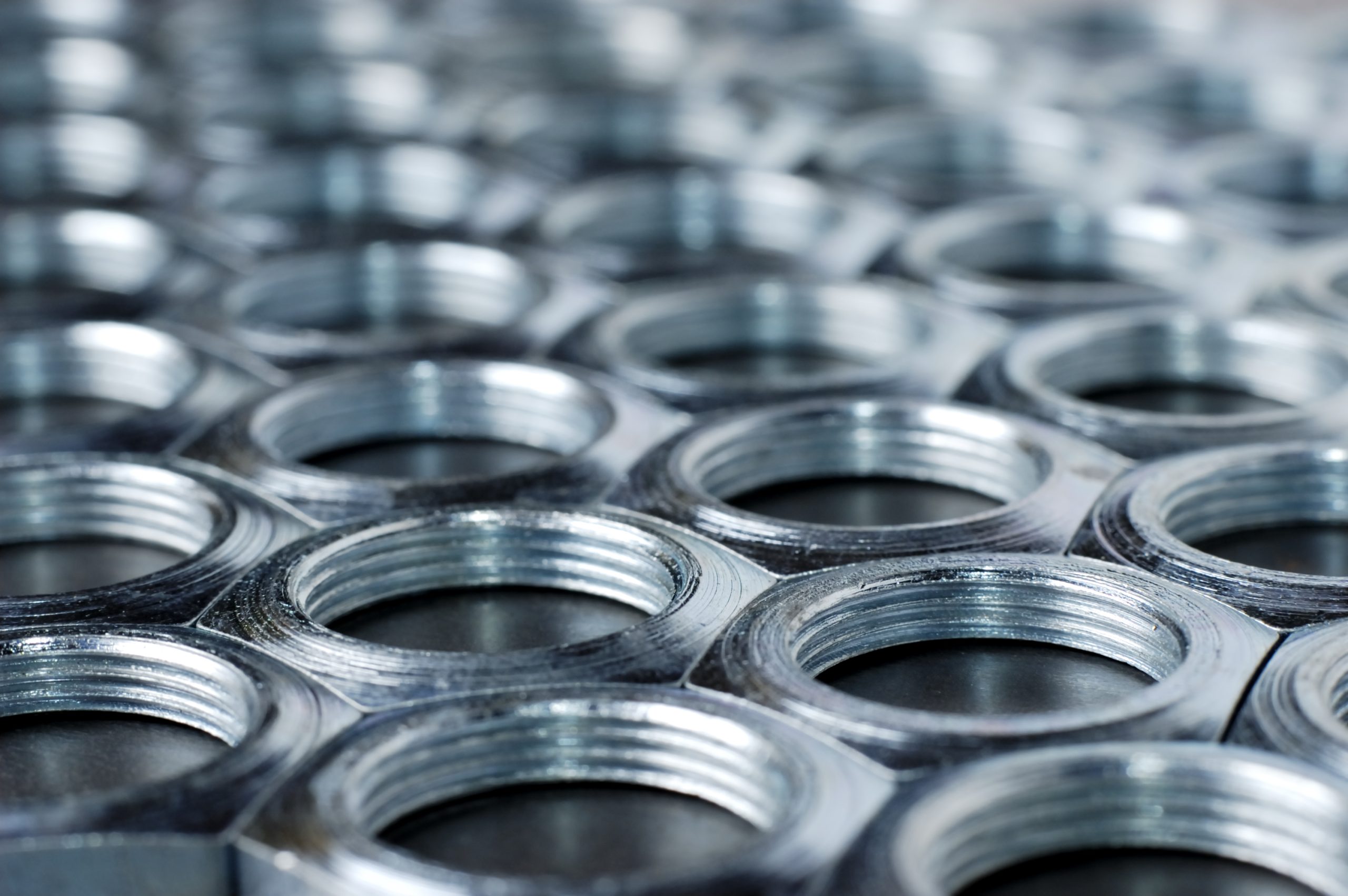
Integrated Metal Finishing and Polishing Services
High-quality metal components often require finishing touches such as polishing, coating, or trimming. A full-service manufacturer like Tanfield offers these services in-house, streamlining the process and ensuring consistent quality across every stage.
Our finishing capabilities enhance corrosion resistance, improve aesthetics, and prepare components for coatings like powder coating or anodising. By managing these processes under one roof, we eliminate the need for multiple suppliers and reduce turnaround times.
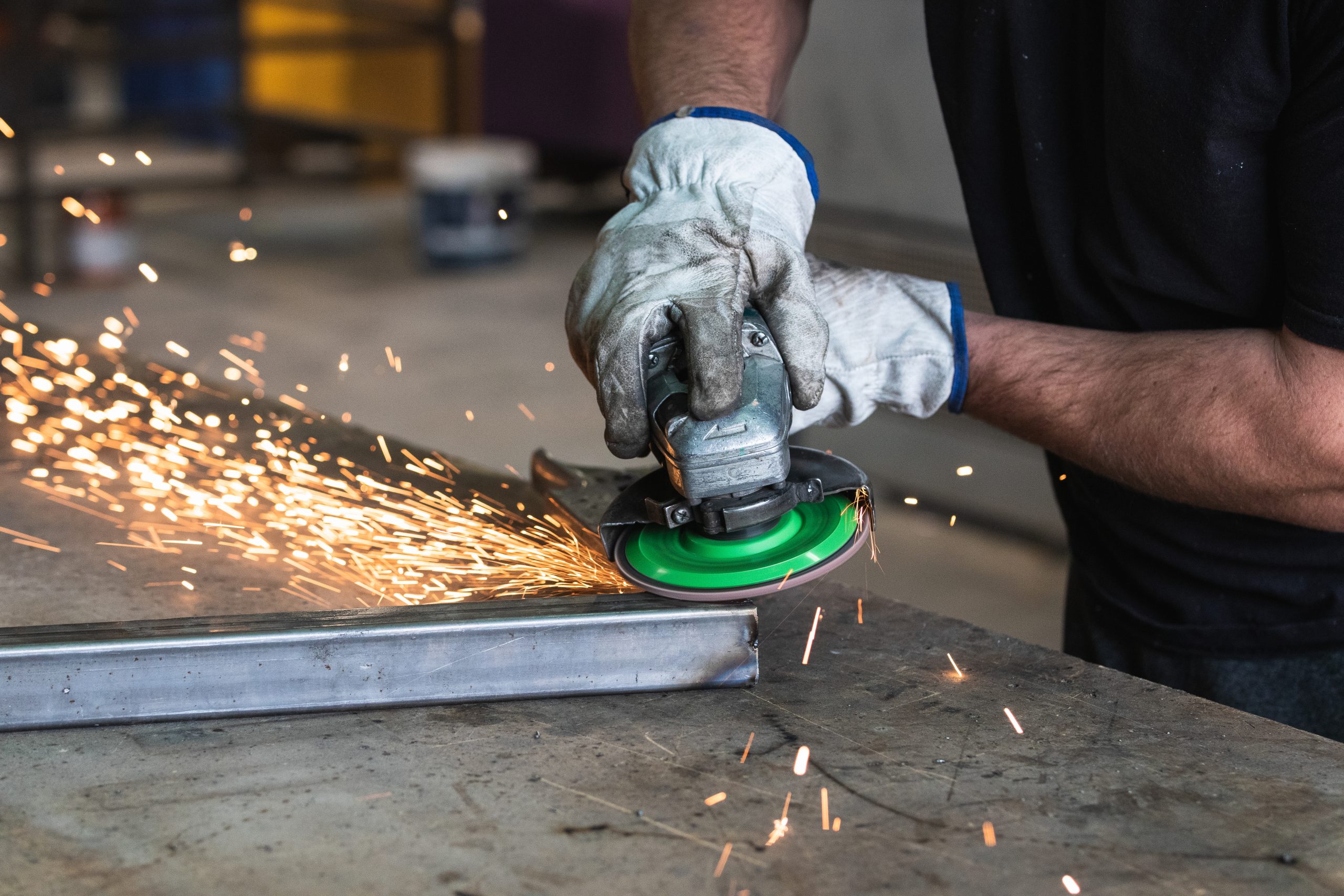
Quality Assurance and Risk Reduction in Metal Manufacturing
Consistency is critical in manufacturing. A trusted metal spinning company implements rigorous quality control procedures at every stage. At Tanfield, each product undergoes thorough inspections, dimensional checks, and surface assessments to meet strict specifications.
Reliable partners also help reduce the risks associated with outsourcing, such as missed deadlines, quality issues, or compliance concerns, giving you peace of mind that your production is in expert hands.
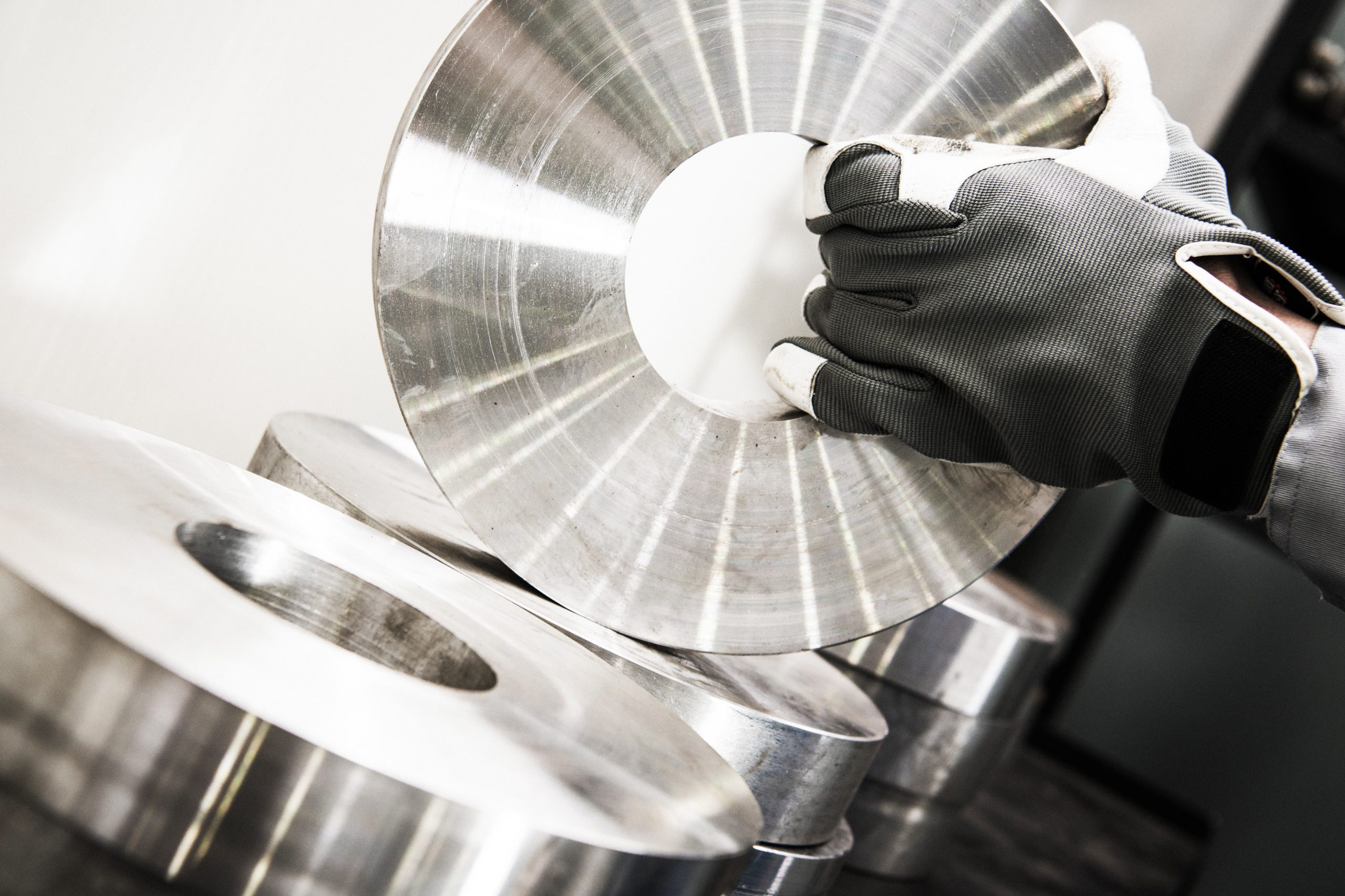
Sustainable Metal Spinning Practices That Reduce Waste
As industries pursue greener manufacturing, metal spinning aligns well with sustainability goals. The process produces minimal scrap as it reshapes rather than cuts metal, and many materials used, like aluminium and stainless steel, are fully recyclable.
Tanfield is committed to sustainable manufacturing. We reduce energy consumption through automation, use eco-friendly coatings, and optimise material use throughout our operations. Clients benefit not only from lower costs but also from a reduced environmental impact.
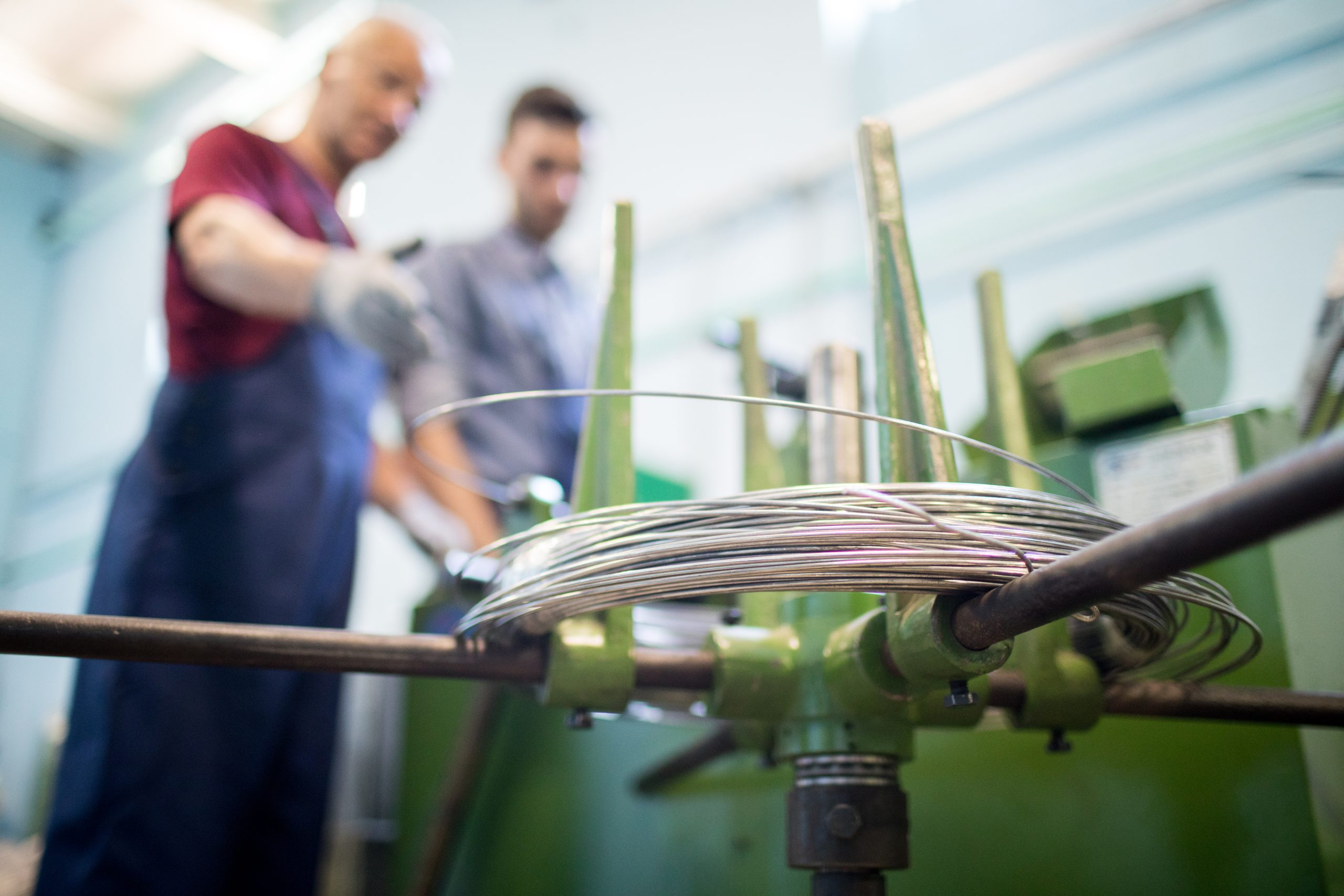
Collaborative Product Development and Engineering Support
One of the most valuable aspects of partnering with an experienced manufacturer is access to engineering insight from the outset. Tanfield works closely with clients during product development, advising on design feasibility, material selection, and manufacturing efficiency.
Whether you’re refining a prototype or preparing for volume production, our collaborative approach helps streamline development and deliver components that meet both performance and cost expectations.
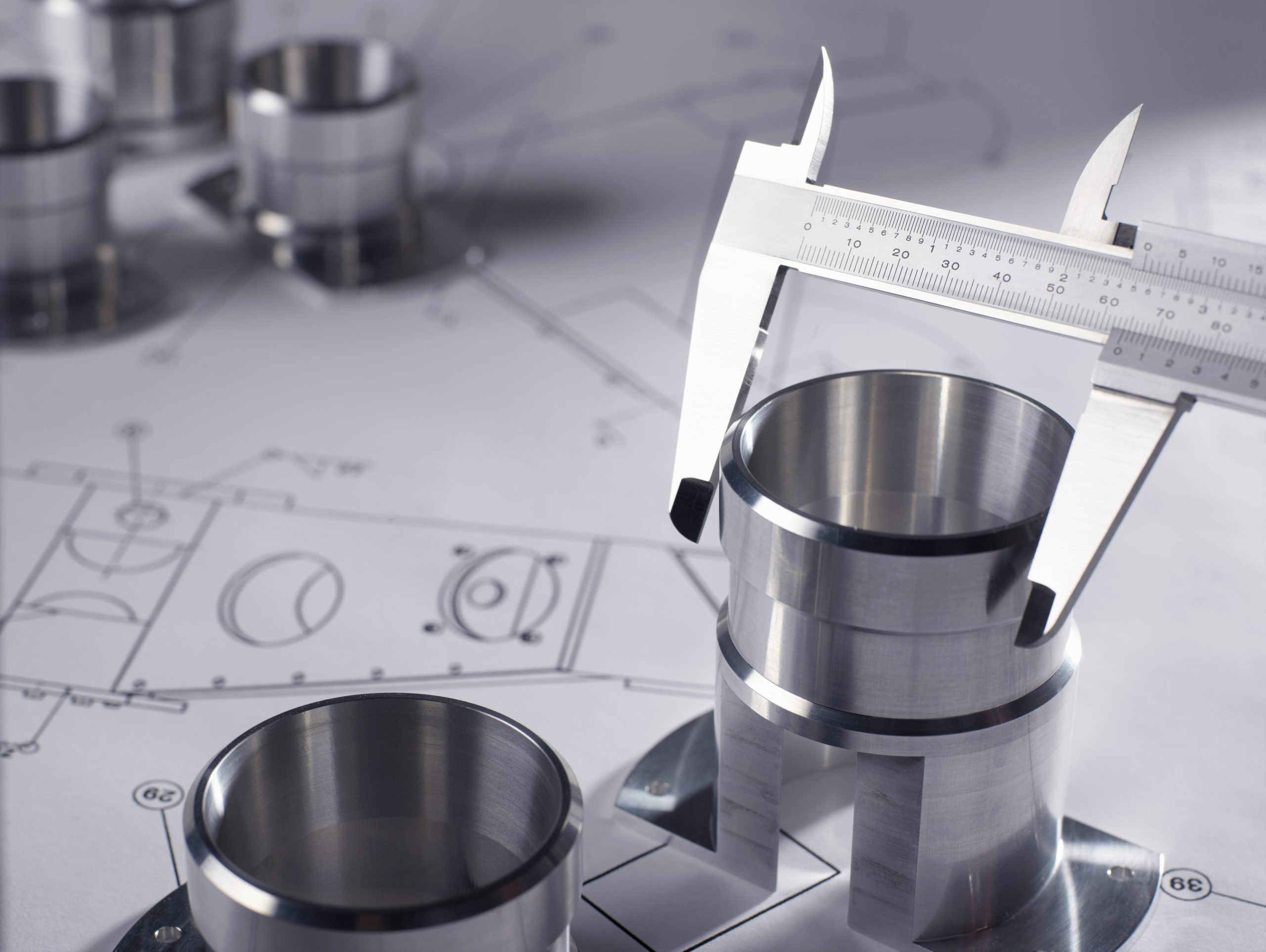
Long-Term Value from a Trusted Metal Spinning Manufacturer
Forming a long-term partnership with a reliable metal spinning supplier like Tanfield offers strategic advantages beyond production. You gain a dependable extension of your team—one that’s invested in the success of your products, responsive to change, and focused on continuous improvement.
At Tanfield, we combine decades of experience with fully automated capabilities and the UK’s most extensive tooling range to deliver bespoke metal spinning solutions tailored to your needs. Whether you require complex geometries, rapid prototyping, or scalable production, we’re here to help.
Contact us today to discuss how we can support your next project with reliable, sustainable, and precision-focused metal spinning services.
Contact Us Today!
We encourage you to reach out to us today, our team of knowledgeable experts is ready to answer your questions, provide personalised guidance, and help you find the right solution for your needs.
Contact Us