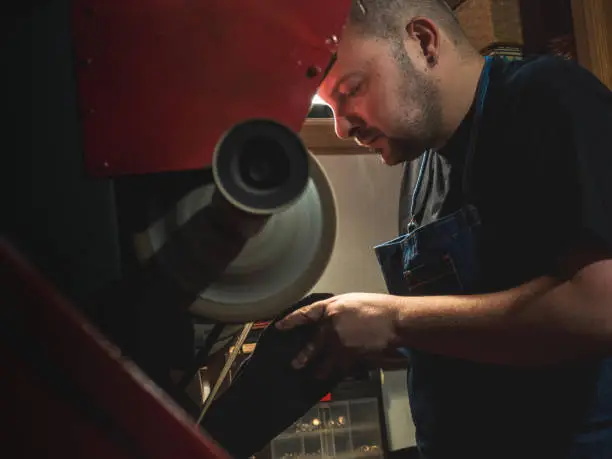
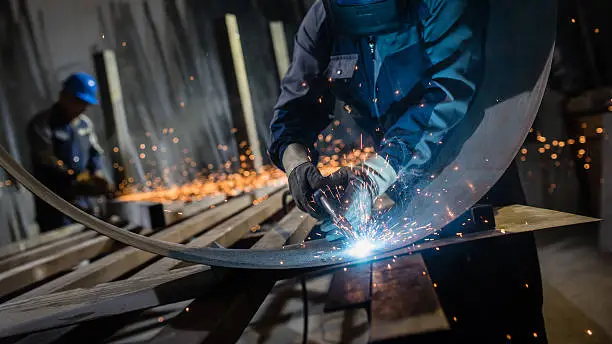
Metal Spinning or Traditional Fabrication? Discover the Best Method for Your Metal Working Project
In the world of metalworking, there are several available methods to shape and craft components, each offering unique benefits depending on the requirements of the project. Among the most prominent techniques are traditional fabrication and metal spinning. These methods cater to different needs, and understanding their distinctions can help you choose the best fit for your specific application. In this guide, we will explore the nuances of these approaches, their advantages, and their most suitable applications.
What Is Traditional Fabrication?
For the purposes of this blog, we define traditional fabrication as a combination of traditional techniques such as cutting, welding, bending, and assembling metals. It is renowned for its versatility and ability to create a wide variety of designs, from simple to highly complex structures.
The Role of Traditional Fabrication
Traditional fabrication plays a vital role in industries requiring intricate assemblies and custom designs. By employing various tools and methods, it accommodates projects with diverse requirements, ranging from large-scale construction to bespoke industrial components.
Common Applications of Traditional Fabrication
Traditional fabrication finds widespread use across various industries due to its versatility and adaptability, including:
- Creating structural steel frameworks for buildings and infrastructure, which provide essential support and stability.
- Manufacturing custom enclosures for industrial equipment, ensuring both functionality and durability.
- Developing vehicle chassis for automotive production, contributing to the safety and efficiency of modern vehicles.
- Constructing metal frameworks for machinery, critical for industrial operations.
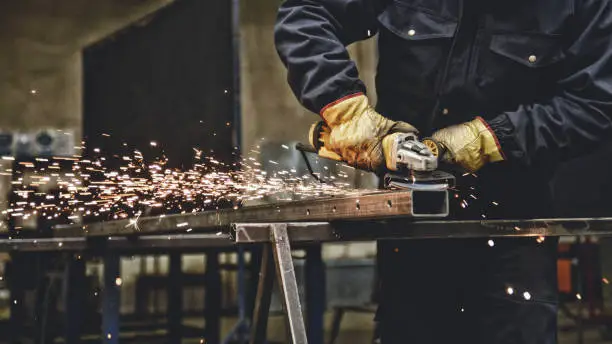
Benefits of Traditional Fabrication
Traditional fabrication is a versatile and reliable approach in metalworking. It covers projects of all scales and complexities, making it a mainstay across industries. Its benefits include:
- Scalability for large projects: Traditional fabrication accommodates both small batches and high-volume production runs, making it suitable for projects of varying sizes.
- Support for intricate assemblies: This approach allows for the creation of complex designs by joining multiple components, enabling highly detailed and customised outcomes.
- Versatility with materials: From lightweight aluminium to robust steel, traditional fabrication supports various metals and thicknesses, meeting diverse project requirements.
- Refinement through established processes: Decades of innovation and use have made traditional fabrication highly efficient, ensuring reliable results that adhere to modern standards.
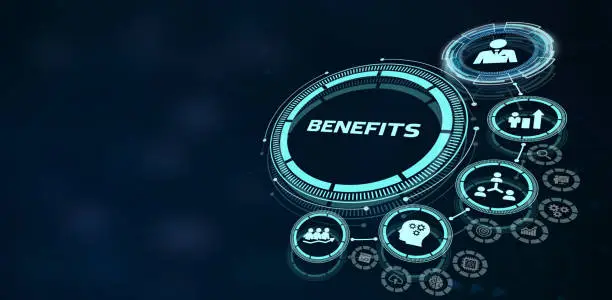
What Is Metal Spinning?
Metal spinning is a specialised and precise metalworking process that involves shaping flat metal discs, or blanks, into symmetrical forms by spinning them on a lathe while applying controlled pressure with a roller tool. This process creates components that are both seamless and durable.
Why Metal Spinning Matters
Metal spinning is highly valued for its ability to produce high-quality, symmetrical parts with minimal waste. The technique is especially effective for industries requiring precision-engineered components that must meet stringent performance criteria.
Typical Applications of Metal Spinning
Metal spinning offers unmatched precision and strength, making it the preferred choice for industries that demand high-quality, seamless components. Some of its most common applications include:
- Satellite dishes for advanced communication systems, where seamless construction ensures optimal performance.
- Elegant decorative light fittings, combining form and function to enhance interior design.
- Robust industrial components, such as machine parts, designed for longevity and reliability.
- Everyday kitchenware like bowls and pans, offering seamless finishes that are both practical and aesthetically pleasing.
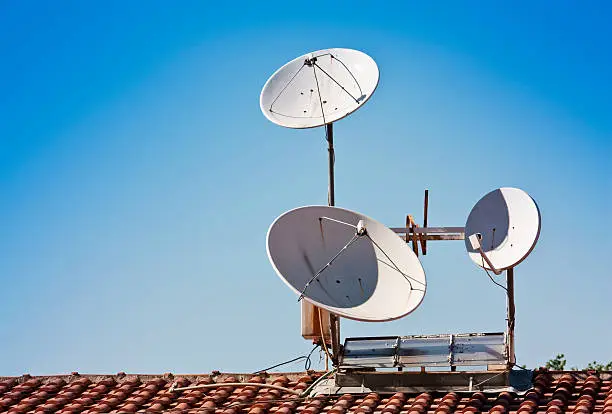
Key Benefits of Metal Spinning
The advantages of metal spinning go beyond its precision and efficiency. This method delivers value in both performance and sustainability, making it a preferred choice for many applications. Its key benefits include:
- Cost savings for small production runs: Metal spinning involves lower tooling costs, which makes it particularly economical for prototypes and limited batch productions.
- Enhanced material durability: Spinning work-hardens the material, increasing its strength and resistance to deformation, which is essential for high-performance applications.
- Flexibility in design changes: This method supports quick and economical design adjustments, enabling manufacturers to adapt efficiently without significant delays.
- Environmentally conscious production: Metal spinning generates minimal waste by shaping a single blank, making it a sustainable option for eco-minded industries.
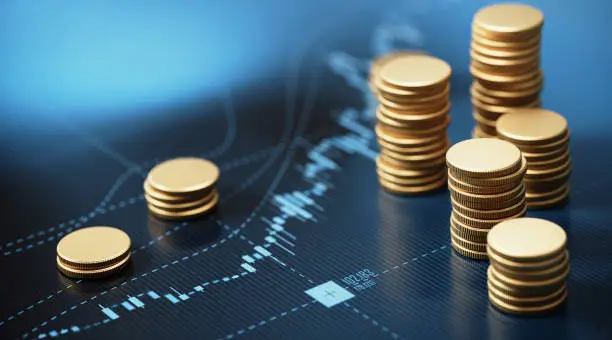
Comparing Metal Spinning and Traditional Fabrication
While both methods are indispensable, their differences highlight their unique applications and benefits. Below is a direct comparison:
Feature | Metal Spinning | Traditional Fabrication |
Process | Forms shapes by spinning a single metal piece | Involves cutting, welding, and assembling parts |
Tooling Costs | Lower costs for small to medium runs | Higher costs due to specialised equipment |
Material Use | Minimal waste | Higher material wastage |
Material Strength | Enhanced through work-hardening | Relies on base material properties |
Design Suitability | Best for symmetrical, rounded shapes | Ideal for intricate and complex assemblies |
Factors to Consider When Choosing a Metal Working Method
Selecting the right metalworking method is a crucial decision that can significantly impact the success of your project. Understanding the unique strengths of metal spinning and traditional fabrication will help you identify the best fit for your specific requirements. Here are the key factors to consider:
- The scale of production volume: Metal spinning provides a cost-effective solution for small-to-medium runs, while traditional fabrication is better suited for high-volume projects.
- The complexity of shapes and designs: Seamless and symmetrical shapes are ideal for metal spinning, whereas traditional fabrication is more adept at handling intricate assemblies and custom designs.
- Budgetary considerations: Projects with tighter budgets may benefit from the lower tooling costs associated with metal spinning, particularly for prototypes and limited runs.
- Durability and strength requirements: If enhanced material strength is a priority, the work-hardening effect of metal spinning may provide the desired outcome for your components.
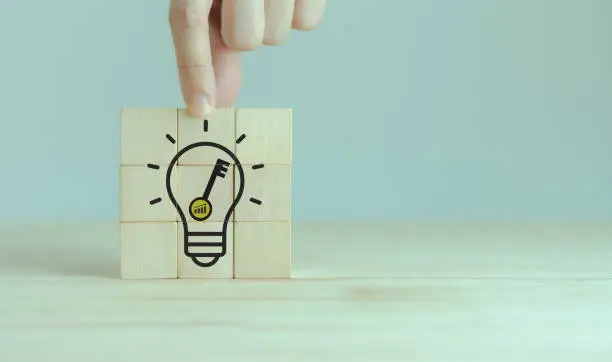
When to Choose Metal Spinning Over Traditional Fabrication
While both metal spinning and traditional fabrication have their merits, there are specific scenarios where metal spinning stands out as the superior option. These include:
- Smaller production volumes: With lower tooling costs, metal spinning is highly economical for prototypes and low-to-medium production runs.
- Enhanced strength and durability: Projects demanding high tensile strength benefit significantly from the work-hardening effect achieved during the spinning process.
- Commitment to sustainable practices: The minimal material waste generated by metal spinning makes it a preferred choice for environmentally conscious manufacturers.
- The need for seamless components: The flawless surface achieved through metal spinning ensures optimal performance for parts like satellite dishes and reflectors.
- Adaptability to design changes: Metal spinning supports rapid adjustments, enabling manufacturers to modify designs without incurring significant delays or costs.
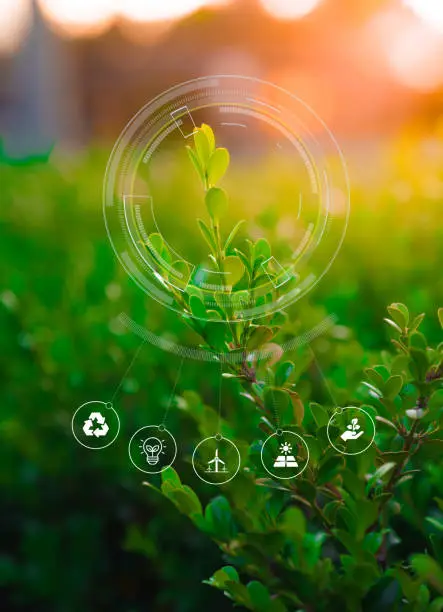
Making the Right Choice for Your Metal Working Project
Choosing the right method for metalworking is essential to achieving your project goals. By understanding the distinct advantages of metal spinning and traditional fabrication, you can make an informed decision that ensures the best results. Whether you need the precision and strength of metal spinning or the versatility of traditional fabrication, selecting the right approach guarantees the highest quality components.
At Tanfield Metal Spinners, we specialise in providing high-quality metal spinning solutions tailored to your unique requirements. With the most extensive tooling range in the UK and advanced facilities, we deliver precision-engineered components for projects of any scale. Whether you need prototypes or large production volumes, our team ensures exceptional results with a commitment to excellence.