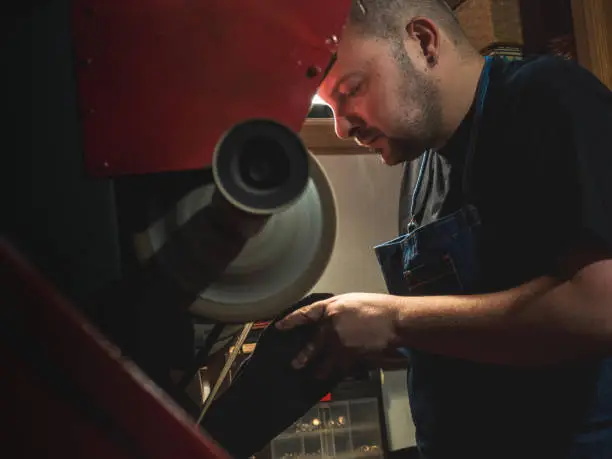

How to Choose the Best Material for Your Metal Spinning Project
Material selection is one of the most critical decisions in any metal spinning project. The success of the final component, from its structural integrity to its longevity and aesthetic finish, depends on choosing the right metal for the job. Whether developing a bespoke product or scaling up production for industrial use, understanding how different materials behave during the spinning process can ensure optimum performance, cost-efficiency, and sustainability.
At Tanfield Metal Spinners, we guide clients through every aspect of material choice. This blog explores the key factors to consider when selecting a metal for spinning and reviews the most commonly used metals and their applications.
Why Material Selection Matters in Metal Spinning
Metal spinning is a versatile forming technique that reshapes a flat metal disc or tube into a symmetrical part using a rotating lathe and applied pressure. Unlike methods such as stamping or casting, metal spinning does not remove material; it reformats it, retaining structural strength and reducing waste. However, this process places unique demands on the metal. Not all materials respond equally well to the stresses of high-speed forming.
Selecting an unsuitable metal can lead to deformation, excessive wear, or even part failure. Conversely, the right choice will facilitate smoother spinning, lower tooling requirements, and produce stronger, more durable components. With this in mind, let’s examine what you need to consider when deciding on the best material for your project.
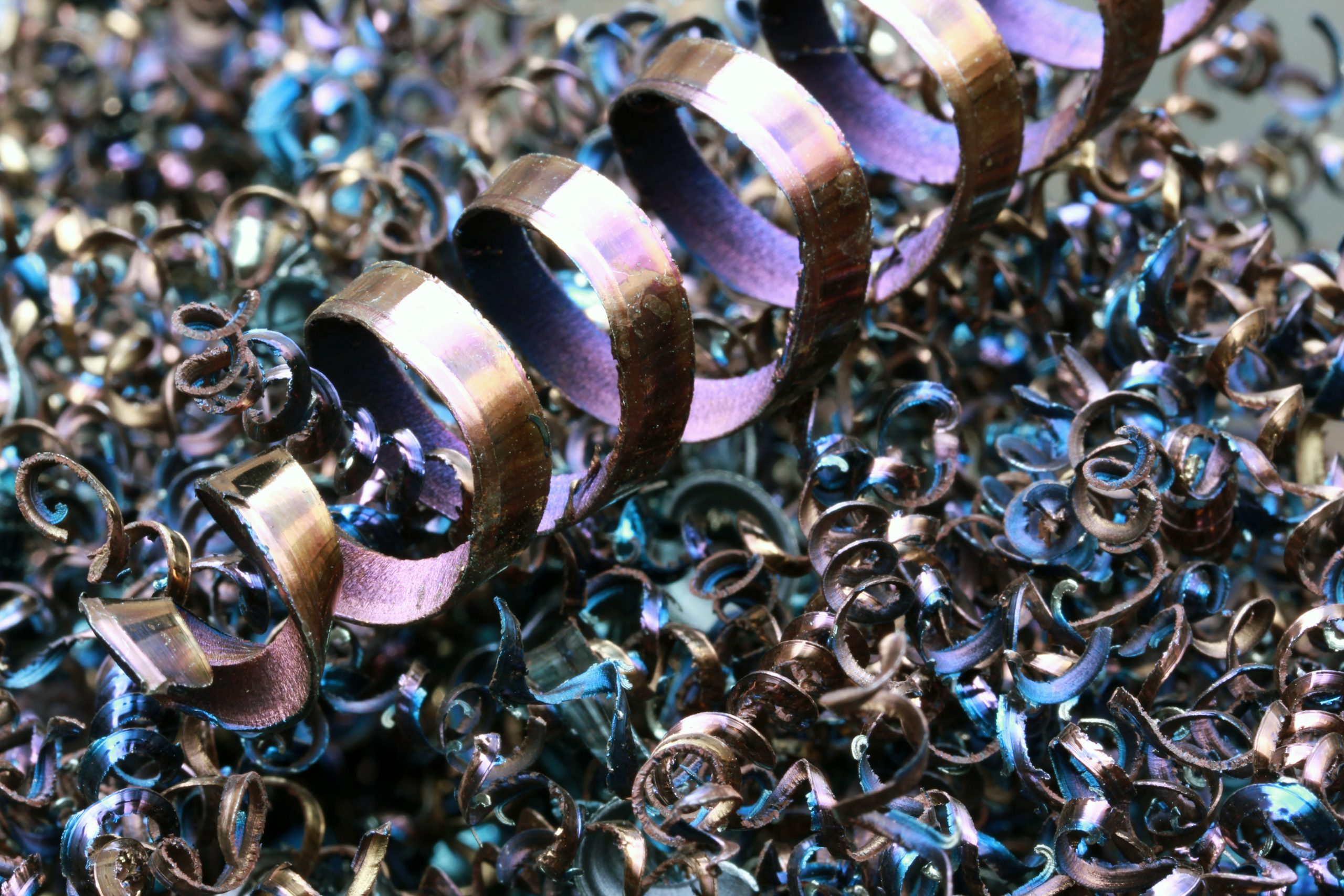
Choosing the Right Metal for Spinning
1. Formability and Ductility
Spinnability, or the ability of a metal to be formed without cracking, is essential. Ductile metals like aluminium and copper deform easily under pressure and are ideal for intricate shapes. Harder or more brittle materials like titanium may require special processing, like annealing during spinning, to prevent cracking or tearing.
2. Strength and Durability
Depending on the end use, the component may need to withstand harsh environments or mechanical stress. Stainless steel, for instance, offers high tensile strength and excellent corrosion resistance, making it ideal for aerospace or medical applications.
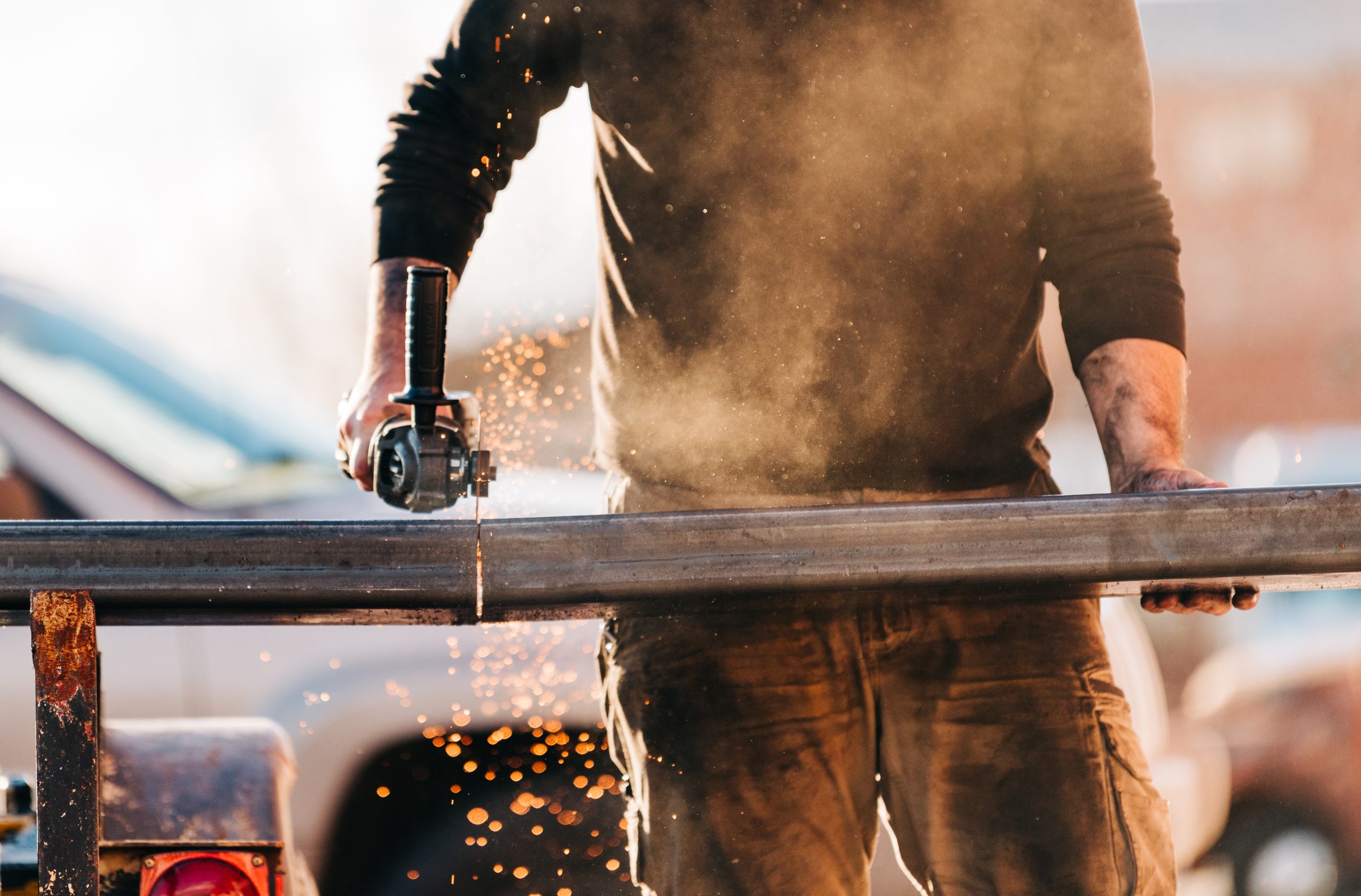
3. Intended Application
Every industry has unique material needs. For example, food-grade stainless steel is vital for hygiene in catering equipment, while copper’s conductivity makes it suitable for electrical components. Understanding the final application ensures the material’s mechanical and chemical properties align with operational demands.
4. Finish and Appearance
If aesthetics matter, as they frequently do in lighting fixtures or consumer products, the natural finish of the metal comes into play. Copper and brass are chosen for their rich tones, while polished stainless steel offers a clean, modern look. Some metals also accept coatings and polishing better than others, which can enhance their final appearance.
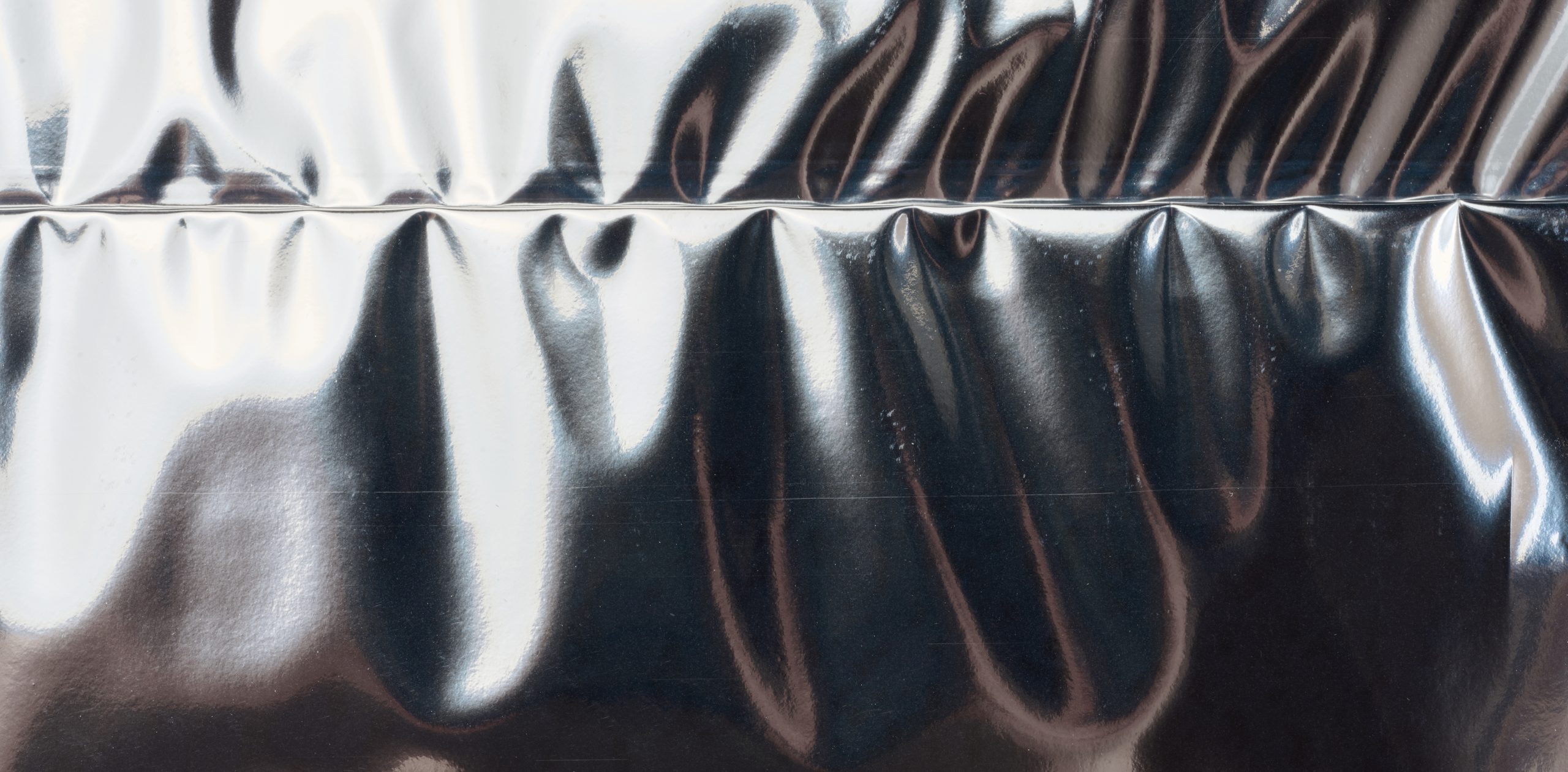
5. Cost and Availability
Budgetary constraints often influence material selection. Aluminium and mild steel offer good spinnability at a lower cost, while higher-spec materials like titanium or speciality alloys are more expensive but may be essential for performance-critical applications.
6. Sustainability
Many industries are now prioritising environmentally conscious practices. Recyclable metals like aluminium and stainless steel align with sustainability goals and help reduce a project’s environmental footprint without compromising quality.
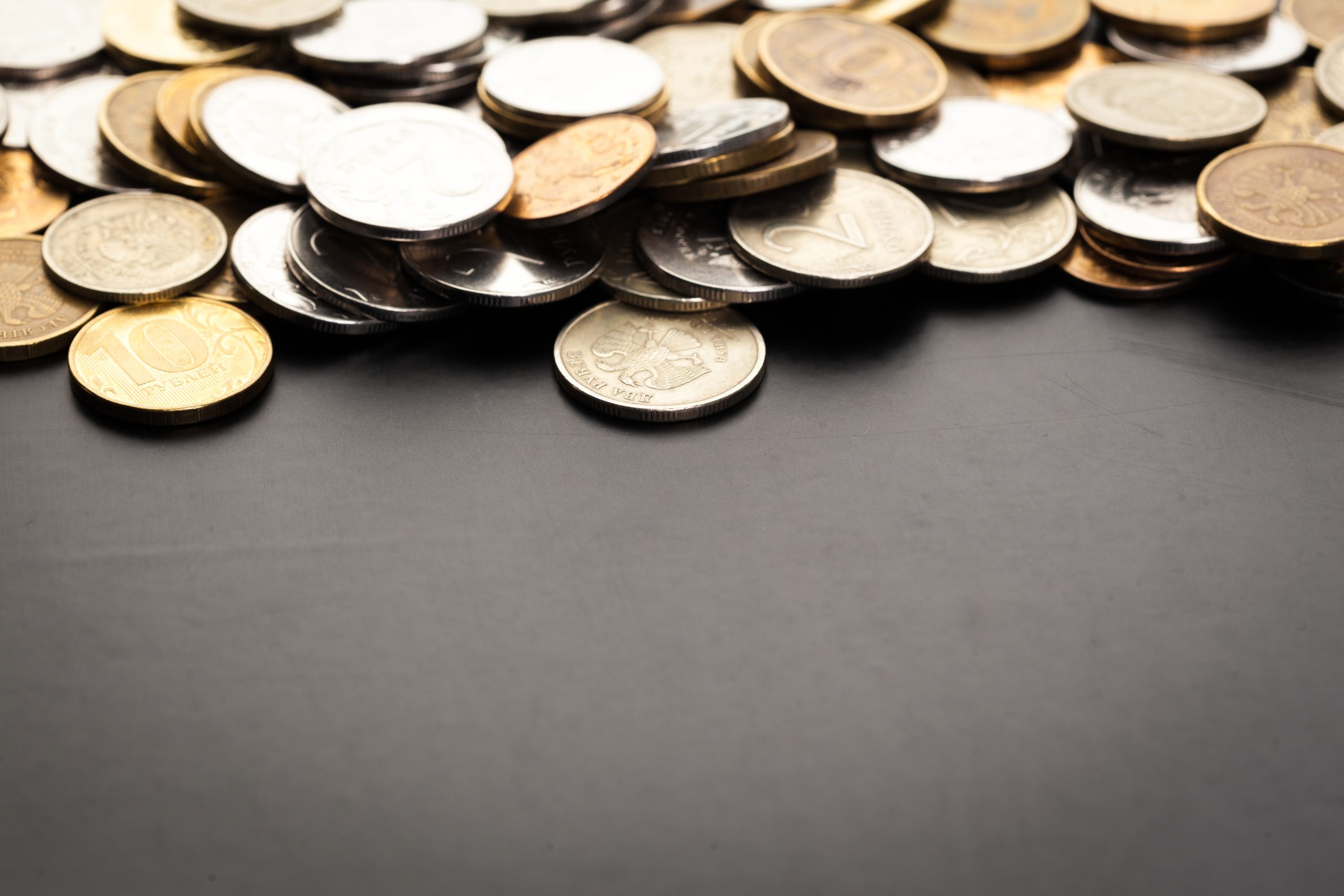
Common Metals Used in Spinning Projects
Let’s explore the metals most frequently selected for metal spinning and the applications they suit best.
Aluminium: Lightweight and Highly Workable
Aluminium is arguably the most popular choice in metal spinning. It combines high corrosion resistance, excellent formability, and lightweight characteristics, making it ideal for aerospace, automotive, and lighting applications. Its affordability and recyclability further enhance its appeal for sustainable manufacturing.
Grades such as 1100 and 3003 are often used due to their ease of forming and clean finish, which requires minimal polishing post-spinning.
Stainless Steel: Strength with Corrosion Resistance
Stainless steel is the go-to option for projects requiring mechanical strength and resistance to oxidation, particularly in demanding environments. Grades 304 and 316 are commonly used for their hygienic properties and durability, and they are ideal for medical equipment, kitchenware, and marine components.
While stainless steel requires more force to spin than softer metals, its longevity and strength justify the added complexity and cost in high-spec applications.
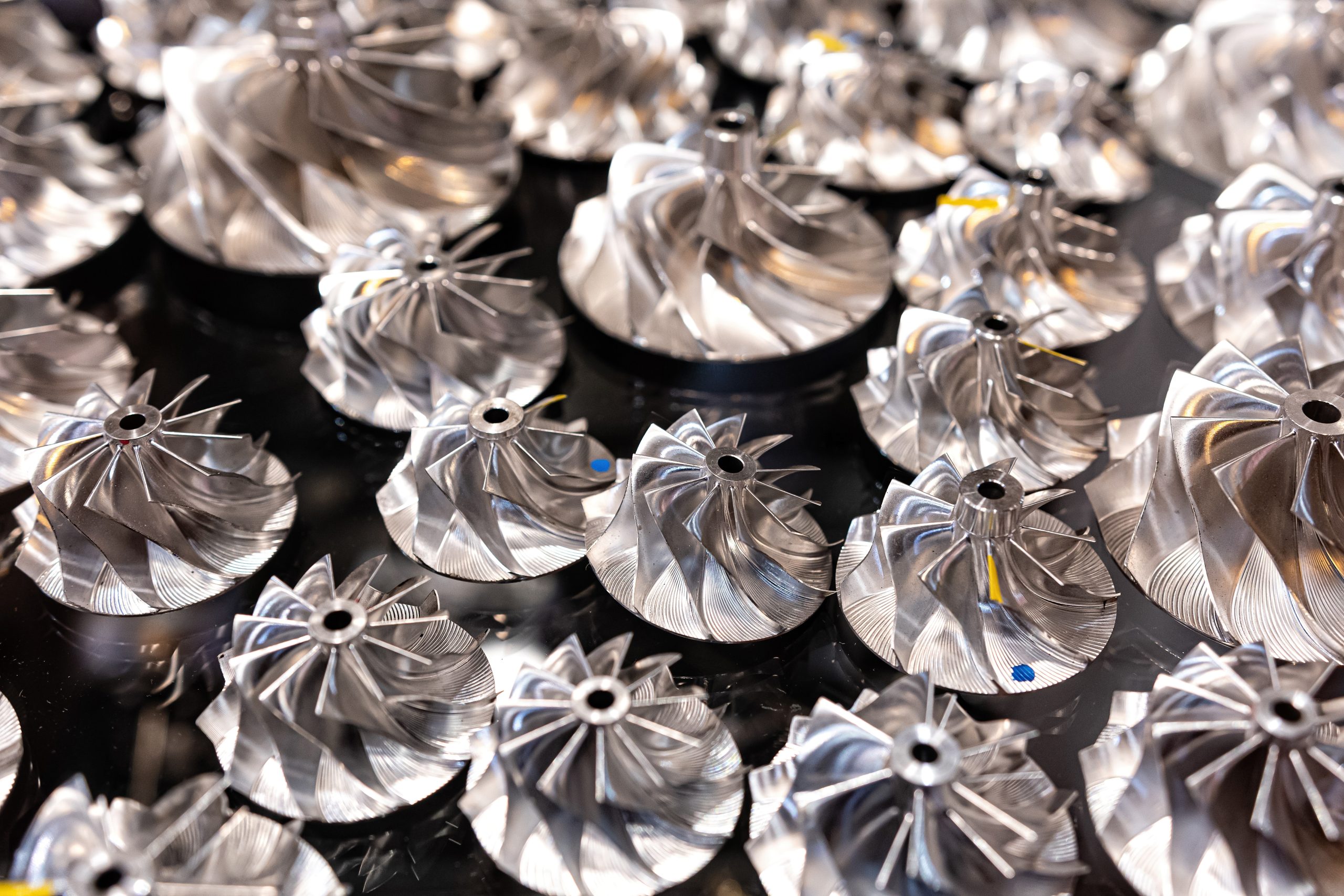
Copper: Exceptional Conductivity and Aesthetics
Copper’s excellent thermal and electrical conductivity makes it indispensable for electrical, HVAC, and decorative projects. It is also naturally antimicrobial, making it suitable for medical and food-contact surfaces.
Its malleability makes it easy to spin, though it requires careful handling to avoid work-hardening too quickly. It also offers a distinctive, warm finish that appeals to designers and architects alike.
Brass: Aesthetic Appeal with Formability
Brass, an alloy of copper and zinc, is another decorative favourite due to its golden hue and corrosion resistance. Brass is widely used in artistic and architectural applications, musical instruments, and light fittings.
While not as conductive as copper, brass does balance visual appeal with respectable strength and workability.
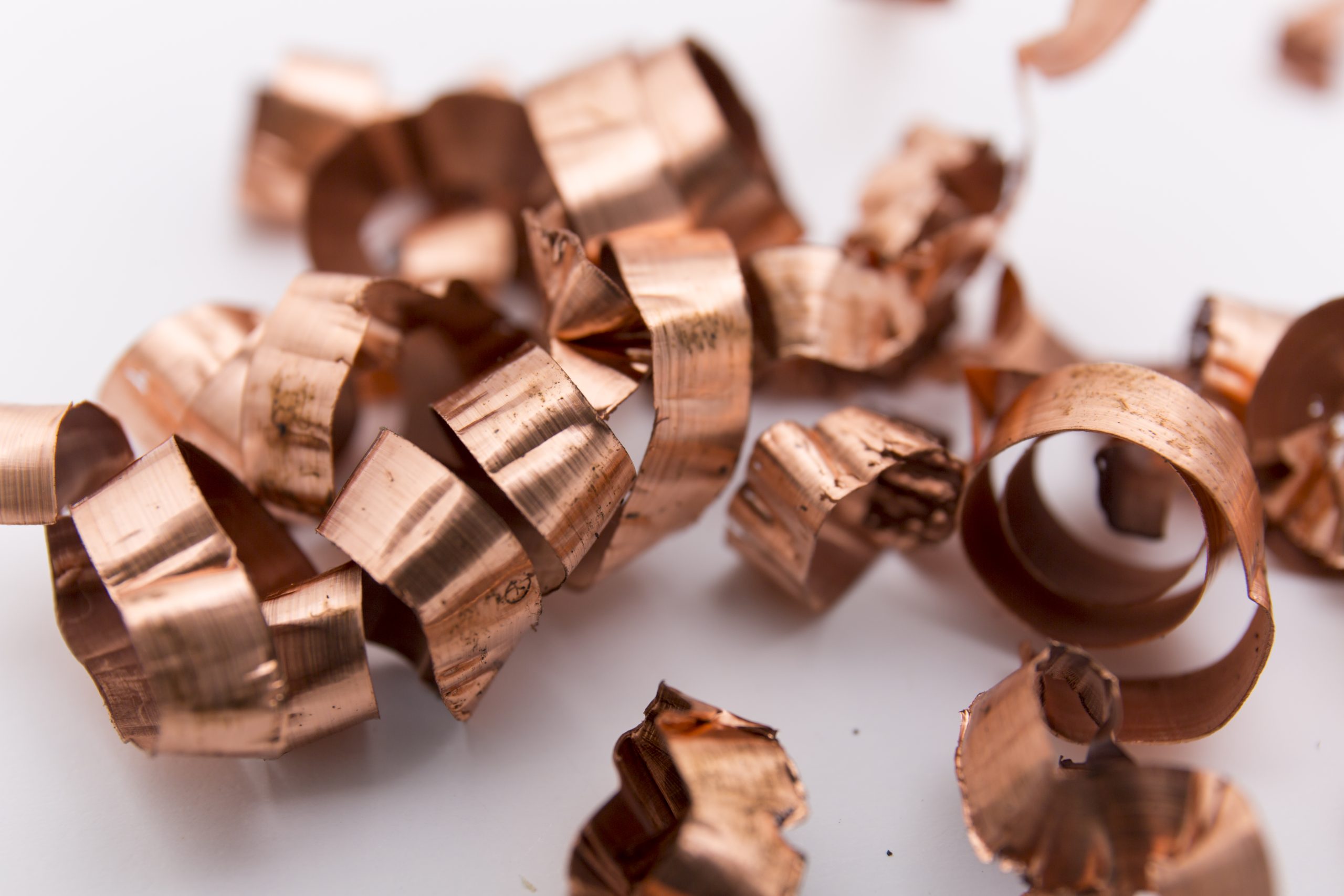
Mild Steel: Cost-Effective and Versatile
For industrial applications where high strength or corrosion resistance is less critical, mild steel offers a durable and affordable option. It’s easy to spin, weld, and machine, and is commonly used in automotive, agricultural, and structural components.
Mild steel can be enhanced to suit more demanding environments with appropriate finishing, such as powder coating or galvanising.
Titanium: High-Performance with Limitations
Titanium is valued in aerospace and medical sectors for its incredible strength-to-weight ratio and resistance to extreme temperatures. However, its hardness and low ductility make it challenging to spin without specialised equipment and processes like annealing.
Titanium is an excellent choice for projects requiring extreme durability and performance, provided the cost and complexity can be justified.
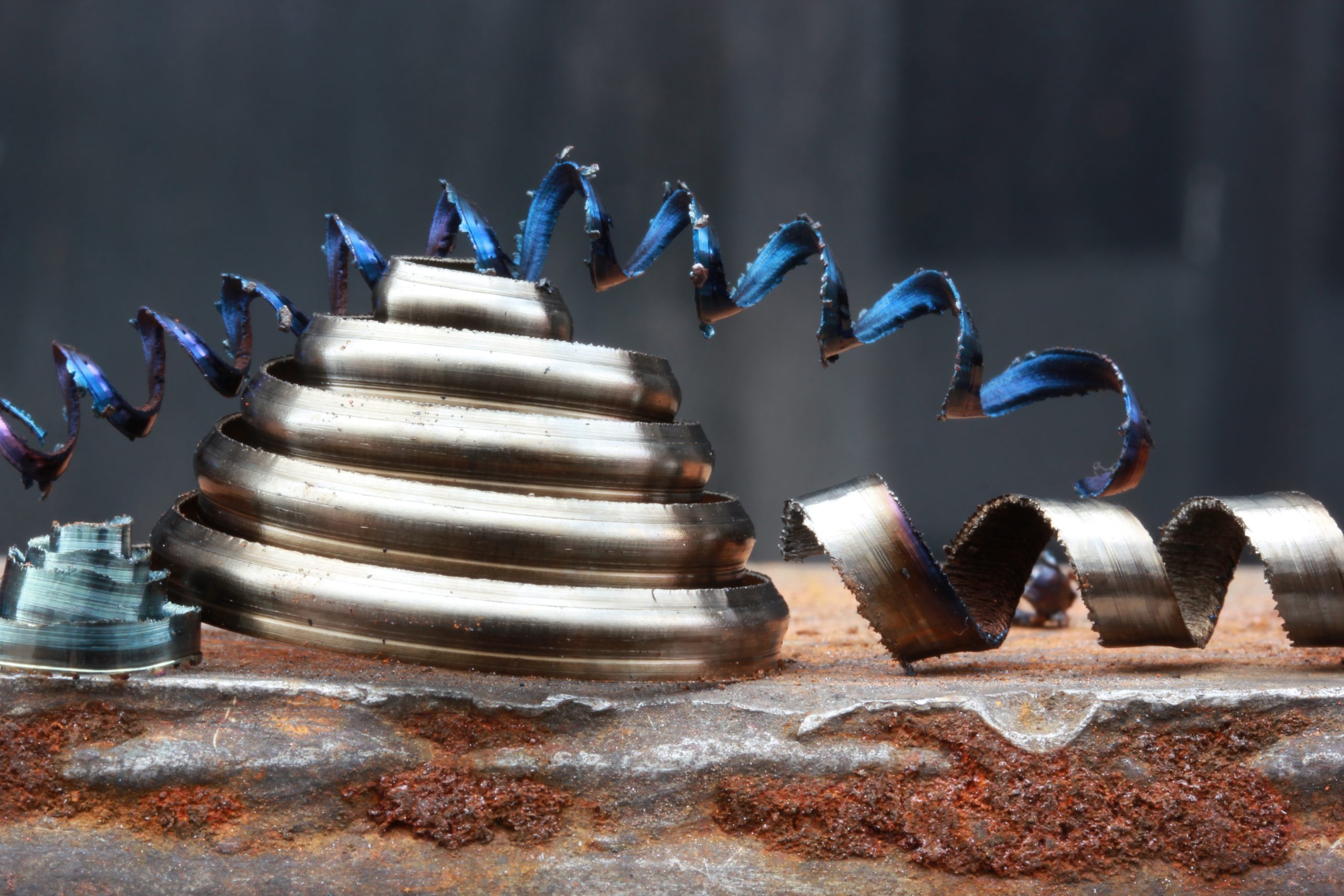
Tailoring Material Selection to Project Goals
Ultimately, the best material for a spinning project balances all the relevant performance, cost, and design factors. At Tanfield Metal Spinners, we consult closely with clients to match material characteristics with project requirements, whether you need a corrosion-resistant component for marine use, a polished decorative piece for architectural integration, or a lightweight, high-strength part for aerospace innovation.
Our extensive tooling capabilities and fully automated CNC systems enable us to spin a wide range of metals with precision and efficiency, making bespoke material selection a seamless part of the process.
Material Matters and Expertise Counts
Choosing the right material for your metal spinning project is more than just compatibility with the spinning process. It’s about engineering components that meet all expectations in function, form, and longevity.
From understanding the nuances of each metal’s properties to aligning with the end-use environment, selecting the correct material is a crucial step in ensuring success. Tanfield Metal Spinners provides the expertise and flexibility to guide your material choice and deliver outstanding results.
Ready to begin your next project? Contact Tanfield Metal Spinners today to discuss your application and explore the best materials for your needs.
Contact Us Today!
We encourage you to reach out to us today, our team of knowledgeable experts is ready to answer your questions, provide personalised guidance, and help you find the right solution for your needs.
Contact Us