Expert Metal Spinning Specialists Since 1984
How does this work?
Get in Touch
Please fill out the short form below and we’ll get in touch
Our Other Services
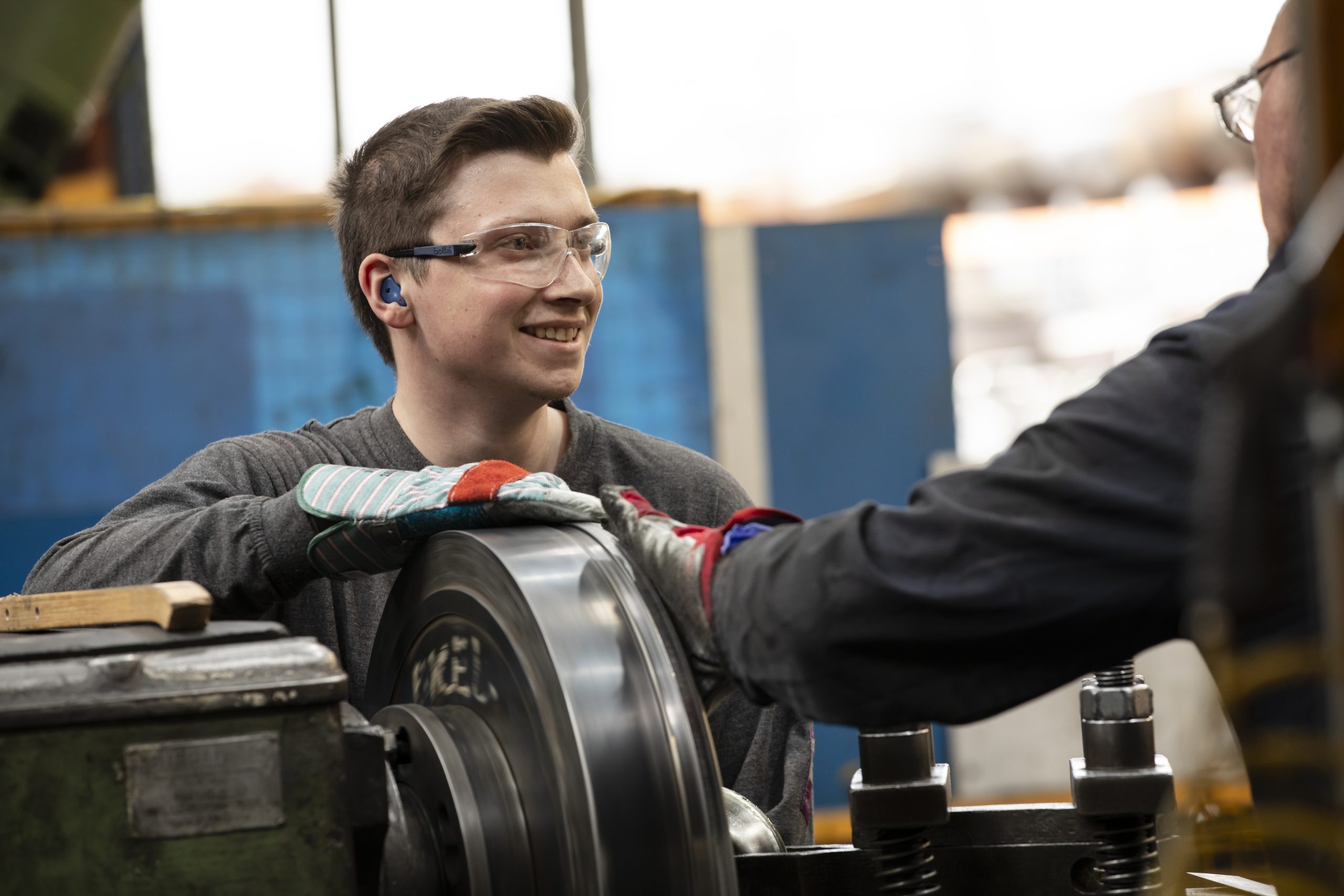
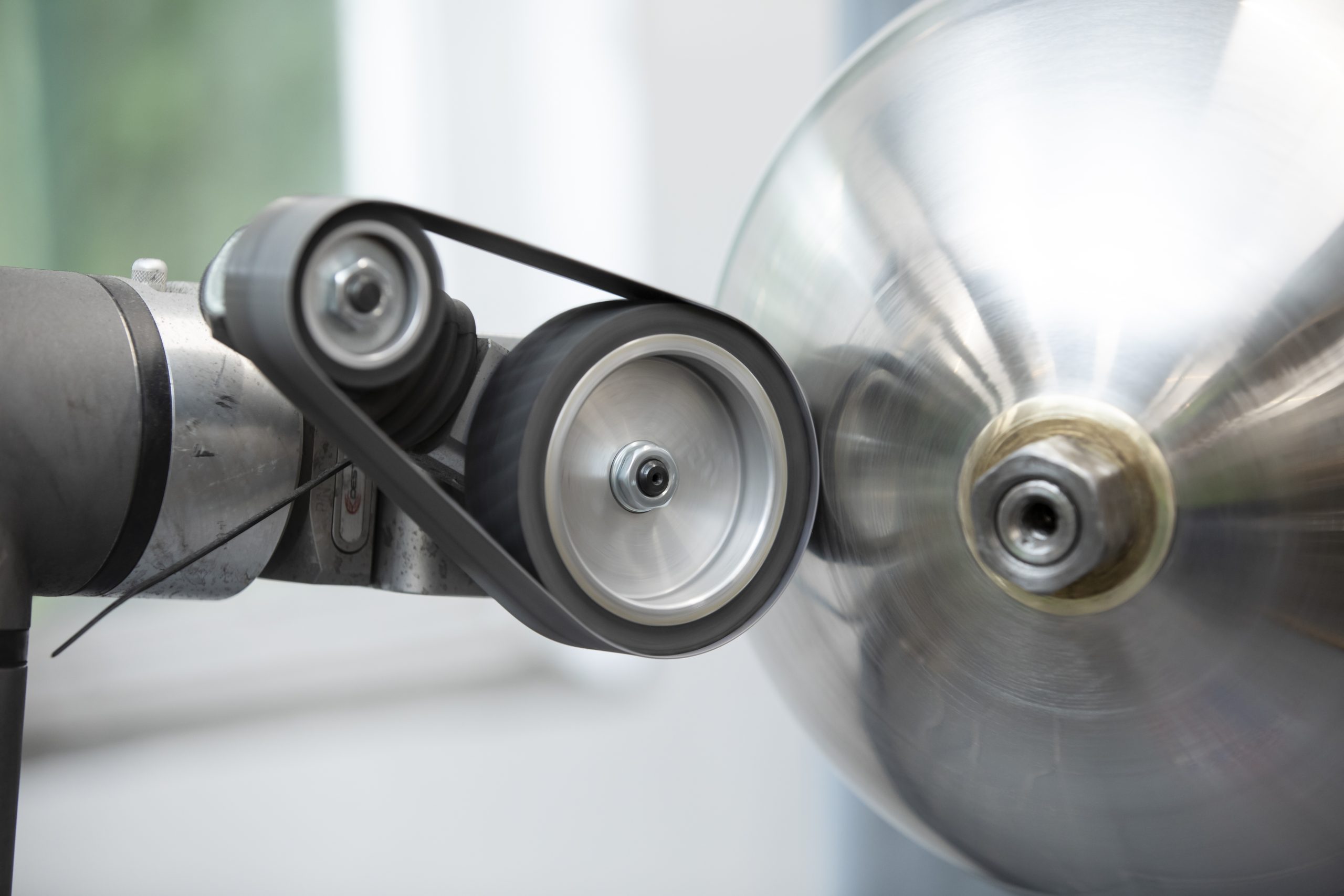
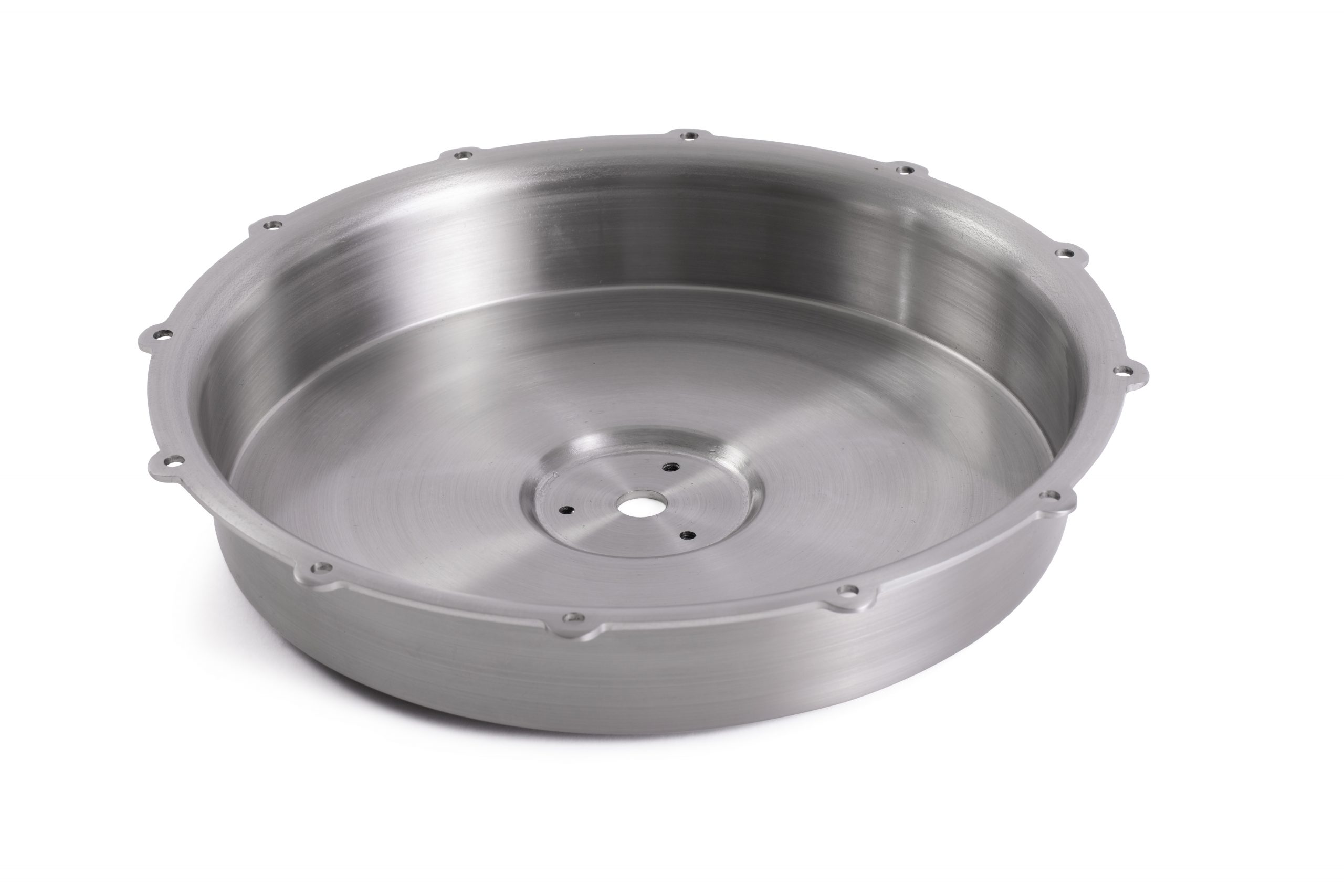
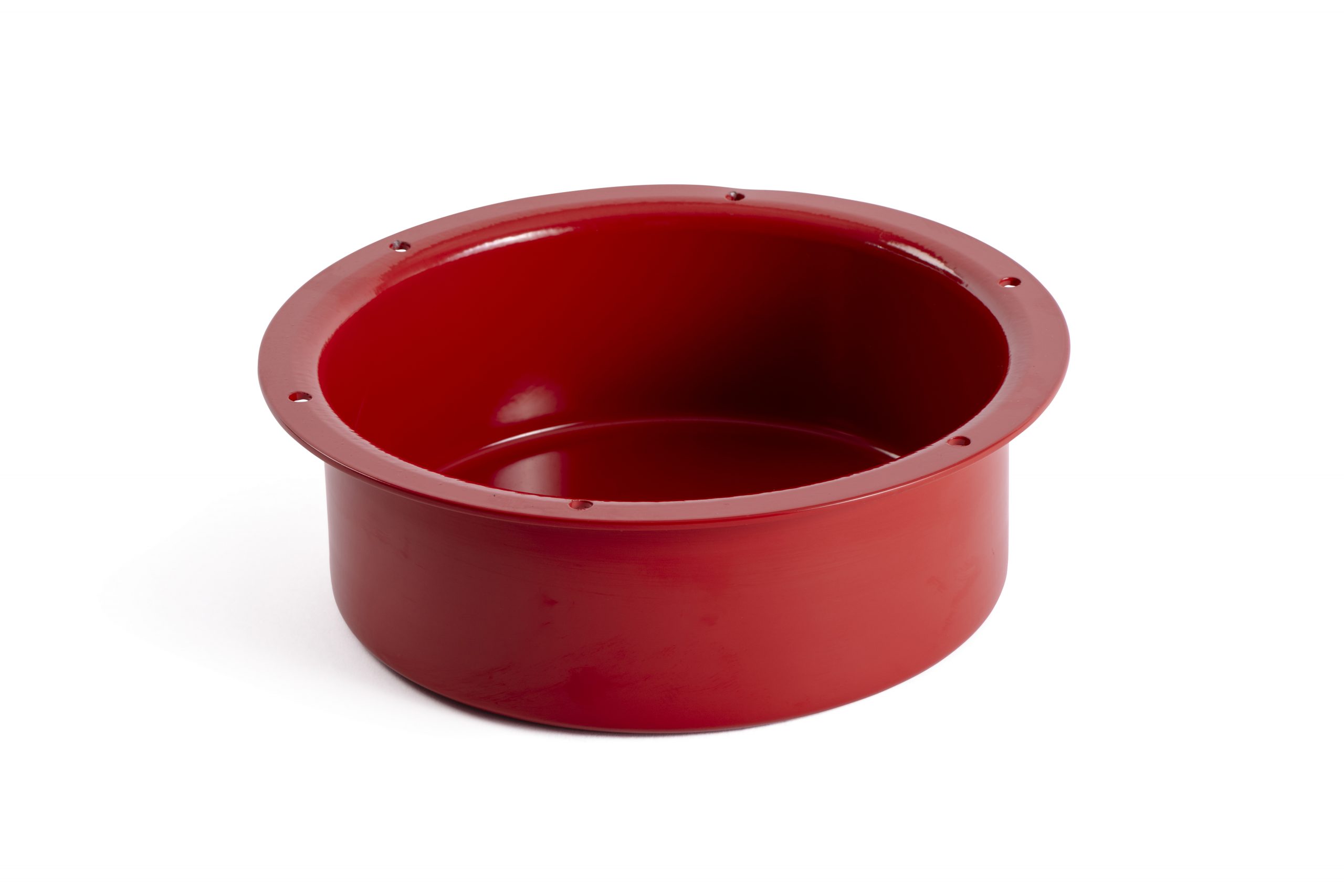
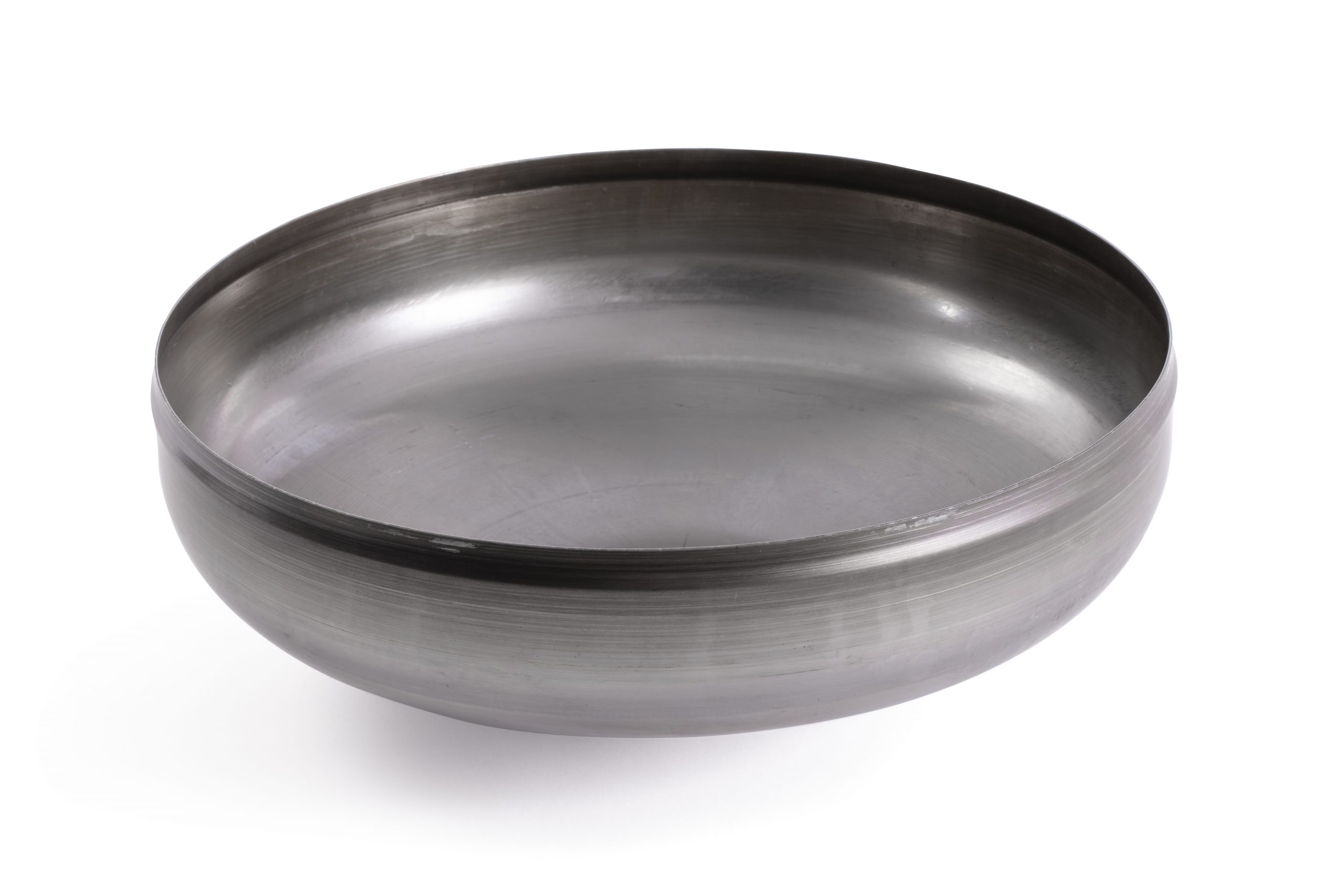
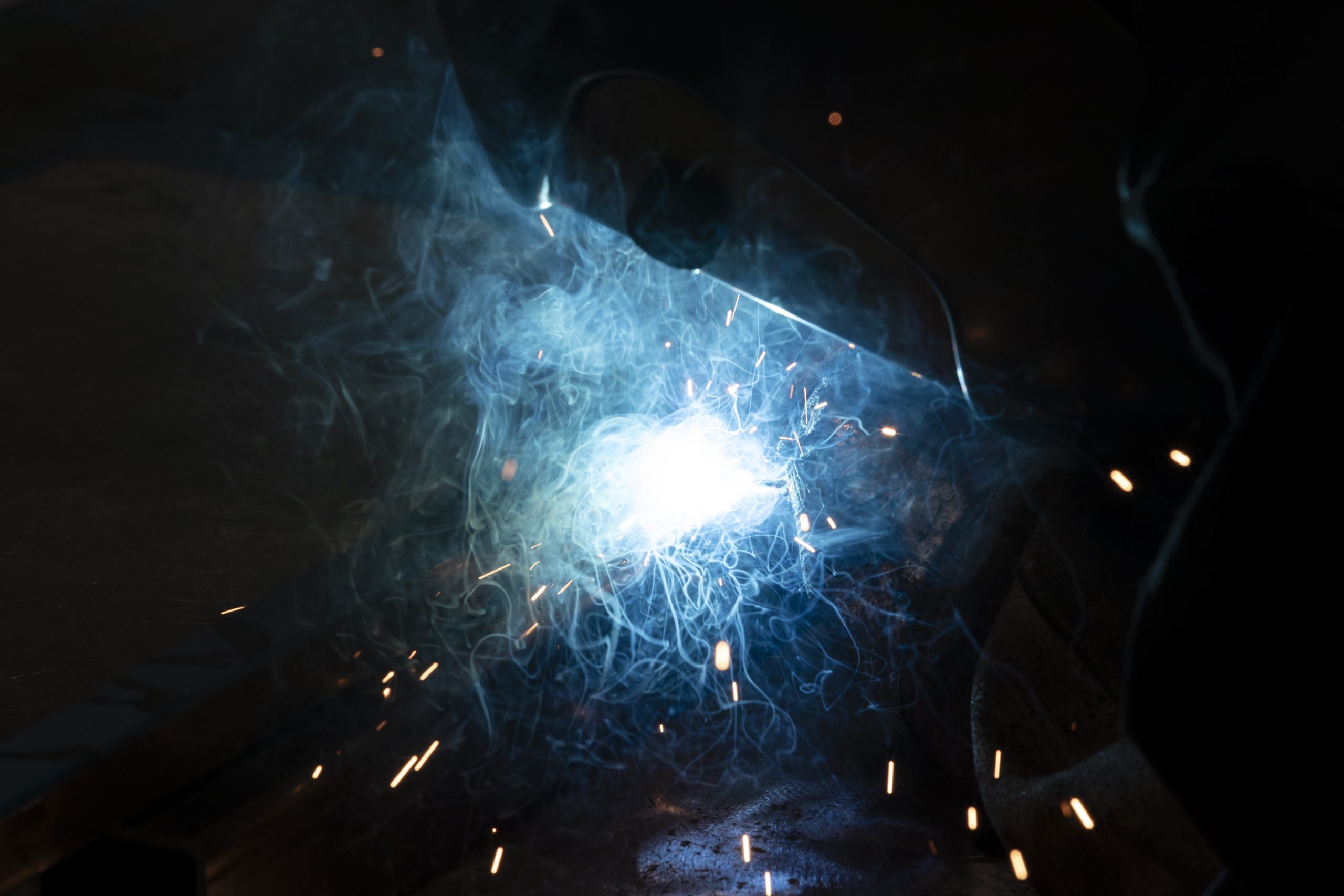

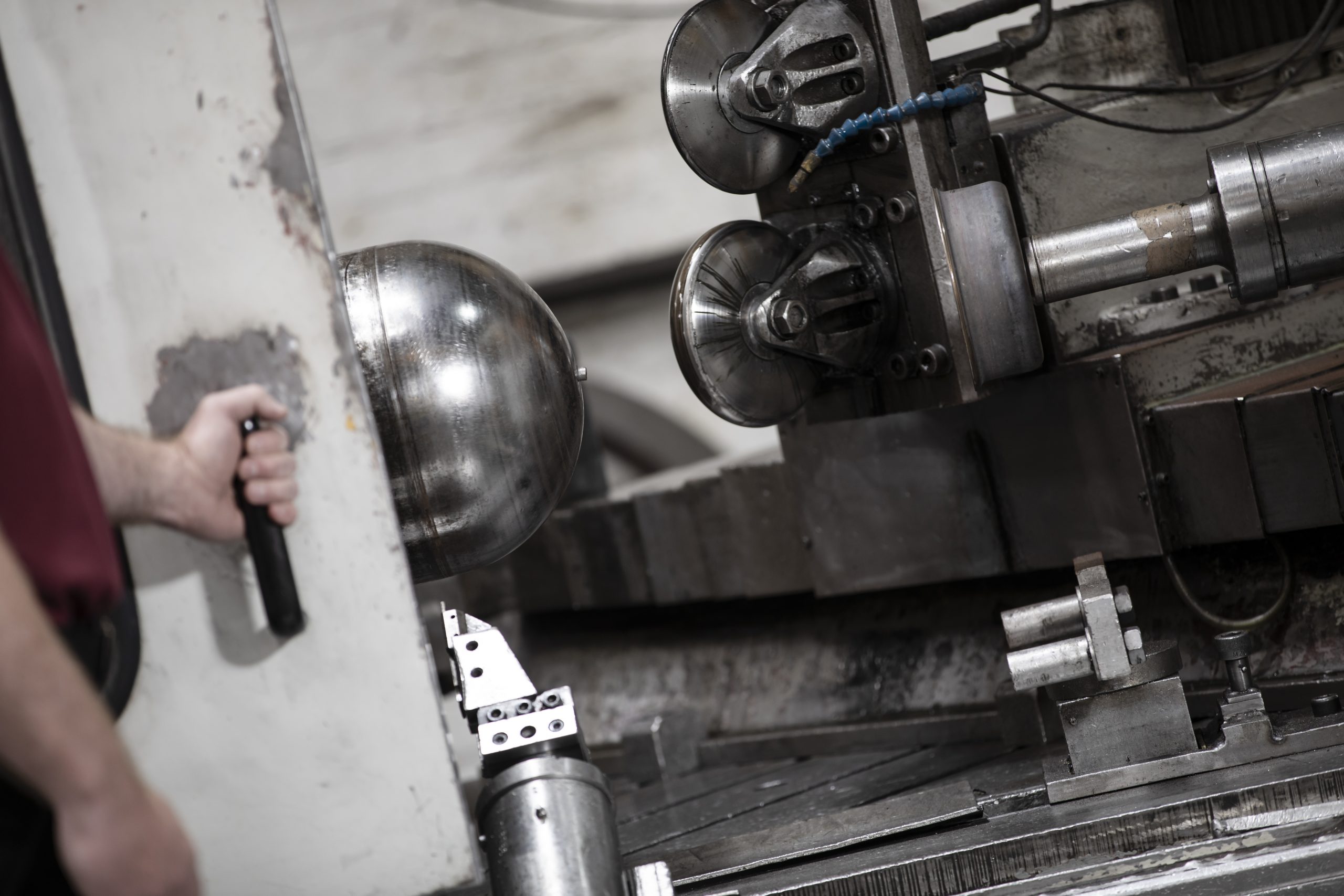
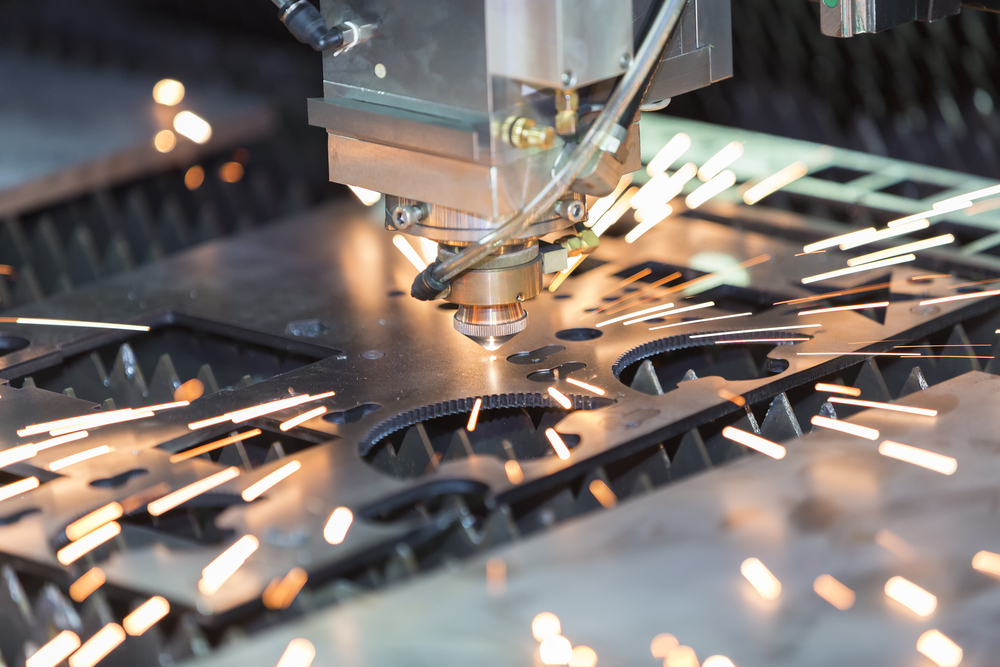
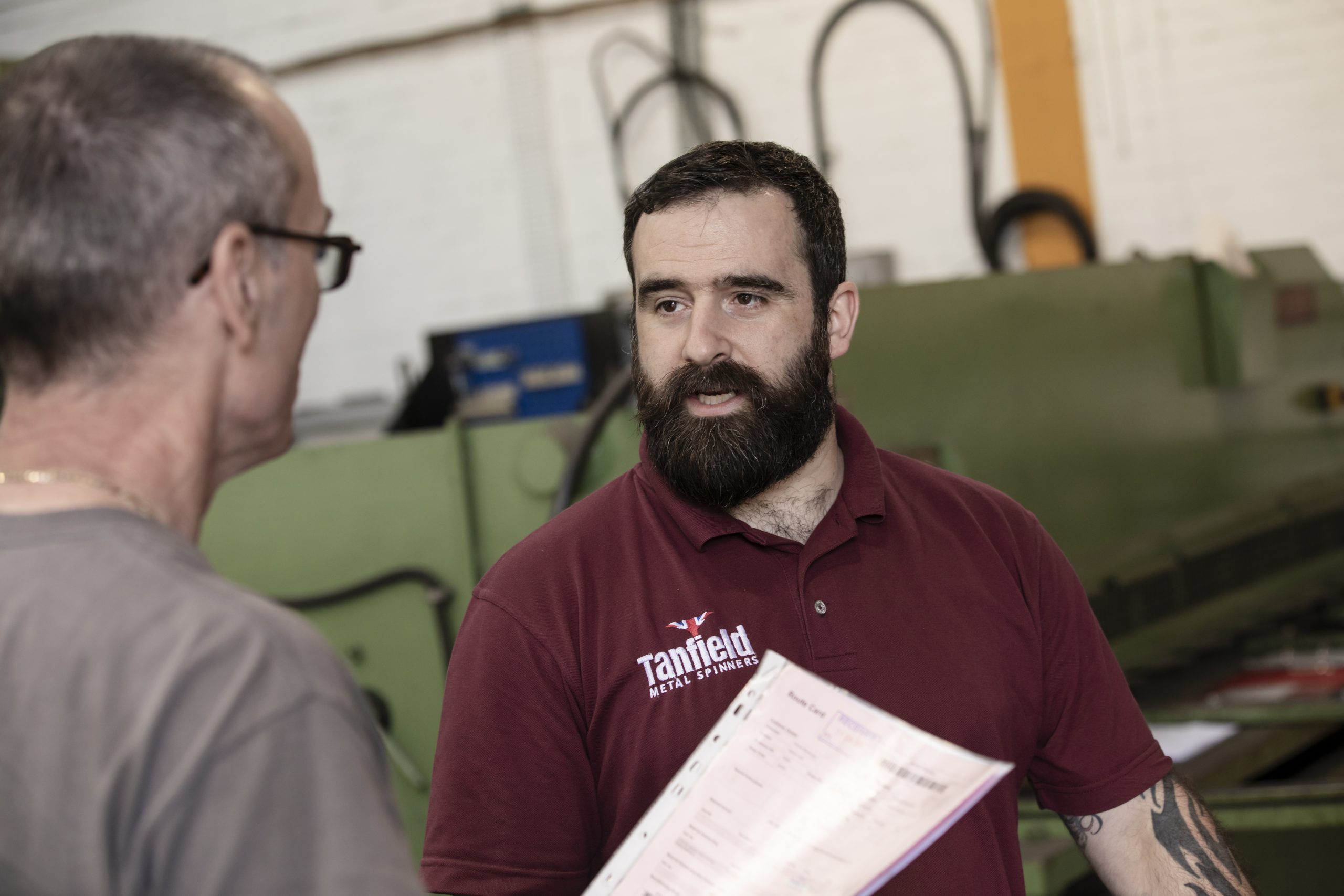
Sectors
Metal spinning is a flexible and precise process. As a result, it has manufacturing applications in a wide range of important industries. We cater for businesses in the following sectors:
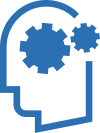
Expertise
We believe that collaboration is key! That’s why we work closely with you to ensure that we provide solutions tailored to your unique needs and requirements.
No drawing? No problem, our expert team will provide one free of charge.

Flexibility
Since 1984 we’ve built an enviable first-class reputation based on the highest quality workmanship with the best advice available on metal thickness and tolerance levels.
We have an open-minded approach to satisfying our customers engineering needs.

Responsive
We pride ourselves on deeply understanding our customers’ needs quickly and effectively. 90% of our quotes are provided within 24 hours.
We take great pride in our excellent on time deliver performance, helping our customers projects run on time, every time.
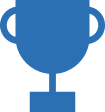
Competitive
With our large range of fully automatic spinning lathes, in our 35,000 sq-ft facility, you can be assured of receiving the best solution for your application, along with the very best lifetime value.
We are very proud to say we are a 100% ‘made in Great Britain’ manufacturer.
Top things we get asked
Metal spinning also known as spin forming is a cost-effective process used to form conical, hemispherical, and cylindrical shapes. A starting blank (flat disk) is spun over a tool in a series of sweeps by a forming roller, the metal is progressively shaped onto the tooling to produce the desired shape, producing the finished part.
In general, metal spinning offers flexibility with low tooling costs and is widely used for either low or high-volume production. Depending on the application, spinning can offer major benefits which often makes it an ideal choice.
Tanfield Metal Spinners will quote for work up to a radius of 2.4 meters 10mm thick. We also partner with an international spinning company for anything above Tanfield’s current capabilities.
Our technical engineering department will supply a drawing on your request for a quote, at no additional cost, which can be signed off before order.
All parts manufactured from Tanfield will have full traceability, all materials that require certification will be automatically sent to our customers on completion of the order.
The following materials can all be spun. If your project requires a different metal, we can work with many more specialist materials, however these will typically require heat (annealing) to meet your specifications.
Aluminium
Brass
Carbon Steel
Copper
Corten
Duplex
Hastelloy Alloys
Mu-metal
Nimonic
Nirosta
Silver
Stainless Steel
Titanium
Zintec
Tanfield prides itself on maintaining a 3–4-week lead time where possible, if tooling is required this can extend the lead times.
Tanfield’s standard tooling stock is the largest in the country and we invest in it on a yearly basis.
If your project requires new tooling Tanfield will look at the most cost-effective way to service our customer’s needs.
Delivery is always a next day service; this can be upgraded to before 12 at an extra cost.