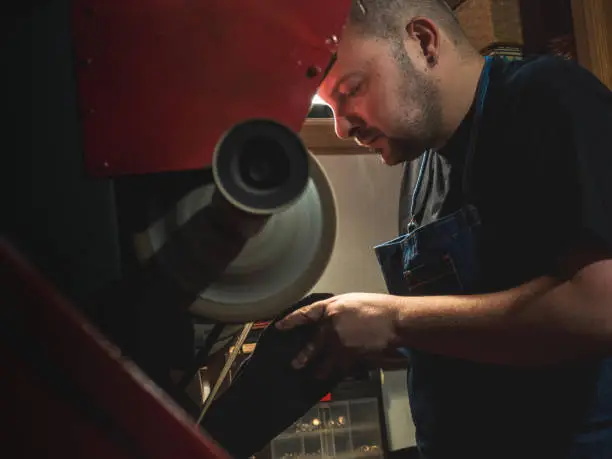
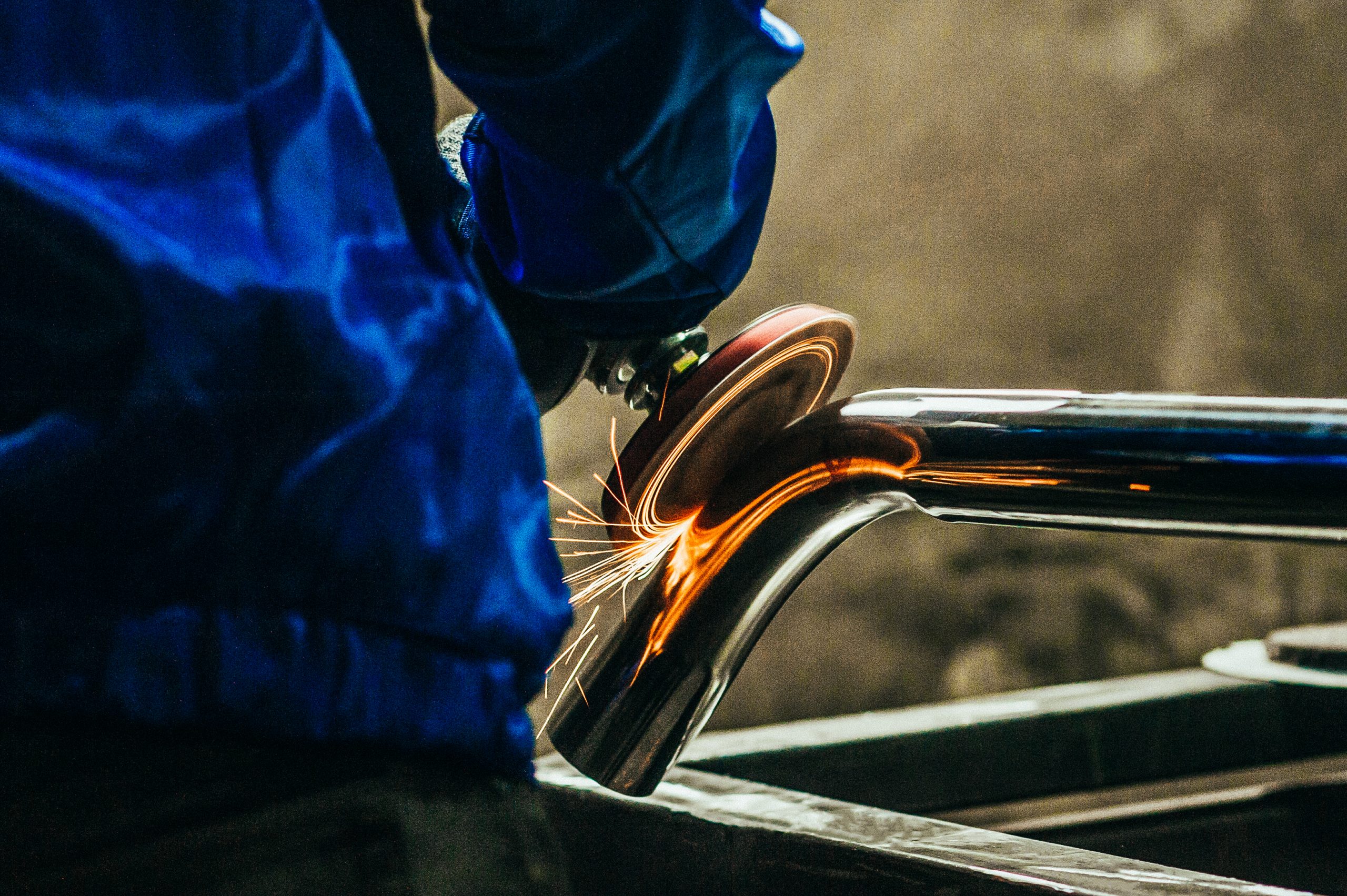
What metal finishings can be used on metal spun parts?
If you think your metal spinning project requires additional finishing, it’s necessary to consider what options are available. This is because each finishing process has different steps, benefits, and costs associated with it. As a result, while one type of finishing might achieve decent results, it could be that a different process is better suited to your project goals. In this article, you’ll find information on the main metal finishings used on metal spun parts.
Benefits of finishes for metal parts
The aim of most metal finishing processes is to alter the surface of the material to instil beneficial properties. This could be for corrosion resistance, longevity, aesthetic appeal, ease of cleaning, or to meet an industry specific regulations and quality controls. It is therefore effective at making sure that the product can complete its intended function over a long period of time. Whatever properties are added through finishing, the process will increase the value of any metal spun parts it’s used on.
Types of finishings for metal spun parts
As mentioned above, there is a great deal of flexibility when it comes to what can be achieved with metal finishings. This is due to the range of different options available to manufacturers.
Polishing
Metal polishing can itself be accomplished in a variety of ways to achieve a shiny smooth finish on the metal. Polishing can also improve durability and chemical corrosion resistance. Common examples include powder polishing and buffing. At the time of writing, our top selling finish is a 250grit rotary polish.
Electropolish
Electropolishing can be used to deep clean the parts after spinning. This involves submerging the metal part in an electrolyte bath and running a current through it.
Anodising
This finishing technique uses an electrochemical process to add a metal oxide layer onto the part. This allows for colouring and decoration, whilst enhancing corrosion resistance. As a result, anodising is frequently applied to aluminium parts used in the automotive and aerospace sectors.
Pickling & Passivating
First, the pickling process is designed to remove surface impurities from the metal, preparing it for other finishes or treatments. These impurities can include rust, contaminants, or scale. Passivation often following pickling, as it forms a protective oxide layer on the part which can only be effective if the metal is completely clean. This finish allows metal spun parts to maintain their shape and integrity in harsh environments.
Expert metal spinners UK
When we produce a quote for a metal spinning project, our metal spinners might recommend a certain type of finishing be applied to your metal spun parts. Although this will add time and a slight extra expense, this is done solely to help you get the best outcome for your project. Equally, we won’t be afraid to tell you when using a metal polisher is unnecessary. Our technical knowledge also extends to materials, cold forming metal, fabrication, and the industries we typically support. Get in touch with a member of the team today.