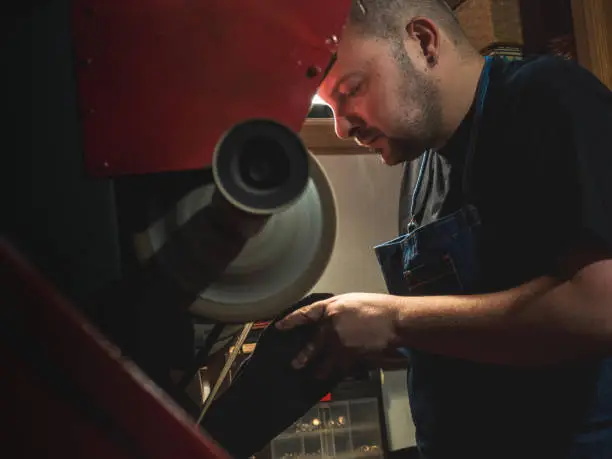
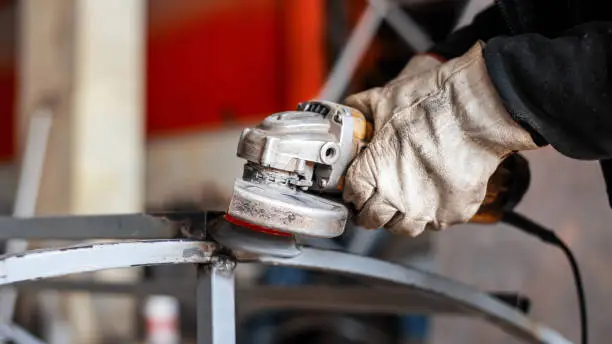
The Metal Polishing Process: Achieving Precision and Excellence with Tanfield Metal Spinners
The metal polishing process is essential for producing metal products that combine both aesthetics and functionality. At Tanfield Metal Spinners, this process transforms raw metal into components with polished, durable finishes that meet precise specifications across various industries. Whether it’s removing imperfections or enhancing the durability of metal components, our metal polishing services are tailored to provide lasting value.
What is Metal Polishing?
Metal polishing is a specialised finishing process that smooths the surface of a metal workpiece and enhances its appearance, often creating a reflective, mirror-like finish. This process involves applying abrasive materials and compounds that gradually refine the surface until the desired level of smoothness and shine is achieved. In industrial applications, metal polishing goes beyond aesthetics. It enhances surface quality by removing oxidation, corrosion, and other imperfections, improving a component’s functionality and extending its lifespan.
Metal polishing is crucial in sectors where both appearance and performance matter. In the aerospace industry, for example, polished metal components help reduce drag on aircraft. In the food industry, polished surfaces meet stringent hygiene requirements, making them easier to clean and less likely to harbour bacteria. Tanfield Metal Spinners uses manual expertise and advanced machinery to achieve optimal results in every metal polishing project.
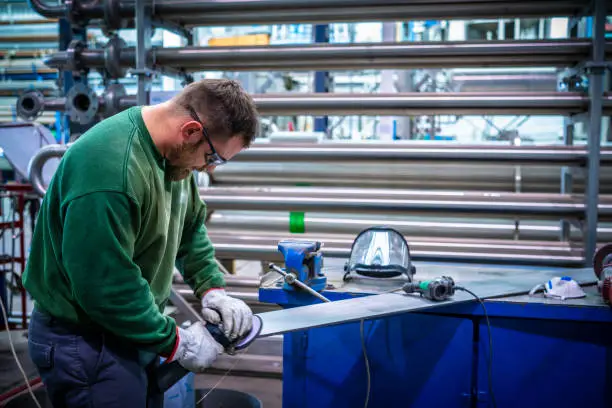
The Science and Technique Behind Metal Polishing
The metal polishing process involves a series of carefully controlled steps, each using different grades of abrasives to achieve progressively finer finishes. This begins with coarse abrasives that quickly remove surface imperfections, finer abrasives that refine the surface, and finishing compounds that produce a high-gloss finish.
Metal polishing can be performed dry or wet, with lubricants applied as needed to achieve specific results. Wet polishing is often used to minimise heat generation and reduce dust, while dry polishing is ideal for specific applications where speed and efficiency are priorities.
Tanfield Metal Spinners’ polishing techniques vary based on the type of metal and the desired end result. For instance, aluminium requires a different abrasive approach than stainless steel due to its softer nature. Using the wrong abrasives or techniques can result in surface damage, which is why Tanfield’s experienced technicians customise the process for each project, ensuring precision and high-quality results every time.
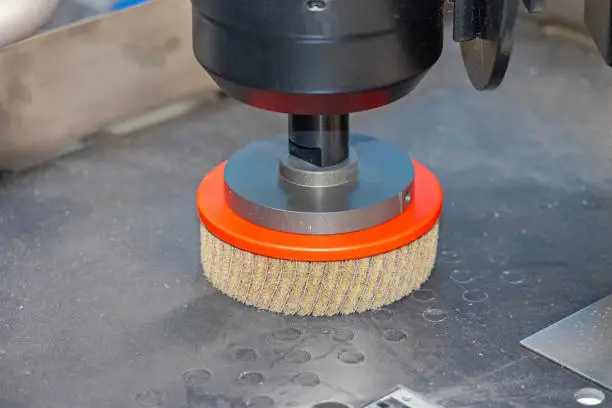
Our Metal Polishing Process
At Tanfield Metal Spinners, we follow a structured, multi-step process that leverages advanced equipment alongside traditional techniques. This allows us to deliver polished metal components that meet the highest standards of quality and consistency. Here’s an overview of our process:
1. Surface Preparation: The process begins with a detailed inspection of the workpiece’s surface. Any visible imperfections, such as scratches or dents, are identified and addressed. We then select the appropriate abrasive material for initial polishing, which removes the roughest imperfections and prepares the surface for further refinement.
2. Gradual Refinement: We switch to finer abrasives once the initial rough polishing is complete. This stage is crucial for achieving a smooth, non-marked surface that prepares the metal for the final polishing stages. Our technicians carefully monitor each step to ensure that the right amount of material is removed, preventing any unintended reduction in thickness.
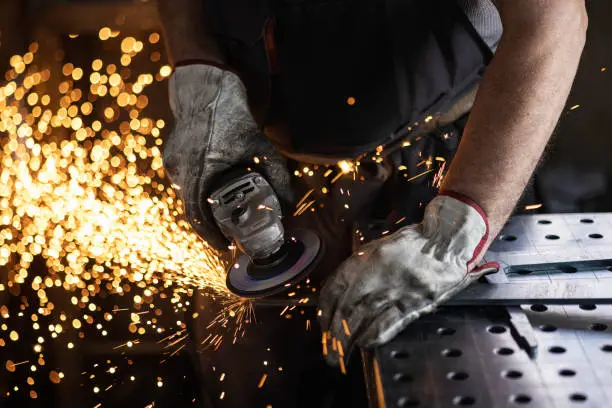
3. Application of Lubricants and Final Polish: For a superior finish, our polishers use a range of lubricants—including wax, oils, and kerosene—depending on the material and desired finish. These substances protect the metal and help achieve a flawless, reflective surface. The final polish often involves polishing compounds that bring out the metal’s natural shine, giving it a mirror-like quality.
4. Quality Assurance: Each polished product undergoes rigorous quality checks to meet Tanfield’s high standards. Measurements are taken to verify dimensional accuracy, while surface inspections confirm that the finish is free from defects. Consistency and precision across every project are priorities for our team, ensuring that our clients receive components that meet their exact specifications.
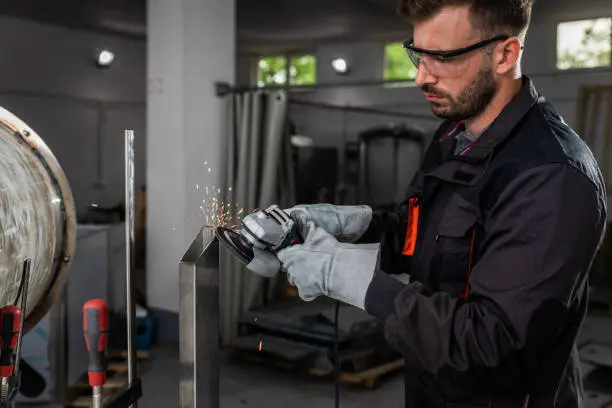
Benefits of Metal Polishing
The advantages of metal polishing extend well beyond visual appeal. Polishing metal brings numerous benefits, enhancing both product performance and longevity. Key benefits include:
- Aesthetic Enhancement: A polished metal surface projects quality and attention to detail, particularly important for consumer-facing products where appearance is a key factor. From lighting fixtures to kitchenware, polished metals add a touch of elegance and professionalism.
- Corrosion Resistance: Polishing removes microscopic imperfections that can trap moisture, reducing the risk of corrosion. This can significantly extend the life of metal components exposed to harsh environments or frequent handling.
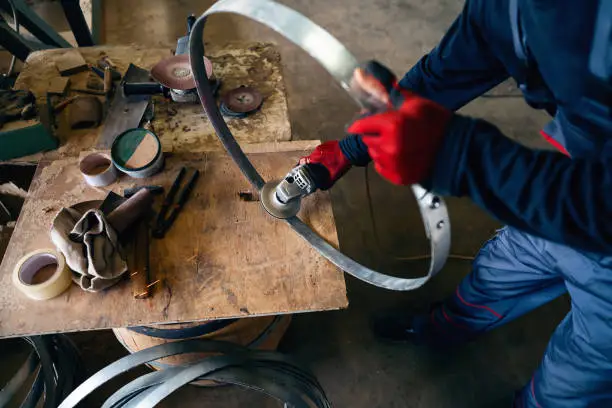
- Improved Hygiene: Polished surfaces are easier to clean and maintain, critical in industries like food processing and healthcare, where hygiene standards are non-negotiable. Smooth surfaces reduce the accumulation of contaminants, making them safer and more sanitary.
- Enhanced Durability: A polished surface is less prone to wear and tear, increasing its resilience under harsh conditions. For example, polished machine components experience less friction, which translates to reduced wear and extended operational life.
- Reflective Qualities: In industries like lighting and automotive, the reflective properties of polished metal can serve functional purposes. Highly polished surfaces reflect light efficiently, enhancing visibility or distributing light evenly.
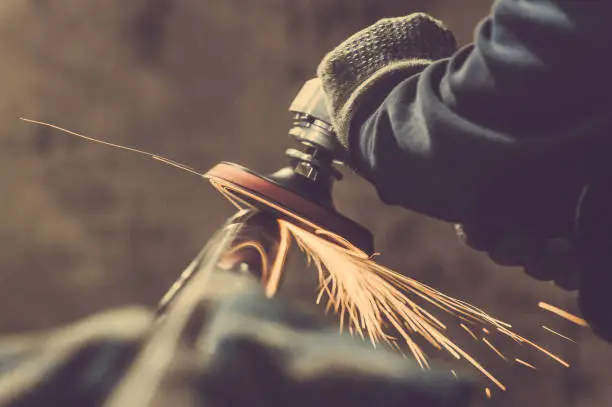
Applications of Metal Polishing Across Industries
Metal polishing is used across various sectors, each with unique requirements for polished metals. Here’s how different industries benefit from our polishing services:
- Food and Beverage: In the food industry, polished metal surfaces are essential for meeting hygiene standards. Equipment such as mixers, tanks, and conveyor belts require smooth surfaces that are easy to sanitise. Our polishing process ensures these surfaces are free from imperfections that could harbour bacteria, making them safer for food contact.
- Aerospace and Automotive: Polished metal components in these industries reduce aerodynamic drag and improve fuel efficiency. The enhanced durability of polished metals also contributes to safety, as components are less likely to fail under stress. Precision and reliability are essential for high-stakes applications like these, and Tanfield Metal Spinners delivers both.
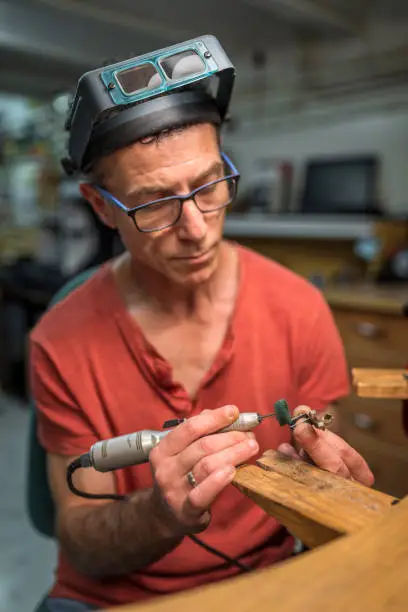
- Pharmaceutical and Healthcare: In medical applications, polished metals are used for surgical instruments and equipment. Polished surfaces enhance the appearance of these tools and improve their performance by making them easier to clean and less likely to accumulate contaminants.
- Industrial Machinery: Machine components that undergo constant friction, such as gears and bearings, benefit from metal polishing, which reduces surface roughness and extends component life. Tanfield’s precision polishing helps minimise friction, heat, and wear in industrial machinery, contributing to greater efficiency and reduced maintenance costs.
- Decorative Applications: Polished metal is often used in architecture, interior design, and consumer goods. The visual appeal of polished metal makes it a popular choice for products like lamps, faucets, and handrails. At Tanfield, we understand the importance of aesthetics in these applications and deliver polished metal that complements high-quality design.
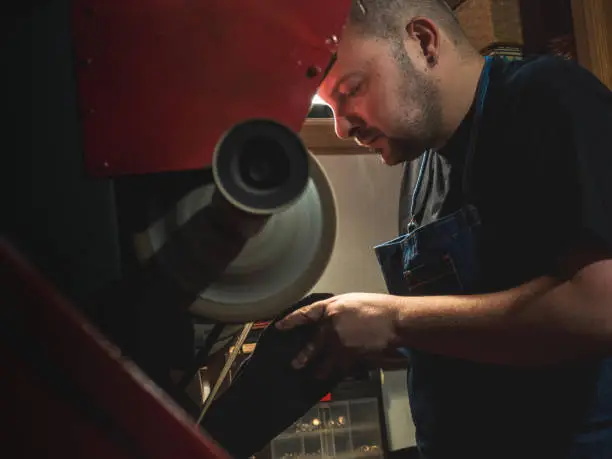
Why Choose Tanfield Metal Spinners for Metal Polishing?
Our dedication to excellence has made us a trusted name in the UK for metal polishing services. Here’s why clients choose Tanfield for their metal finishing needs:
- Expertise and Precision: Our skilled polishers combine years of experience with the latest polishing techniques and equipment, providing a high level of expertise that few can match. Every step in our process is designed to achieve a consistent, high-quality finish.
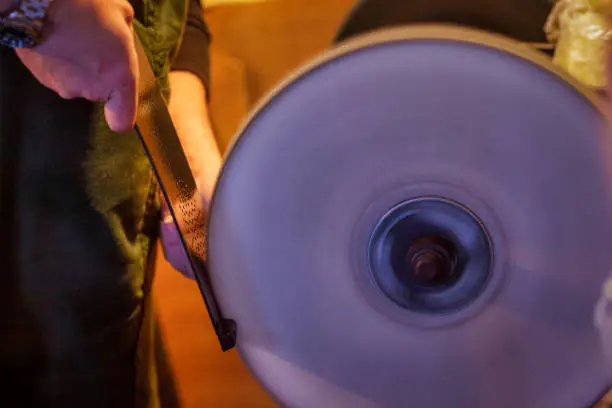
- State-of-the-Art Equipment: Our fully automated polishing system ensures consistent, precise results for any project, whether a small-batch or large-scale. Automation allows us to maintain exacting standards while offering faster turnaround times.
- Customised Solutions: Every project is unique, and we take a personalised approach to meet each client’s specific needs. By working closely with you, we develop customised polishing solutions that align with your requirements and goals.
- ISO 9001 Certification: Quality is at the core of what we do. Our adherence to ISO 9001 standards ensures that every project meets the highest standards in the industry, giving clients peace of mind that their components will perform as expected.
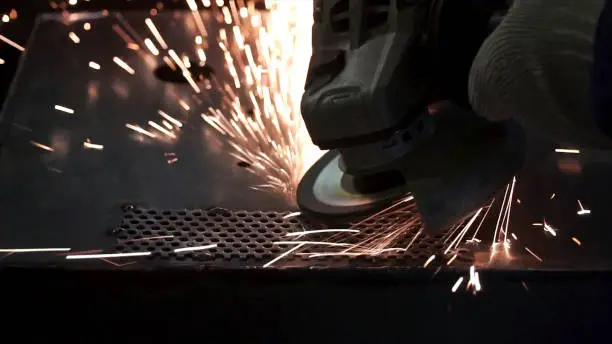
Maximising Performance and Aesthetics with Tanfield Metal Polishing
Metal polishing is essential for any industry where durability, aesthetics, and hygiene are priorities. Tanfield Metal Spinners provides comprehensive metal polishing services that deliver both visual and practical benefits. Our commitment to precision, quality, and customer satisfaction ensures that each project meets our clients’ exact specifications.
Contact us directly for more information on our metal polishing services or to discuss a specific project. Let Tanfield Metal Spinners help you achieve the perfect finish for your metal components, maximising both performance and appearance.