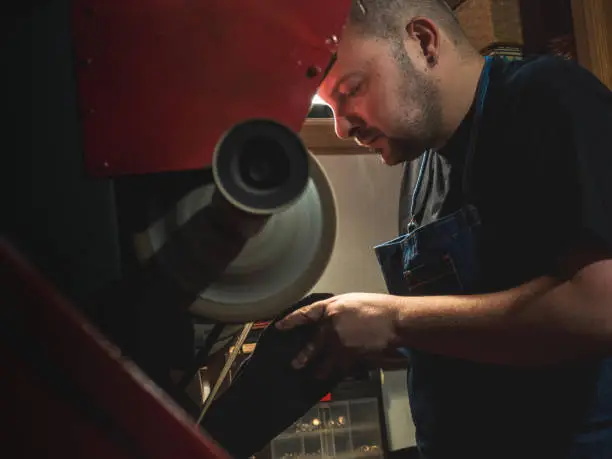
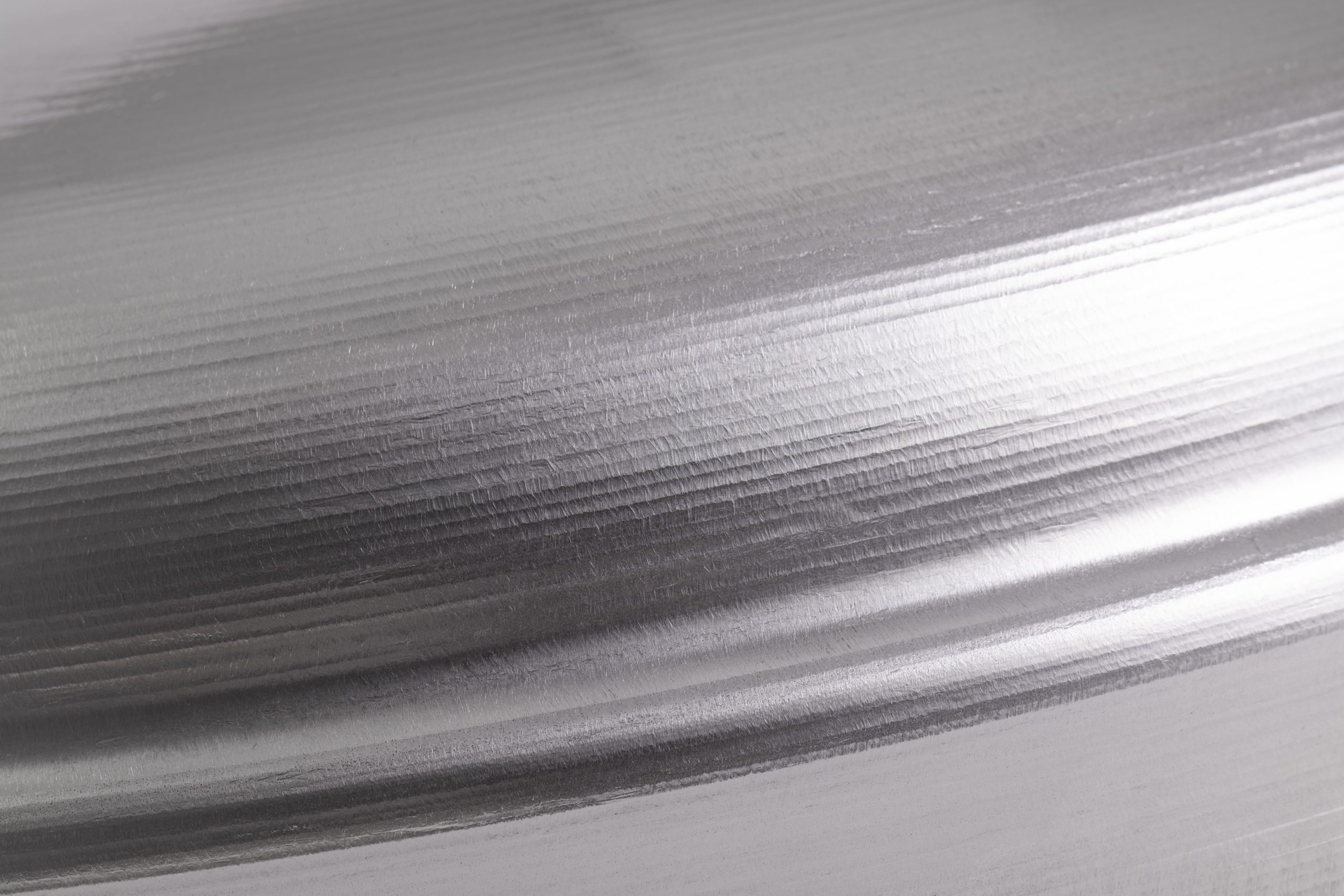
The joggling process explained
There are several important processes that can be involved in creating bespoke metalwork for various clients and industries, one of which is joggling. The term joggling relates to a bending technique used on dished ends and can be an essential technique for the fabrication of a dished end onto a cylinder. In this guide we will be exploring the key steps involved in the joggling process and its importance within Tanfield’s metal spinning services.
What is joggling and why is it important?
The joggling process involves modifying the edge of a metal component to create a step or offset. This step or offset, known as a joggle in metal spinning, is typically formed along the periphery of a curved or dished end.
This image offers a great example of a joggled dished end created by Tanfield.
The purpose of joggling is to facilitate the assembly and welding of components, ensuring a secure and precise fit. Joggling serves multiple important functions including:
- Accurate welding – the joggle joint in metal spinning enables the welding process to be more precise and accurate. This is due to the secure connection between the joggle and the structure it is connected to.
- Improving the fit between parts – the joggling process helps to reduce gaps and ensure a tight joint between the components. As a result, the metal product will be long-lasting and can perform its function effectively.
- Reduce stress concentrations – a joggle can help distribute the stress more evenly across the joint, which reduces the risk of stress concentrations.
- Minimised distortion – joggling helps to reduce distortion during the welding process. Distortion can be a concern in metal fabrication, and a well-designed joggle can help control and mitigate the metal changing shape.
- Enhancing the structural integrity – joggle joints can reinforce the structural integrity of the newly assembled parts. This is vital for certain industries and product types like pressure vessels and tanks where a secure, leak-free seal is paramount.
- Better quality control – metalwork demands the highest level of quality control, and the joggling process is no different. Often a joggled component will need to meet specific dimensional and structural requirements, and with Tanfield’s strict Also, our joggler is CNC which ensures repeatability of our high quality process.
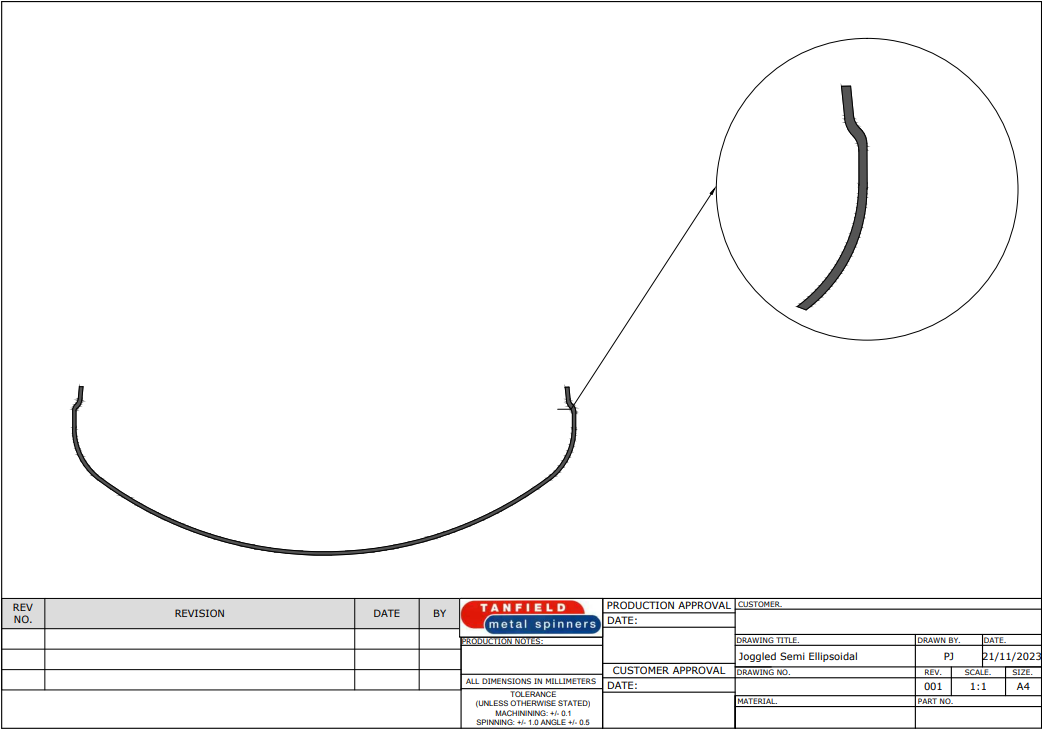
The joggling process
The specific details of the joggling process can vary depending on the type of part being fabricated and the industry requirements. However, we can provide a general overview of the steps involved in joggling.
1) A previously spun metal spinning (dished end) is placed on the joggler and clamped.
2) Using the formers, the metal is bent by around 20-30 degrees, often in opposite directions. A joggle press will clamp the spinning between two dies and apply pressure.
3) The part is released and bent again until the desired shape is accurately formed for the joggle. Depending on the type of joggle it may need to go through another joggling tool.
4) The exact depth and dimensions of the joggle depend on specific engineering requirements.
The joggling process has low production costs and is very versatile in creating different shapes, which make it a commonly used technique in the world of metal spinning. It is particularly important for industries where precision and reliability in assembling the metal components are key for long-term functionality, rigorous use, and safety.
Conclusion
Tanfield Metal Spinners are experts in a wide range of high-quality metal spinning processes including joggling. All our metal spun products are created to meet industry standards and ensure our clients receive the best possible quality of products that meet their specific requirements.
Contact us today by either filling out our online form, emailing us at talktoanexpert@metal-spinners.com, or giving us a call on 01914193377 to discuss your project needs and how our specialist team can help.