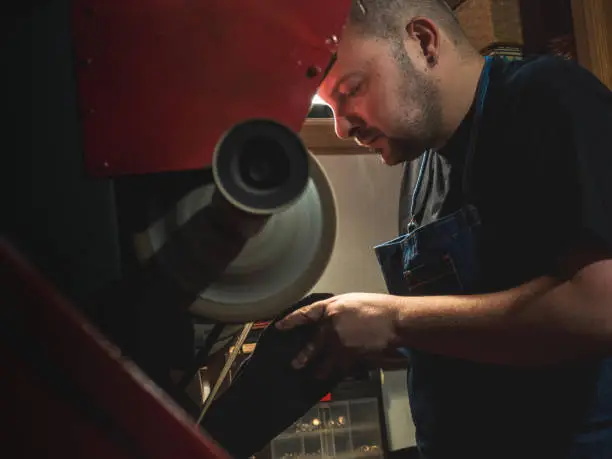
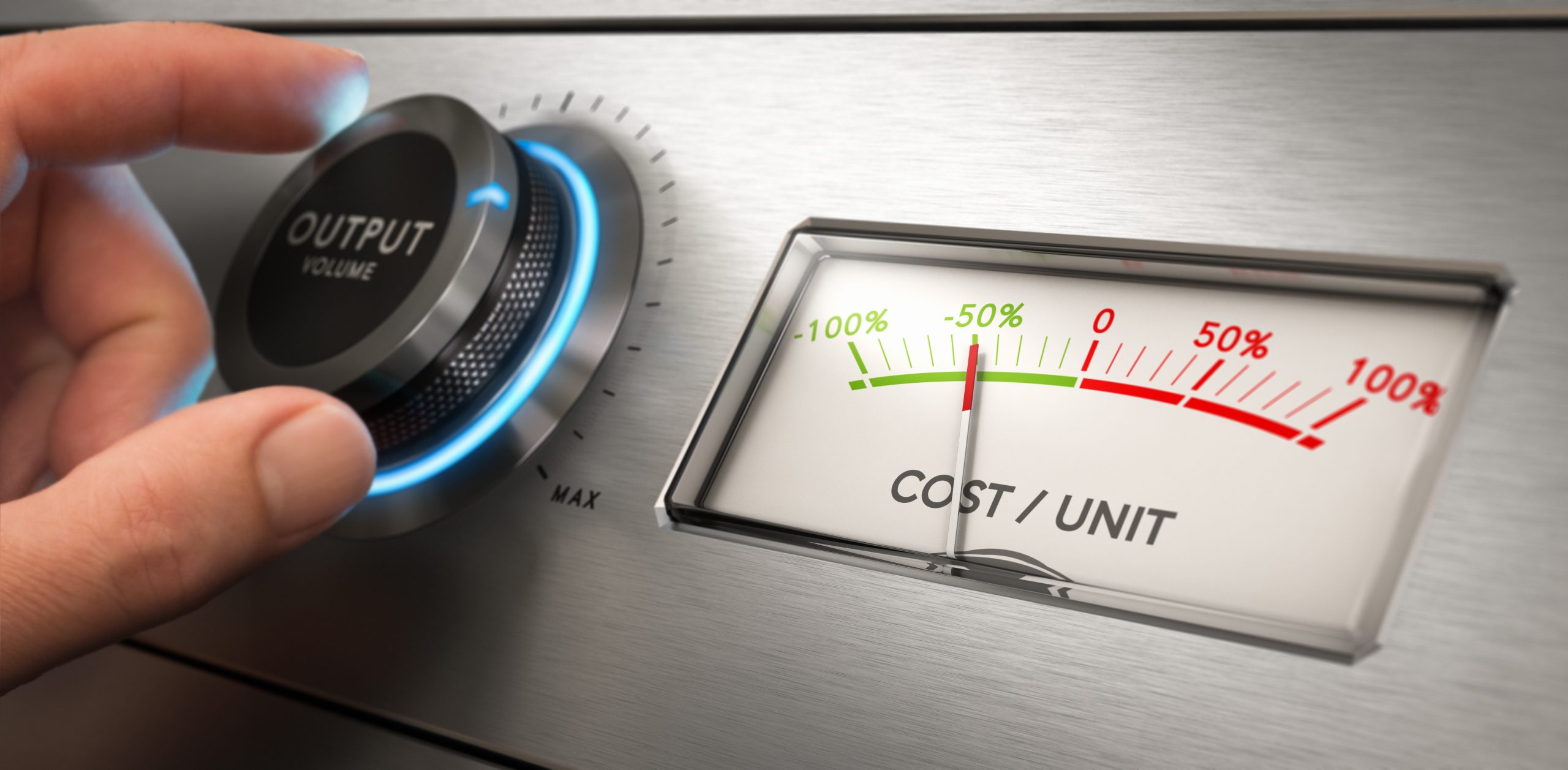
How to save costs with metal spinning
Metal spinning is a unique metal forming process that has application in a wide range of technical industries. This includes cryogenics, food production, agriculture, and more. Regardless of the product application though, outsourced metal spinning can provide significant cost savings when compared with more traditional metal forming and fabrication techniques. Below, we break down the areas of production which can benefit from the use of metal spinning.
What makes the metal spinning process different?
Metal spinning, also known as spin forming or spin turning, is a cold forming process that shapes metal discs into other shapes. This is typically done using specialist lathe machines that are operated by a highly trained metal spinner. The size and type of tool affixed to the metal spinning machine will determine what shape part is spun. The process is accurate and highly repeatable, allowing for large scale production of metal spun parts.
Cost efficiencies of metal spinning
Metal spinning minimizes material waste compared to traditional machining processes. The spinning process uses a single, blank circle, reducing the amount of material required for the final product.
Metal spinning often requires less complex tooling compared to other forming methods and while producing a custom tool can be costly, it can be used many times over. In addition, Tanfield Metal Spinners have the largest pre-existing tooling stock anywhere in the UK. As a result, tooling costs can be very low as you are essentially renting a metal spinning tool. This is especially useful for projects that require small batches.
Metal spinning is generally a fast and efficient process, allowing for quicker production rates compared to some alternative metal forming methods. This can result in reduced labour costs and shorter lead times.
Bespoke metal spinning can be completed for small to medium production runs of a design, making it economical for businesses that want to fulfil short-term demand. Equally, the repeatability of metal spinning makes it ideal for large scale production. In these cases, buying materials in bulk adds to the cost efficiency as each sheet of metal can produce multiple metal spun parts.
It’s often simpler and quicker to make changes to the metal spinning process than other metal forming techniques. This reduces downtime during production runs, leading to potential cost savings as a result. What’s more, CNC metal spinning machines have the ability to retain previous settings which also helps with switching between designs.
Metal spinning generally requires less energy compared to other metalworking processes, contributing to lower operational costs. This is especially apparent when compared to hot forming techniques.
Many metal spun parts do not require finishing such as anodising or pickling and passivating. Forgoing finishing processes reduces the time and money costs associated with the final product.
Affordable precision metal spinning
To conclude, metal spinning offers various cost-saving advantages to many kinds of businesses. By considering your specific project requirements, the team at Tanfield Metal Spinners will provide you with a competitive quote. Contact us today to discuss what lead time and budget works for you.