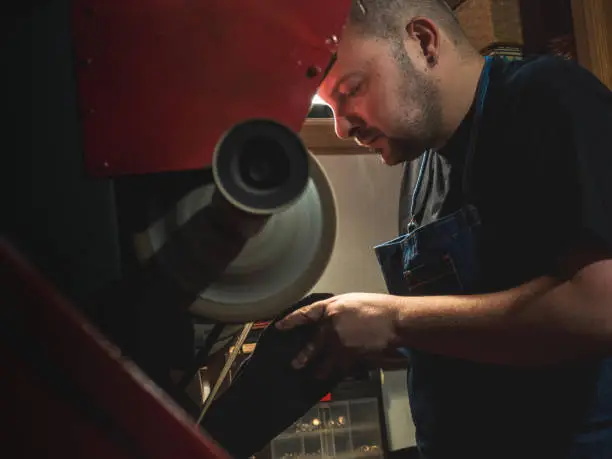
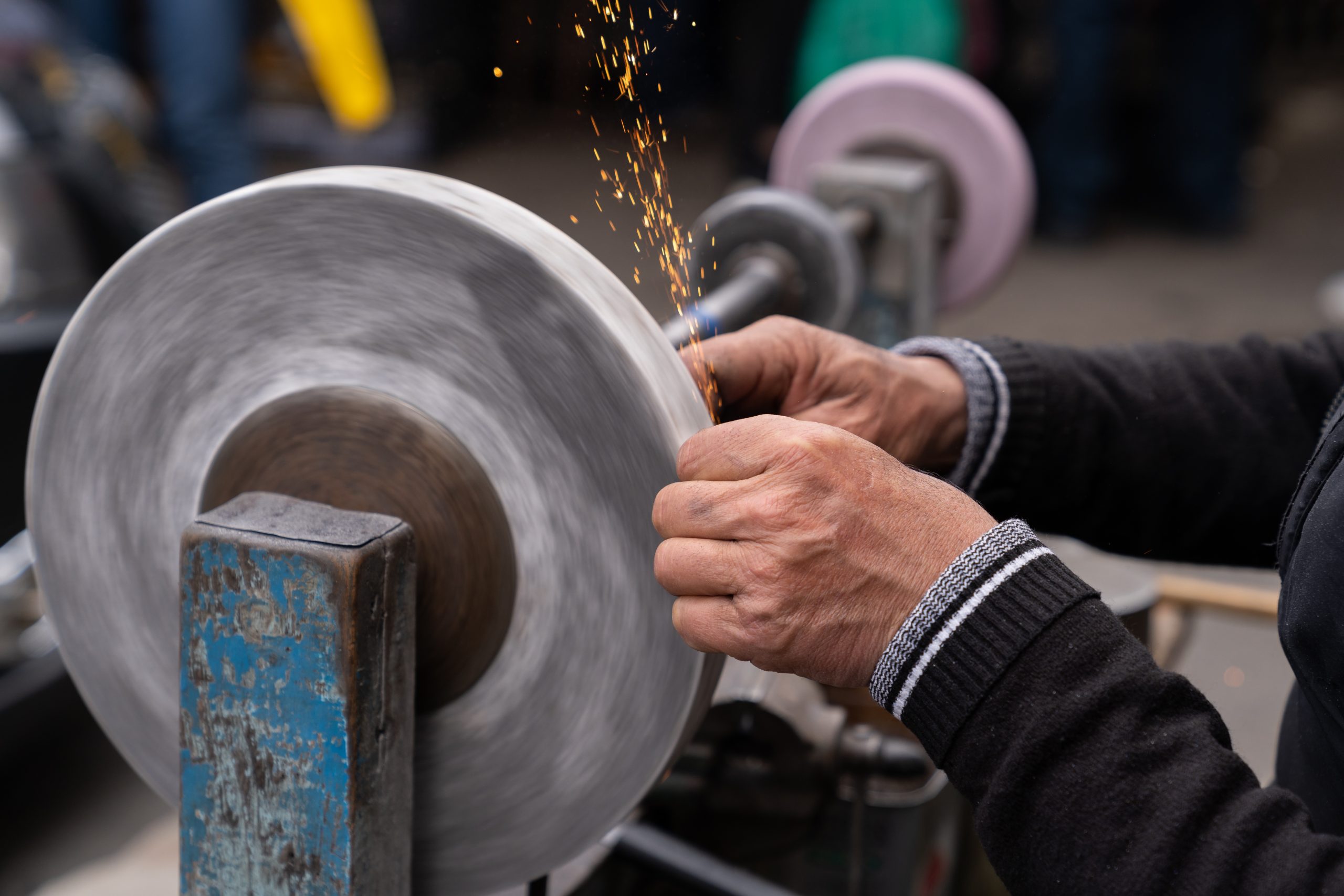
How Automation in Metal Spinning Helps Speed Up Production
Metal spinning began as a manual process, relying on the skill and precision of experienced operators to shape metal discs into functional, symmetrical components. For many years, this hands-on approach was effective for producing small batches and custom parts. However, as demand for larger volumes, tighter tolerances, and faster turnaround times increased, the limitations of manual methods became more apparent.
To meet these growing requirements, the metalworking industry has steadily adopted automation. By introducing technologies such as CNC (Computer Numerical Control) control systems, robotics, and real-time monitoring tools, manufacturers have been able to enhance production speed, improve consistency, and reduce material waste.
This blog explores how automation has changed the world of metal spinning. It outlines the key technologies involved, explains the impact on efficiency and safety, and highlights the advantages automation brings to a wide range of industries.
What Is Automated Metal Spinning?
Metal spinning is a forming technique that shapes flat metal discs, known as blanks, into cylindrical or conical components using rotational force. Traditionally, skilled artisans guided tools manually to create these shapes. While this craftsmanship remains valuable for bespoke projects, automated metal spinning has rapidly become the standard for high-volume, high-precision manufacturing.
Automation now plays a central role in this process. With the use of CNC technology, robotic systems, and real-time monitoring, production has become significantly faster and more consistent. This modern approach removes many of the variables inherent in manual work and provides the reliability required by today’s industries.
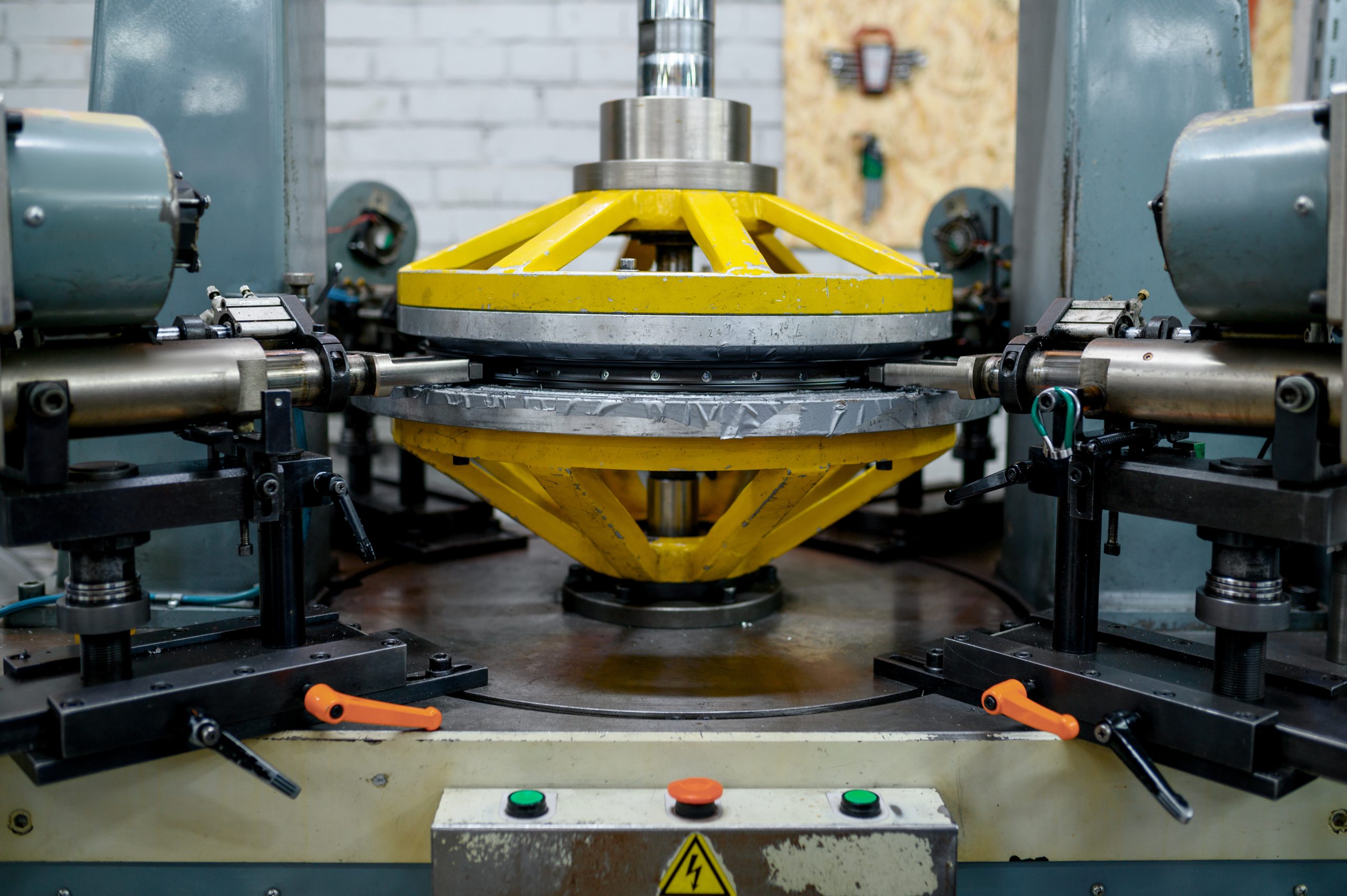
CNC Metal Spinning: Boosting Speed and Production Efficiency
CNC metal spinning has transformed the industry by allowing manufacturers to produce complex geometries with remarkable consistency. A CNC machine operates based on pre-programmed instructions, guiding the lathe and forming tools to precise positions. This process ensures every component is identical, which is essential in sectors such as aerospace, medical manufacturing, and automotive production.
Beyond consistency, CNC spinning also drastically reduces cycle times. These systems operate up to fifteen times faster than manual methods, offering shorter lead times and greater production capacity. At Tanfield, our CNC equipment enables us to meet tight deadlines while maintaining exceptional accuracy across each production run.
The flexibility of CNC programming also allows for rapid design changes. Whether refining a prototype or adjusting specifications mid-project, engineers can reconfigure settings without interrupting workflow. This capability not only improves responsiveness but also supports a faster time to market for our clients.
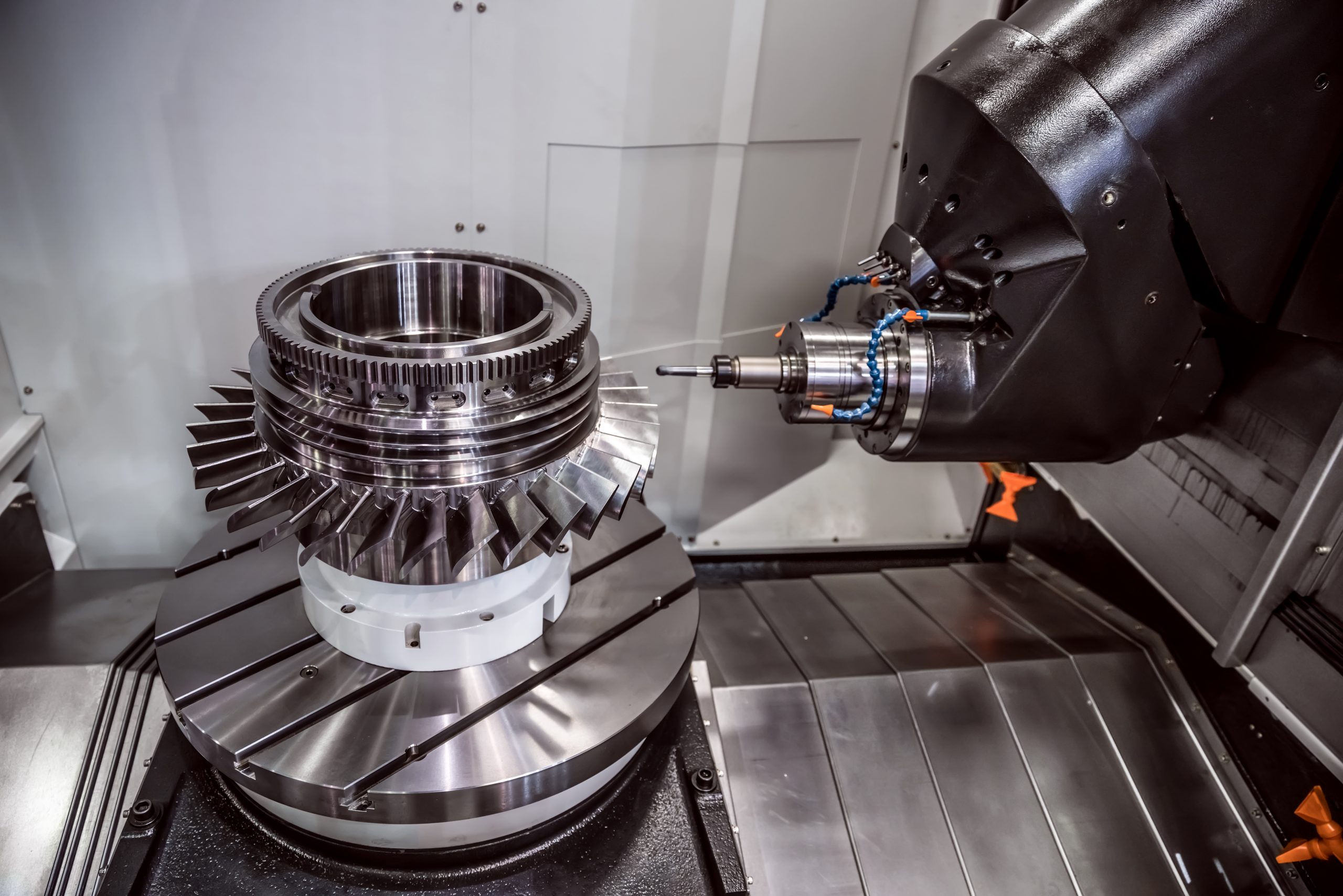
Using Robotics in Metal Spinning to Improve Safety and Productivity
Robotic automation is another critical element in accelerating production. At Tanfield, we use collaborative robots, known as cobots, to manage repetitive or labour-intensive tasks such as loading and unloading blanks, positioning parts, and handling post-process operations. These robots operate alongside our skilled technicians, enabling each team member to focus on more complex responsibilities.
Robotic systems improve overall efficiency by reducing idle time and allowing 24-hour operation without the need for breaks. In addition, automating high-risk tasks minimises the chance of workplace injuries, creating a safer environment for our workforce. The result is a more productive, reliable, and sustainable operation.
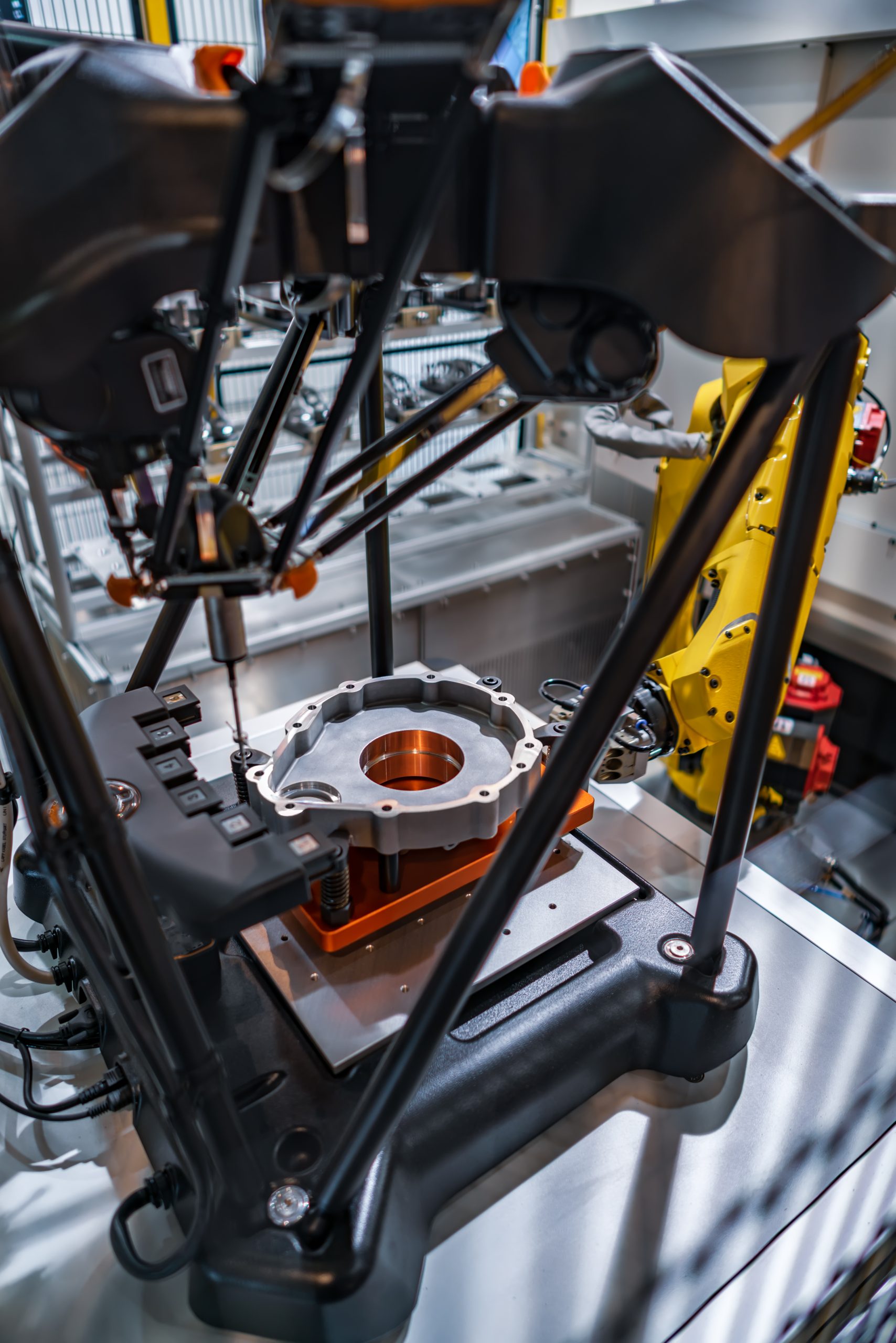
Real-Time Monitoring for Smarter Metal Spinning Operations
Automation does not stop at machinery. Intelligent software tools now monitor the performance of spinning operations in real-time, and sensors collect data on factors such as forming pressure, spindle speed, and temperature. If any metric falls outside the expected range, adjustments are made automatically to maintain quality.
This proactive approach reduces material waste and helps prevent costly errors. Real-time monitoring also supports predictive maintenance by identifying wear or inefficiencies before they cause machine downtime. At Tanfield, we use this data to continuously improve performance and ensure each batch meets exacting standards.
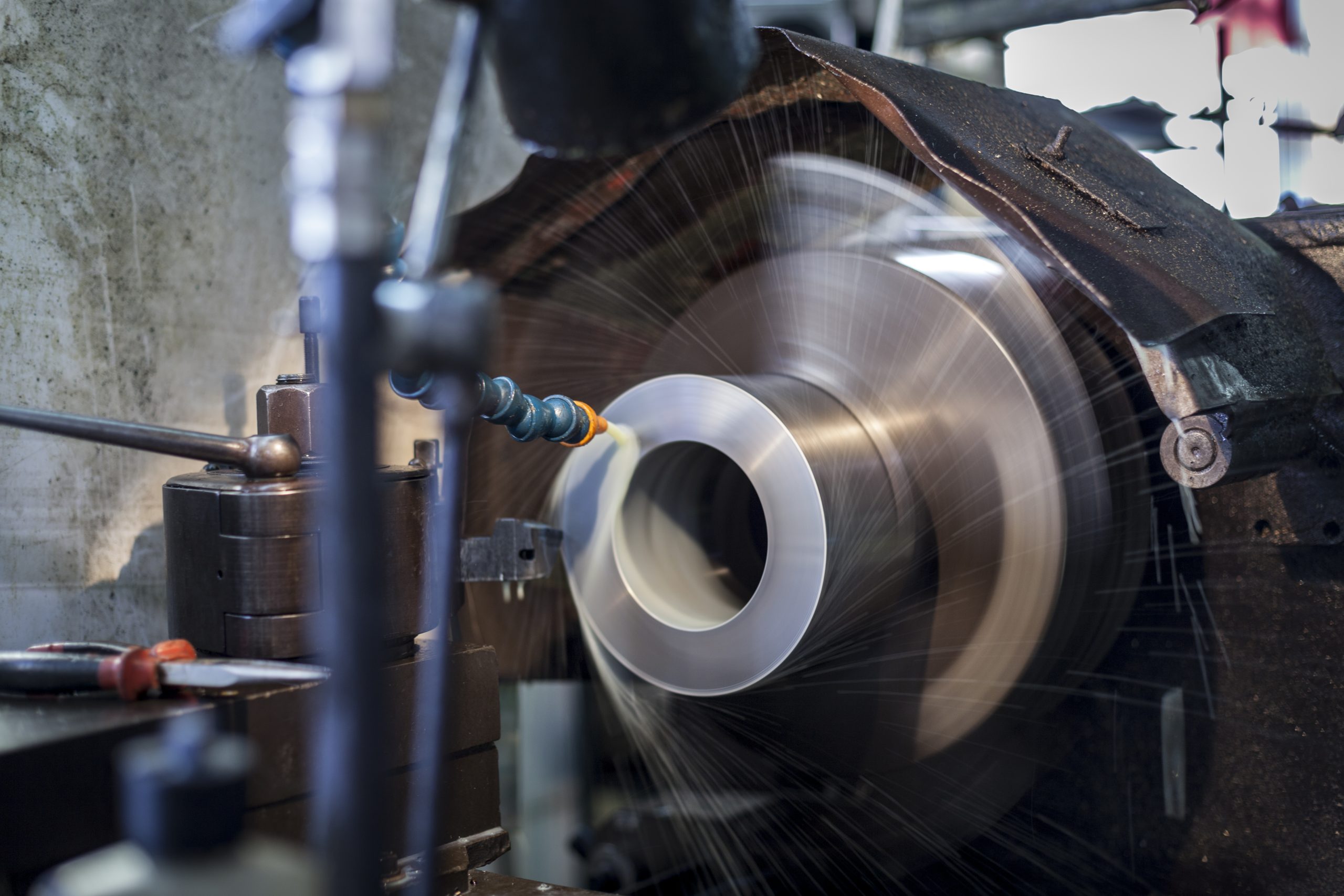
Faster Time to Market with Automated Metal Spinning Processes
Automation drives speed in the forming process and across the entire production timeline. Automated systems enable a streamlined workflow, from initial design and prototyping to final delivery. CNC machines and robotic handling systems allow swift reconfiguration, allowing us to adapt quickly to design changes or new client requirements.
This agility is particularly valuable in product development cycles where time to market can determine commercial success. Automated metal spinning reduces setup times and eliminates delays often associated with traditional tooling, making it an ideal choice for businesses that need efficient production at every stage.
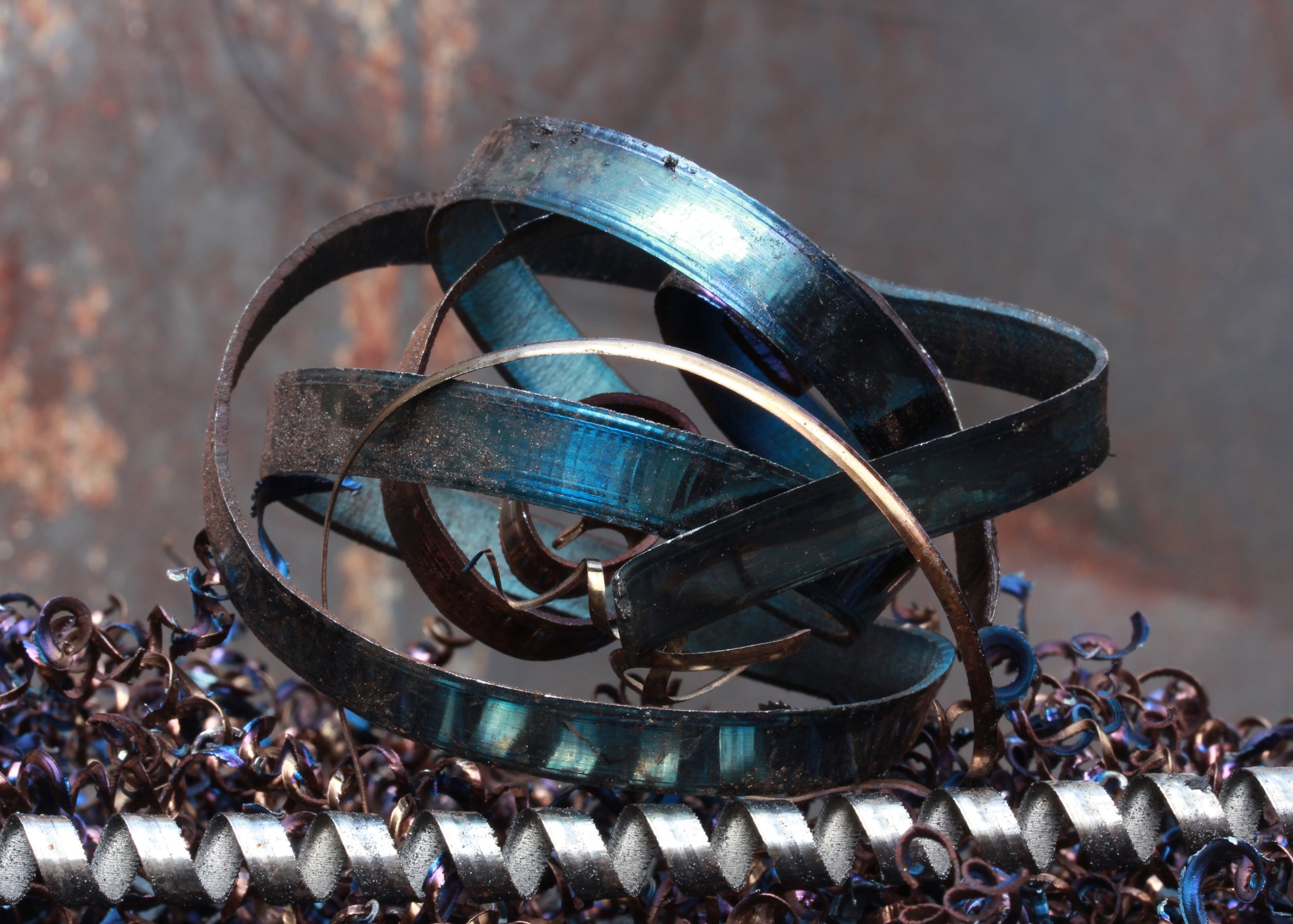
Supporting Sustainability Through Efficient Production
While automation delivers clear performance benefits, it also supports Tanfield’s commitment to sustainability. CNC spinning maximises material use by forming rather than cutting, significantly reducing the amount of scrap metal produced. Automated systems further enhance this efficiency by optimising material flow and limiting rework.
Additionally, modern machinery consumes less energy. Advanced programming helps reduce idle time, while robotics operate with high precision and minimal power requirements. These energy-saving practices lower both operational costs and environmental impact, aligning with broader goals for responsible manufacturing.
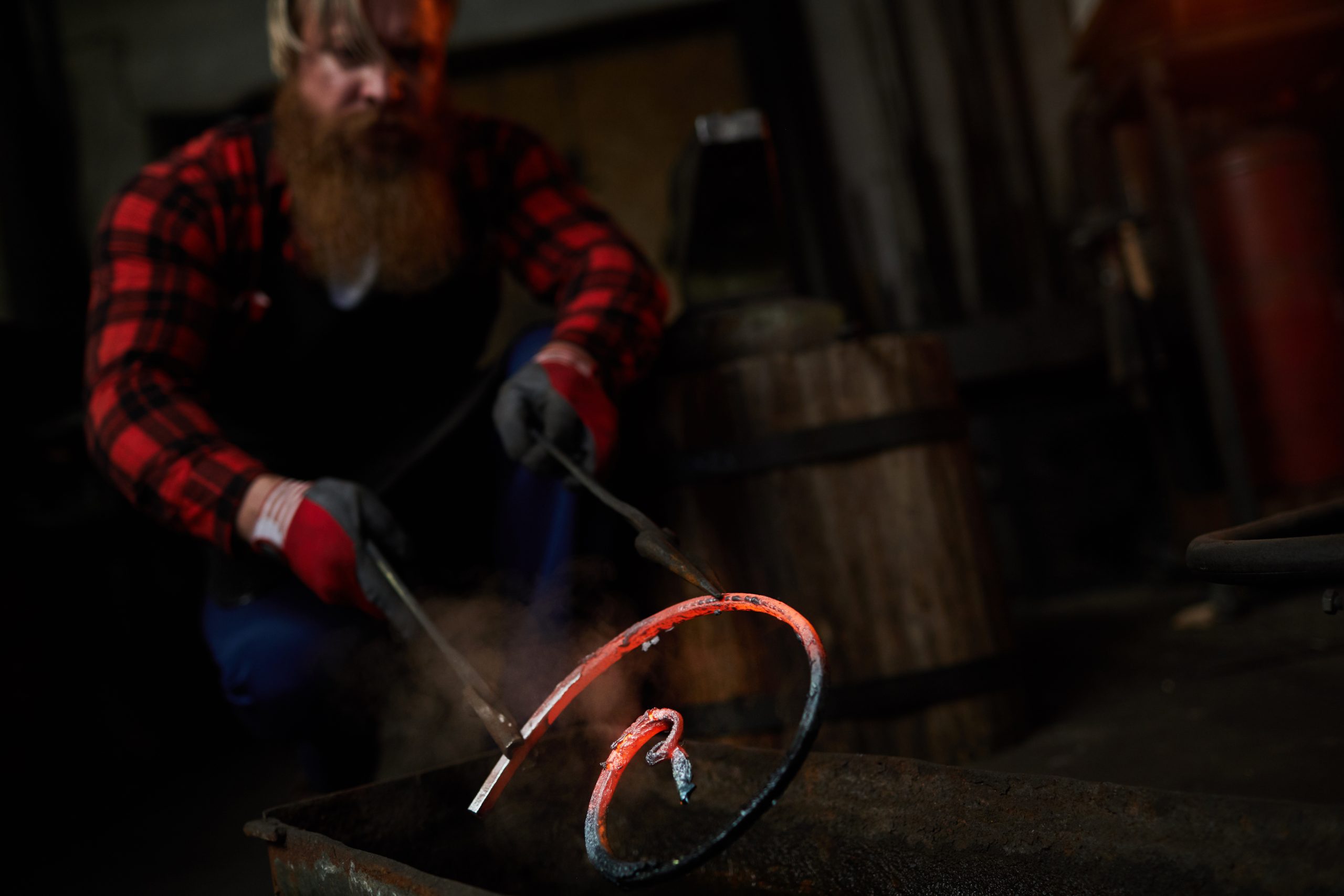
Industries That Benefit from Automated Metal Spinning
The benefits of automation extend across a wide range of industries. In aerospace, for example, automated spinning allows for the creation of lightweight, structurally robust components that meet strict safety standards. In automotive applications, manufacturers rely on CNC-spun parts for systems that require consistent tolerances and performance under pressure.
Other sectors, such as medical, architectural, and renewable energy, also depend on the precision and scalability that automation provides. At Tanfield, our fully automated capabilities enable us to serve these industries with tailored solutions that meet the most demanding technical requirements.
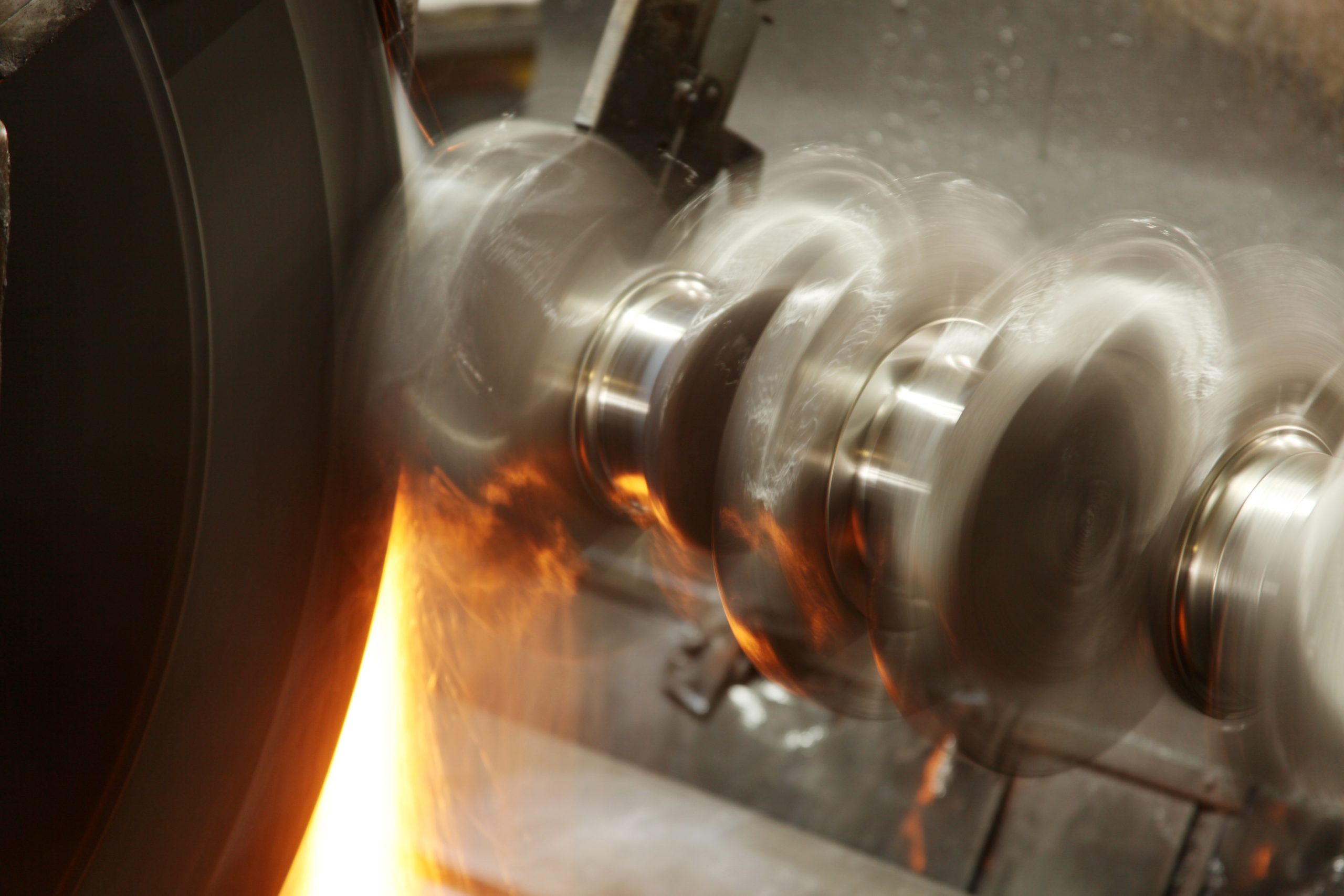
The Future of Fast, Precise, Scalable Metal Spinning
Automation is not a future aspiration; it is the engine driving modern manufacturing. In metal spinning, it offers a clear path to faster production, superior quality, and cost control. By integrating CNC technology, robotics, and smart monitoring tools, Tanfield Metal Spinners delivers outstanding results for clients who require precision, speed, and flexibility.
Whether your project involves high-volume orders or bespoke, complex geometries, our blend of skilled human and automated systems can meet the challenge. We invite you to explore how our advanced metal spinning services can accelerate your production schedule while maintaining the highest standards of craftsmanship and performance.
Contact Tanfield Metal Spinners today to discover how our automation capabilities can help bring your project to life.
Contact Us Today!
We encourage you to reach out to us today, our team of knowledgeable experts is ready to answer your questions, provide personalised guidance, and help you find the right solution for your needs.
Contact Us