Anodising, Electropolishing, and Pickling & Passivating
Benefits of Anodising, Electropolishing and Pickling & Passivating
Anodising, Electropolishing and Pickling & Passivating are an essential part of our treatment process for all spun products and provide a range of benefits for many of the sectors we work with.
Electropolishing
Electropolishing is an electrochemical process that removes a controlled amount of material from a metal surface to improve its finish, cleanliness, and corrosion resistance. It involves immersing the metal in an electrolyte bath and applying an electrical current to create a smooth and shiny surface.
Anodising
Anodising is an electrochemical process that forms a durable oxide layer on the surface of metals. This oxide layer enhances corrosion resistance, provides a decorative finish, and allows for the colouring of the metal. Anodising is commonly used in various industries, including aerospace and automotive, to improve the properties of aluminium components.
Pickling
Pickling is a chemical process used to remove surface impurities, contaminants, rust, scale, and oxides from metal surfaces. It involves immersing the metal in an acidic solution to clean and prepare it for subsequent treatments or processes.
Passivation
Passivation is a chemical process that follows pickling, primarily used for stainless steel and other corrosion-resistant alloys. It forms a protective passive oxide layer on the metal’s surface, enhancing its corrosion resistance and maintaining its integrity in harsh environments.
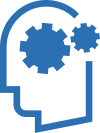
Expertise
We believe that collaboration is key! That’s why we work closely with you to ensure that we provide solutions tailored to your unique needs and requirements.
No drawing? No problem, our expert team will provide one free of charge.

Flexibility
Since 1984 we’ve built an enviable first-class reputation based on the highest quality workmanship with the best advice available on metal thickness and tolerance levels.
We have an open-minded approach to satisfying our customers engineering needs.

Responsive
We pride ourselves on deeply understanding our customers’ needs quickly and effectively. 90% of our quotes are provided within 24 hours.
We take great pride in our excellent on time deliver performance, helping our customers projects run on time, every time.
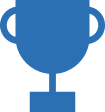
Competitive
With our large range of fully automatic spinning lathes, in our 35,000 sq-ft facility, you can be assured of receiving the best solution for your application, along with the very best lifetime value.
We are very proud to say we are a 100% ‘made in Great Britain’ manufacturer.
Top things we get asked
Anodising is an electrochemical process that enhances the natural oxide layer on the surface of aluminium and other metals. This process improves corrosion resistance, increases surface durability, and can add aesthetic value through colouring. It’s widely used in industries such as aerospace, architecture, and consumer electronics.
Anodizing is primarily used for aluminium and its alloys. While other metals like titanium and magnesium can also be anodized, aluminium is the most common due to its compatibility and effectiveness with this process.
An anodised surface is highly durable and resistant to wear, corrosion, and UV damage. The thickness of the anodised layer can be tailored to specific applications, with thicker coatings offering enhanced durability for industrial or outdoor use.
Anodising is used across many industries, including:
- Aerospace: Lightweight, corrosion-resistant parts.
- Construction: Architectural panels and fixtures.
- Automotive: Decorative trim and functional components.
- Consumer Goods: Electronics casings and home appliances.
Electropolishing is an electrochemical process that removes a thin layer of material from a metal surface to improve its smoothness, appearance, and corrosion resistance. The process involves immersing the part in an electrolyte solution and applying an electrical current, which dissolves surface imperfections at a microscopic level.
Pickling and passivating are chemical processes used to clean and protect stainless steel surfaces.
- Pickling removes surface impurities such as oxides, scale, and discoloration caused by welding or heat treatment.
- Passivating enhances the natural oxide layer on stainless steel, improving corrosion resistance.