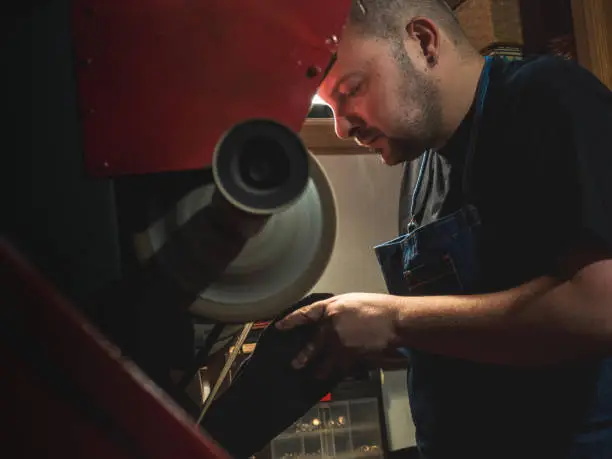
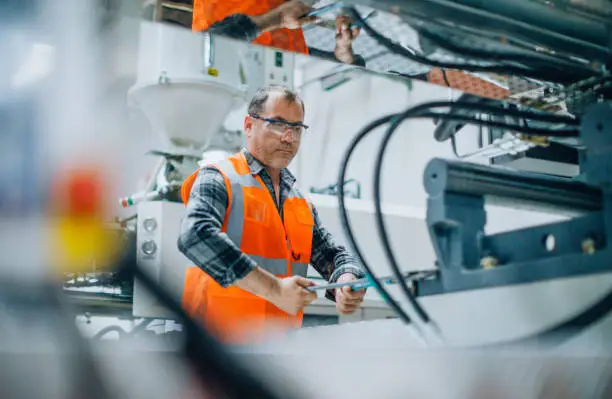
A Guide to Metal Finishing: Enhancing Quality and Durability
Metal finishing is a critical step in manufacturing, transforming raw metal into high-quality components with enhanced durability and aesthetic appeal. At Tanfield Metal Spinners, our metal finishing ensures that every product meets strict quality and performance standards. This guide provides an overview of metal finishing techniques, their benefits, and how to choose the best option for various applications.
What is Metal Finishing?
Metal finishing encompasses various techniques that modify the surface of metal products to improve appearance, durability, and functionality. The process often includes cleaning, polishing, coating, or texturing to enhance qualities like corrosion resistance, electrical conductivity, and scratch resistance. In some cases, metal finishing involves altering the metal’s molecular structure to increase strength and resilience.
Metal finishing adds value across industries, from improving the longevity of components in harsh environments to creating an attractive finish for consumer products. At Tanfield Metal Spinners, we specialise in a range of high-quality finishing techniques tailored to meet our clients’ specific requirements.
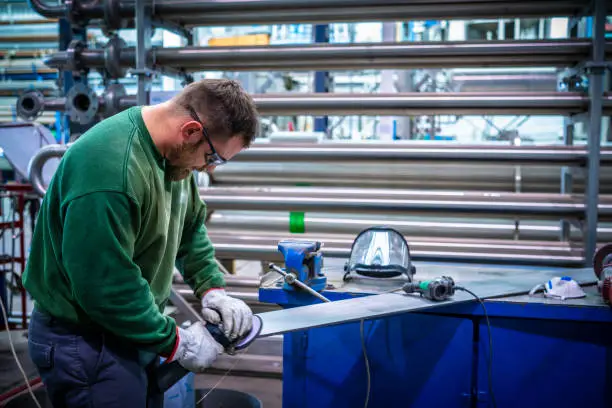
Why Metal Finishing Matters
Metal, though durable, remains susceptible to wear, corrosion, and environmental damage. Metal finishing helps mitigate these issues, providing essential benefits such as:
- Enhanced Durability: Techniques like plating and anodising increase resistance to corrosion and abrasion, extending a product’s lifespan.
- Improved Aesthetics: Polished or coated finishes add visual appeal, especially for consumer products where appearance is vital.
- Functional Properties: Certain finishes improve functionality, such as conductivity in electrical applications or ease of cleaning in the food industry.
- Cost-Effectiveness: By enhancing durability, finishing reduces the need for replacement parts, offering a cost-effective solution for industries dependent on high-performance components.
A clear understanding of different metal finishing types helps select the best method for each application.
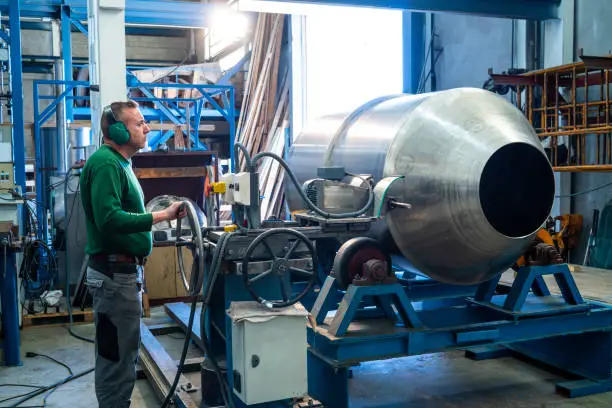
Types of Metal Finishing Processes
Metal finishing includes a variety of techniques, each offering unique benefits based on the material and desired outcome. Here’s an overview of some common metal finishing processes:
1. Plating
Plating coats a metal surface with a thin layer of another metal, enhancing properties like corrosion resistance, surface hardness, and appearance. Plating is common in electronics, automotive, and aerospace applications that require increased durability.
- Electroplating: Involves submerging the metal component in a bath of metal ions and applying an electric current to bond ions to the surface. This method provides precise, even coating.
- Electroless Plating: This uses a chemical reaction instead of electricity to deposit the coating, ideal for complex shapes where consistent coverage is necessary.
- Hot Dip Galvanising: Dips the metal into molten zinc, creating a protective zinc-iron alloy layer. This method is popular for steel parts exposed to outdoor environments.
2. Anodising
Anodising is an electrochemical process primarily used for aluminium. The metal is placed in an acid electrolyte bath, and an electric current forms a corrosion-resistant oxide layer on the surface. Anodising is common in architectural and electronics applications, providing both durability and a range of colour options.
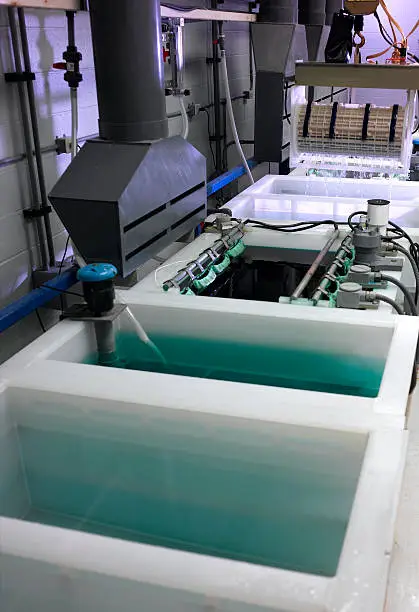
3. Powder Coating
Powder coating uses electrostatically charged powder to cover the metal surface, which is then heated to create a smooth, hard coating. This eco-friendly process offers resistance against chipping and fading, making it ideal for the automotive, appliance, and outdoor furniture industries.
4. Polishing and Buffing
Polishing and buffing smooth the metal surface, often creating a mirror-like shine. Polishing enhances appearance and surface cleanliness, which is essential in industries like food processing and pharmaceuticals. Buffing is commonly used to achieve high gloss on metals such as stainless steel and aluminium.
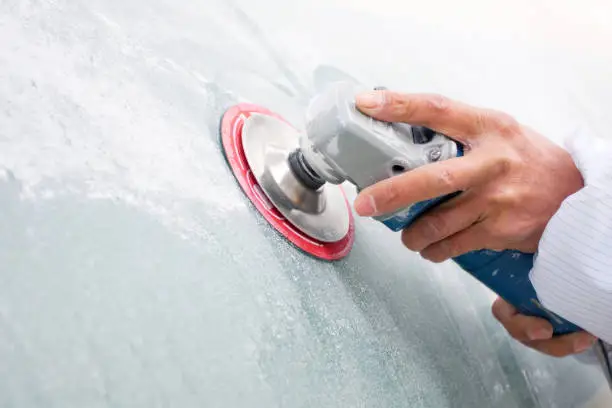
5. Electropolishing
Electropolishing removes metal ions from the surface, creating a smooth, clean finish that resists corrosion. This process suits medical and laboratory equipment, where cleanliness and durability are critical. Electropolishing also deburrs the metal surface, removing microscopic imperfections for a refined finish.
6. Grinding
Grinding uses abrasive wheels to remove material from the metal surface, preparing it for further finishing processes or removing imperfections. Grinding is effective for smoothing rough welds or preparing surfaces for painting or coating.
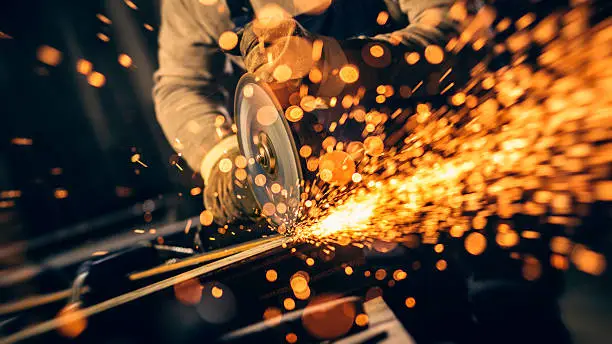
7. Blasting
Blasting uses high-pressure abrasive materials to clean and smooth the metal surface, creating a matte or textured finish. Blasting is often used as a preparatory step before other finishing processes, such as painting or powder coating, to improve adhesion.
8. Painting and Coating
Painting, one of the most versatile and cost-effective finishing techniques, provides a protective layer that can be customised in various colours. Powder coating, a more durable alternative to wet paint, uses powder and electrostatic charges instead of liquid paint, offering enhanced durability.
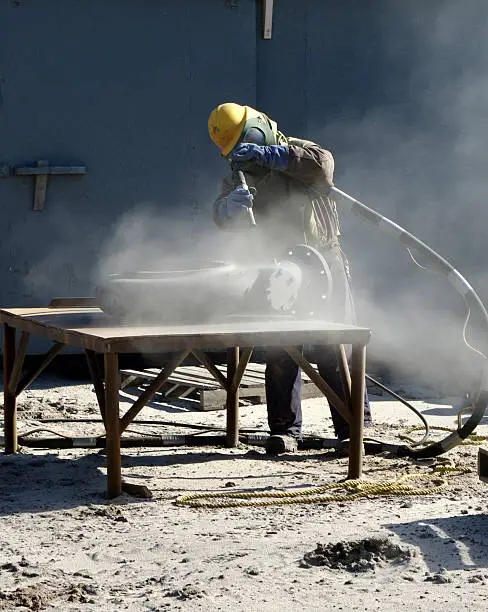
Choosing the Right Metal Finishing Process
Selecting a metal finishing technique involves considering factors like metal type, appearance, functionality, and budget. Here’s what to evaluate when choosing a finishing process:
- Material Compatibility: Certain metals respond better to specific finishes. Anodising works well for aluminium, while galvanising is typically used for steel.
- Durability Requirements: For products exposed to harsh conditions, methods like hot dip galvanising or powder coating provide excellent resistance to corrosion and wear.
- Aesthetic Preferences: Polishing or painting can enhance the visual appeal of metal products, making them suitable for consumer-facing items.
- Cost and Efficiency: Finishing techniques vary in cost. Powder coating and painting are generally more affordable, while high-precision methods like electroplating offer superior consistency but may cost more.
Applications of Metal Finishing
Metal finishing is integral to various industries, each benefiting from the unique advantages of different finishes. Common applications include:
- Automotive: Powder coating, plating, and anodising provide durable surfaces for parts exposed to weather and mechanical stress.
- Electronics: Plating and electropolishing enhance conductivity and corrosion resistance, extending the lifespan of electronic components.
- Food and Beverage: Polished finishes improve hygiene and ease of cleaning for food processing equipment.
- Architecture: Anodised aluminium offers durability and aesthetic options, making it a popular choice in architectural applications.
- Medical Equipment: Electropolishing produces smooth, hygienic surfaces that meet stringent regulatory standards for medical devices.
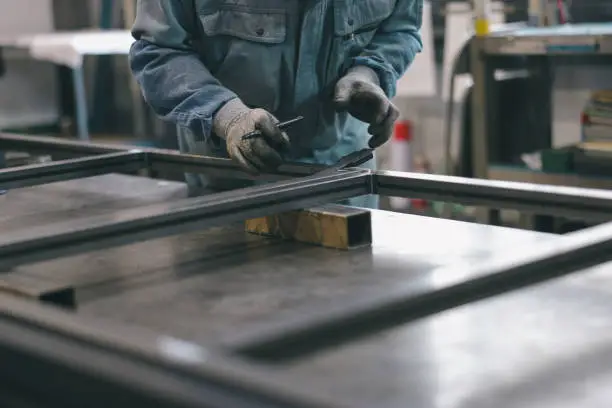
Elevating Metal Quality and Performance with Expert Finishing
Metal finishing enhances the value, functionality, and aesthetics of metal components across various industries. Techniques like plating, anodising, polishing, and powder coating each offer distinct advantages tailored to specific applications.
Tanfield Metal Spinners provides high-quality finishing solutions that meet strict performance and visual standards, helping clients achieve lasting quality and durability. Our team ensures that every component meets ISO 9001 quality standards and undergoes rigorous quality control checks. Advanced machinery allows us to handle complex finishing processes with precision, ensuring consistent, high-quality results.
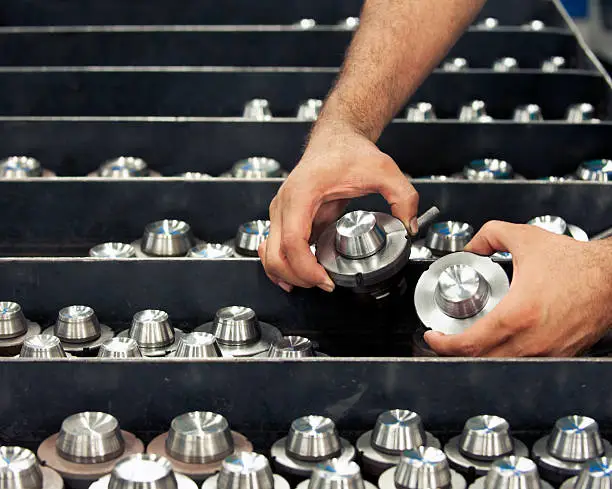
For more information or to discuss your metal finishing needs, contact Tanfield Metal Spinners today. Our team is ready to help you select the ideal finishing technique to achieve the perfect result for your project.