Fabrication and Welding Services
Our Fabrication Process
When it comes to sheet metal fabrication, we start with a technical review of the design. As with everything we do here at Tanfield, we work collaboratively to ensure our customers are getting the best results. The initial review helps us assign the correct tools, skills, and machinery to complete the project work.
It’s then passed on to our fabrication team who utilise the relevant techniques to execute the design to the design specifications. Our metal fabrication manufacturing process typically consists of multiple steps, the exact number of which will vary depending on the nature of the project.
Tanfield concludes all our fabrication and welding processes by checking products are certified to BSEN 1090. After this, the products can be signed off and delivered to you the following day.
What Fabrication and Welding Can Do For You
Industrial metal fabrication and welding is used extensively by companies focused on core processes. Here, our services can be used to create vital parts such as pressure vessels, containers, machine components, and more.
Tanfield Metal Spinners puts its fabrication expertise to use by offering a service that can produce a huge variety of metal fabricated parts. On top of this, we can shape different materials where finished products require certain properties. These decisions are informed by the extensive materials knowledge possessed by our fabricators and welders.
Tanfield have a proven track record of executing fabrication projects for the agriculture, food manufacturing, cryogenic, air movement, and safety industries. If you belong to one of these industries and you’re looking for metal fabricators near me, look no further than us.
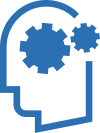
Expertise
We believe that collaboration is key! That’s why we work closely with you to ensure that we provide solutions tailored to your unique needs and requirements.
No drawing? No problem, our expert team will provide one free of charge.

Flexibility
Since 1984 we’ve built an enviable first-class reputation based on the highest quality workmanship with the best advice available on metal thickness and tolerance levels.
We have an open-minded approach to satisfying our customers engineering needs.

Responsive
We pride ourselves on deeply understanding our customers’ needs quickly and effectively. 90% of our quotes are provided within 24 hours.
We take great pride in our excellent on time deliver performance, helping our customers projects run on time, every time.
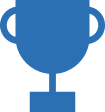
Competitive
With our large range of fully automatic spinning lathes, in our 35,000 sq-ft facility, you can be assured of receiving the best solution for your application, along with the very best lifetime value.
We are very proud to say we are a 100% ‘made in Great Britain’ manufacturer.
Top things we get asked
Metal fabrication is a multi-step manufacturing process used to shape raw metal into finished products or components. This process includes various techniques such as cutting, bending, forming, welding, machining, and assembling. Metal fabrication can be applied to a wide range of metals, including steel, aluminium, copper, and brass. The process typically starts with design and engineering phases, where specifications are established, followed by fabrication and finishing.
The choice of metal depends on the application’s requirements, common metals include:
- Steel: The most widely used metal due to its strength, versatility, and cost-efficiency. Types include carbon steel stainless steel, and alloy steel
- Aluminium: Known for being lightweight, corrosion-resistant, and easy to work with. Commonly used in aerospace, automotive, and consumer products.
- Copper: Valued for its excellent conductivity and corrosion resistance, making it ideal for electrical and plumbing applications.
- Brass: An alloy of copper and zinc, brass is durable, corrosion-resistant, and has an attractive finish, often used for fittings and decorative elements.
- Titanium: Exceptionally strong and lightweight, titanium is used in high-performance applications like aerospace, medical implants, and sporting goods.
Metal fabrication is used in a wide range of industries due to its versatility, cost-effectiveness, and ability to produce strong, seamless, and precise parts. Some key industries include:
- Aerospace
- Automotive
- Medical
- Food and Beverage
- HVAC (Heating, Ventilation, and Air Conditioning)
- Defense and Military
- Renewable Energy
- Architectural and Lighting
- Marine
- Electronics
- Industrial Equipment
Metal spinning is favoured in these industries for its ability to create durable, seamless, and high-precision parts while minimising waste and reducing costs compared to other fabrication methods.
The timeline for a metal fabrication project varies widely depending on the complexity, size, and scope. For simple projects like cutting and bending basic parts, the process can take a few days. More complex projects involving custom design, welding, machining, and assembly may take several weeks. Factors like material availability, design revisions, and the need for specialised finishes can also impact lead times. Clear communication with the fabricator during the planning phase helps set realistic expectations.
There are several factors influence the cost of a metal fabrication project, these are:
- Material – The type, quality, and thickness of the metal. Specialised metals like titanium or stainless steel are more expensive than carbon steel.
- Design Complexity – Intricate designs or tight tolerances require more time and specialised equipment.
- Labor – Skilled labour for processes like welding or machining adds to costs.
- Quantity – Higher production volumes can reduce the per-unit cost due to efficiencies in batch processing.
- Finishing – Coatings, paint, and treatments like galvanisation add to the cost.
- Machinery Use – Processes like laser cutting or CNC machining may involve higher costs for setup and operation.
The primary metal fabrication techniques are:
- Cutting, which is when you use methods like laser cutting, water jet cutting, or plasma cutting.
- Bending, where you use press brakes or rollers to shape metal.
- Welding, where you fuse metals using heat.
- Machining, which is milling, drilling, or turning with CNC machines.
- Assembling, which is where you join components with fasteners or adhesives.