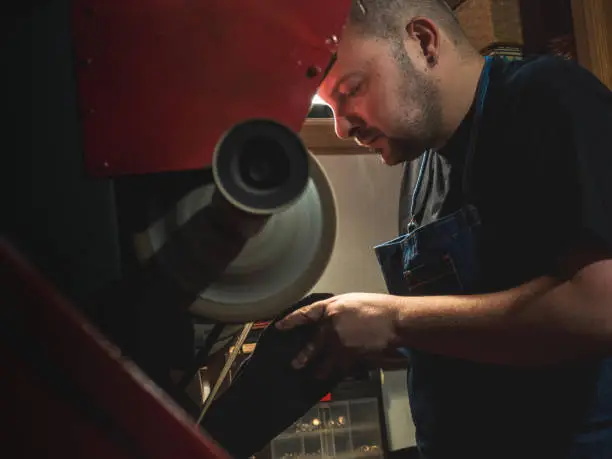
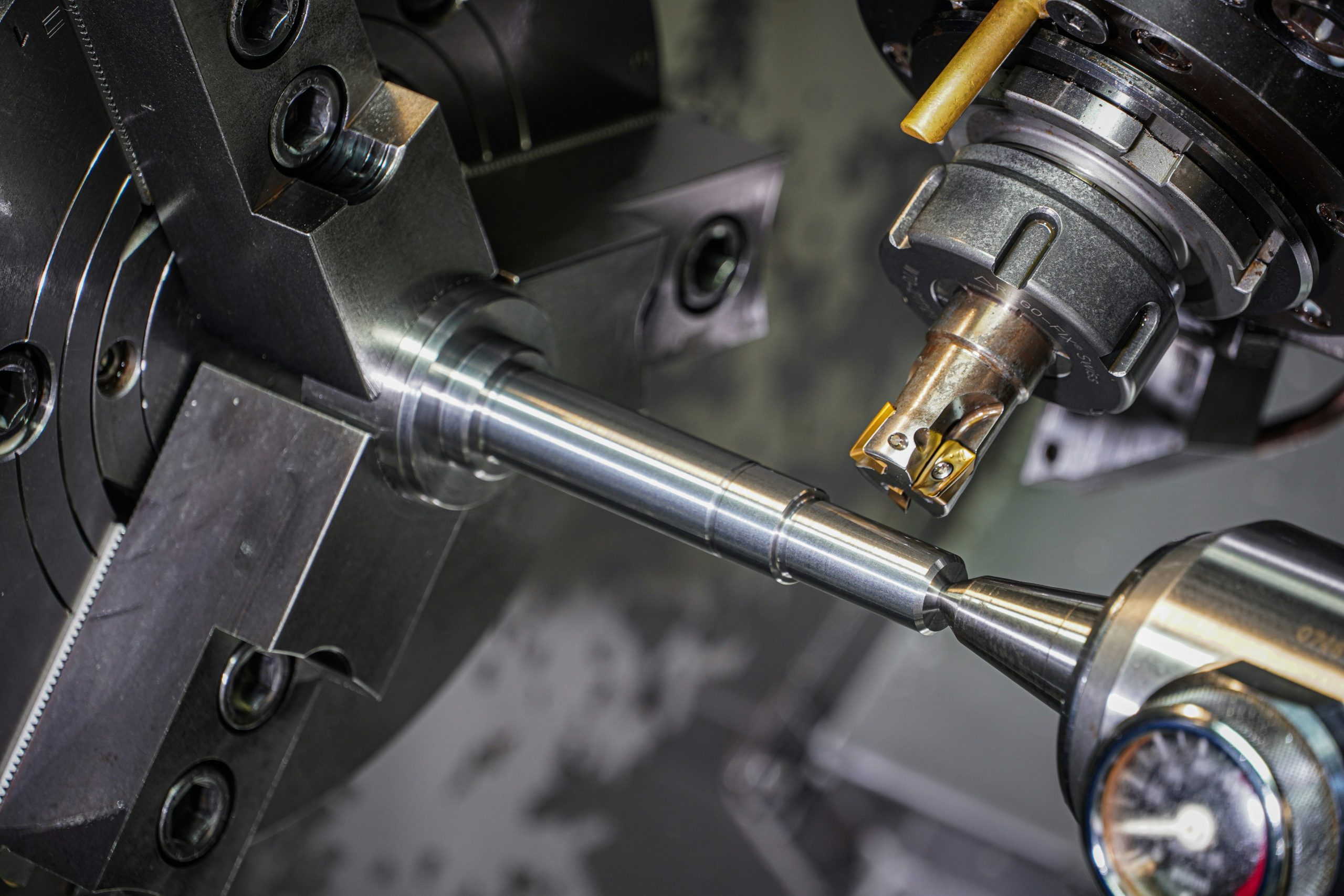
Exploring the history of metal spinning
Nowadays, metal spinning is a precision cold forming technique which has wide reaching applications in a variety of industries. This wasn’t always the case. Although the metal spinning process was revolutionary from its inception, it has undergone many developments over its long history. In this article, we examine how the metal spinning process has changed over hundreds of years. This allows us to trace a timeline to where we are now, with CNC metal spinning machines and massive tooling capabilities.
Summary of metal spinning
In its most basic form, metal spinning is a metal forming process that takes a sheet metal blank and transforms it into a symmetrical conical or cylindrical shape. Rollers use force to shape the metal without the need for heating. Today, many metal spinners make use of machinery to help rotate and hold workpieces in place, although a great deal of skill is still required from the spinner themselves. Tools are created to form parts of certain sizes and thicknesses, with the blank taking on the shape of the tool during the spinning process. The work is always done according to pre-determined tolerances.
Read about the ‘Factors affecting the tolerance of metal spun parts’ for more insight.
Origins of metal spinning
The first known evidence of what we would recognise a metal spinning comes from 4th century illustrations discovered in Egypt. These depicted two men operating a wooden spinning lathe, which consisted of a ‘bow-like’ instrument. It was also found that metal spinning of copper, stone, and wood was an established practice in India and China around this time. Due to technology restraints, these were likely the only materials that could be formed with the metal spinning process.
Medieval metal spinning
In the middle ages, there came many developments in the approach to spinning metal. One of the most significant was the introduction of a pedal which allowed for the continuous rotation of the material, similar to how an old swing machine runs. This development gave the craftsman free use of his hands to apply force to the material while at the same time controlling the speed of the rotation. These new lathes were also more compact, allowing just one worker to sit at their station and complete their metal spinning duties.
Impact of the industrial revolution
The 18th and 19th centuries saw countless developments, new technologies, and new techniques thanks to the adoption of fossil fuels during the industrial revolution. It was at this time that the metal spinning lathe as we know it was created. This framework allowed for the continuous rotation of a metal workpiece without the need for human intervention. The result was that metal spinning was now able to create precise metal spun parts that were uniform. In other words, metal spinning became a reliable option for mass production.
Rise of computer control metal spinning
As the 20th century progressed, more industries started adopting metal spinning as a key manufacturing process. Crucially, this included Aerospace, food production, and safety industries to name a few. Improvements meant that metal spinning could create larger and more complex parts. This expanded the scope of applications for the process while maintaining its repeatability. Metal spinners also began adopting complimentary techniques and approaches, such as using hydraulic metal pressing, automated metal fabrication, and modern metal finishings.
It was then in the 1960’s and 1970’s that the first CN and CNC machines for metal spinning were developed. This greatly increased the efficiency of the technique, as it allowed aspects of the process, such as the spin speed and deformation depth, to be changed quickly through pre-set commands.
Partner with modern metal spinning company
Metal spinning didn’t become the cost-effective, precise, flexible, and highly repeatable process it is overnight. The history or metal spinning shows us the key developments that have led to its many benefits. At Tanfield Metal Spinners, we are proud to be positioned at the forefront of the UK metal spinning industry, with the largest tooling stock across Europe. Our team use their expertise in tandem with modern technology to achieve the best results for clients. Get in touch to discuss your project requirements.