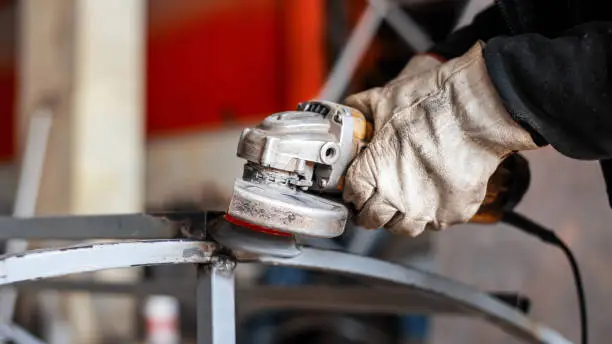
The Metal Polishing Process: Achieving Precision and Excellence with Tanfield Metal Spinners
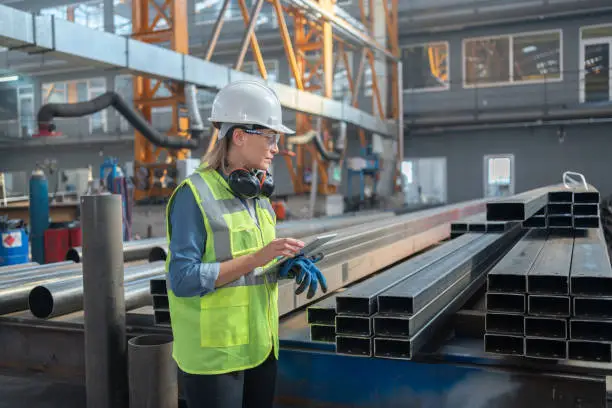
When it comes to manufacturing, particularly ‘lean manufacturing’, high waste levels are often an indicator of inefficient processes. For businesses, this represents untapped potential and unnecessary costs. Metal spinning typically produces very little waste, especially when compared to hot forming techniques. This post is designed to teach you what the telltale signs of waste in manufacturing look like, along with how incorporating metal spinning into operations can help reduce inefficiencies that lead to waste.
Identifying and eliminating waste is vital to sustainable manufacturing practices. By addressing areas of waste, metal spinning companies can reduce their environmental impact and improve overall operational efficiency.
Efficient waste management in manufacturing is not just about reducing costs; it also plays a crucial role in conserving resources and minimising environmental impact. Companies that prioritise waste reduction often find themselves at the forefront of sustainable manufacturing practices, setting an example for the industry as a whole.
When core manufacturing processes involve excessive material waste, it not only depletes valuable resources but also increases manufacturing costs. Implementing tighter quality control measures and optimising designs can help minimise material waste.
Energy-intensive manufacturing processes, coupled with inefficient machinery, can significantly contribute to waste. By regularly assessing and upgrading machinery, manufacturers can improve energy utilisation and reduce wastage.
Streamlining the metal spinning workflow by eliminating unnecessary process steps can help reduce cycle time and resource consumption. By conducting thorough process evaluations, manufacturers can identify redundant steps and optimize production.
Moreover, waste reduction efforts in manufacturing can lead to enhanced product quality and customer satisfaction. By focusing on eliminating waste, companies can improve the consistency and reliability of their products, ultimately building a stronger reputation in the market.
Firstly, metal spinning is a cold forming process. The creation of metal spun products does not require the metal to be heated. This constant heating requires a massive amount of energy input, with excess heat and smoke often being given off as waste products. Furthermore, metal spinning produces very little material waste as the entire blank is used for shaping. The only waste comes from the sheet metal offcuts that are created when the blanks are initially cut. Finally, the large scale repeatability of metal spinning allows for easier inventory management.
General advice for reducing lean manufacturing waste can include:
Many metal fabrication companies are only focused on how much they can deliver. At Tanfield Metal Spinners, we are constantly striving to improve our processes to support manufacturing efforts. Through our team’s expertise, we can advise on how our metal spinning services can slot into your overall production process. This might mean recommending certain techniques, such as metal swaging, pressing, or metal finishings to reduce manufacturing waste. Get in touch today to chat about your project requirements.